0001421461false2021FYhttp://fasb.org/us-gaap/2021-01-31#OtherLiabilitiesCurrenthttp://fasb.org/us-gaap/2021-01-31#OtherLiabilitiesCurrenthttp://fasb.org/us-gaap/2021-01-31#OtherLiabilitiesCurrenthttp://fasb.org/us-gaap/2021-01-31#OtherLiabilitiesCurrent00014214612021-01-012021-12-3100014214612021-06-30iso4217:USD00014214612022-02-28xbrli:shares00014214612021-12-3100014214612020-12-31iso4217:USDxbrli:shares0001421461us-gaap:MineralMember2021-01-012021-12-310001421461us-gaap:MineralMember2020-01-012020-12-310001421461us-gaap:MineralMember2019-01-012019-12-310001421461us-gaap:CargoAndFreightMember2021-01-012021-12-310001421461us-gaap:CargoAndFreightMember2020-01-012020-12-310001421461us-gaap:CargoAndFreightMember2019-01-012019-12-310001421461ipi:WarehouseandHandlingMember2021-01-012021-12-310001421461ipi:WarehouseandHandlingMember2020-01-012020-12-310001421461ipi:WarehouseandHandlingMember2019-01-012019-12-3100014214612020-01-012020-12-3100014214612019-01-012019-12-310001421461us-gaap:CommonStockMember2018-12-310001421461us-gaap:AdditionalPaidInCapitalMember2018-12-310001421461us-gaap:RetainedEarningsMember2018-12-3100014214612018-12-310001421461us-gaap:RetainedEarningsMember2019-01-012019-12-310001421461us-gaap:AdditionalPaidInCapitalMember2019-01-012019-12-310001421461us-gaap:CommonStockMember2019-01-012019-12-310001421461us-gaap:CommonStockMember2019-12-310001421461us-gaap:AdditionalPaidInCapitalMember2019-12-310001421461us-gaap:RetainedEarningsMember2019-12-3100014214612019-12-310001421461us-gaap:RetainedEarningsMember2020-01-012020-12-310001421461us-gaap:AdditionalPaidInCapitalMember2020-01-012020-12-310001421461us-gaap:CommonStockMember2020-01-012020-12-310001421461us-gaap:CommonStockMember2020-12-310001421461us-gaap:AdditionalPaidInCapitalMember2020-12-310001421461us-gaap:RetainedEarningsMember2020-12-310001421461us-gaap:RetainedEarningsMember2021-01-012021-12-310001421461us-gaap:AdditionalPaidInCapitalMember2021-01-012021-12-310001421461us-gaap:CommonStockMember2021-01-012021-12-310001421461us-gaap:CommonStockMember2021-12-310001421461us-gaap:AdditionalPaidInCapitalMember2021-12-310001421461us-gaap:RetainedEarningsMember2021-12-31ipi:Facilityipi:Reporting_Segments00014214612020-08-1000014214612020-08-102020-08-10xbrli:pure00014214612020-08-140001421461us-gaap:RestrictedStockMember2021-01-012021-12-310001421461us-gaap:RestrictedStockMember2020-01-012020-12-310001421461us-gaap:RestrictedStockMember2019-01-012019-12-310001421461us-gaap:EmployeeStockOptionMember2021-01-012021-12-310001421461us-gaap:EmployeeStockOptionMember2020-01-012020-12-310001421461us-gaap:EmployeeStockOptionMember2019-01-012019-12-310001421461us-gaap:LandMember2021-12-310001421461us-gaap:LandMember2020-12-310001421461us-gaap:LandImprovementsMember2021-12-310001421461us-gaap:LandImprovementsMember2020-12-310001421461us-gaap:MiningPropertiesAndMineralRightsMember2021-12-310001421461us-gaap:MiningPropertiesAndMineralRightsMember2020-12-310001421461us-gaap:BuildingAndBuildingImprovementsMember2021-12-310001421461us-gaap:BuildingAndBuildingImprovementsMember2020-12-310001421461us-gaap:MachineryAndEquipmentMember2021-12-310001421461us-gaap:MachineryAndEquipmentMember2020-12-310001421461us-gaap:VehiclesMember2021-12-310001421461us-gaap:VehiclesMember2020-12-310001421461us-gaap:OfficeEquipmentMember2021-12-310001421461us-gaap:OfficeEquipmentMember2020-12-310001421461ipi:RightOfUseAssetsMember2021-12-310001421461ipi:RightOfUseAssetsMember2020-12-310001421461us-gaap:BreedingAndProductionAnimalsMember2021-12-310001421461us-gaap:BreedingAndProductionAnimalsMember2020-12-310001421461us-gaap:ConstructionInProgressMember2021-12-310001421461us-gaap:ConstructionInProgressMember2020-12-310001421461us-gaap:PropertyPlantAndEquipmentMember2021-12-310001421461us-gaap:PropertyPlantAndEquipmentMember2020-12-310001421461us-gaap:OtherNoncurrentLiabilitiesMember2021-12-310001421461us-gaap:OtherNoncurrentLiabilitiesMember2020-12-3100014214612019-05-012019-05-310001421461us-gaap:RoyaltyAgreementsMember2021-12-310001421461us-gaap:RoyaltyAgreementsMember2020-12-310001421461us-gaap:UseRightsMember2021-12-310001421461us-gaap:UseRightsMember2020-12-310001421461us-gaap:LondonInterbankOfferedRateLIBORMembersrt:MinimumMember2021-01-012021-12-310001421461us-gaap:LondonInterbankOfferedRateLIBORMembersrt:MaximumMember2021-01-012021-12-310001421461ipi:PaycheckProtectionProgramLoanMember2020-04-012020-04-300001421461ipi:PaycheckProtectionProgramLoanMember2021-06-012021-06-300001421461ipi:SeriesBSeniorNotesMember2021-06-012021-06-300001421461ipi:SeriesBSeniorNotesMember2020-12-310001421461srt:MinimumMemberus-gaap:MeasurementInputRiskFreeInterestRateMember2021-12-310001421461srt:MaximumMemberus-gaap:MeasurementInputRiskFreeInterestRateMember2021-12-310001421461ipi:PotashMemberipi:PotashMember2021-01-012021-12-310001421461ipi:TrioMemberipi:PotashMember2021-01-012021-12-310001421461ipi:OilFieldServicesMemberipi:PotashMember2021-01-012021-12-310001421461ipi:PotashMemberus-gaap:IntersegmentEliminationMember2021-01-012021-12-310001421461ipi:PotashMember2021-01-012021-12-310001421461ipi:PotashMemberipi:TrioMember2021-01-012021-12-310001421461ipi:TrioMemberipi:TrioMember2021-01-012021-12-310001421461ipi:OilFieldServicesMemberipi:TrioMember2021-01-012021-12-310001421461ipi:TrioMemberus-gaap:IntersegmentEliminationMember2021-01-012021-12-310001421461ipi:TrioMember2021-01-012021-12-310001421461ipi:PotashMemberipi:WaterProductMember2021-01-012021-12-310001421461ipi:TrioMemberipi:WaterProductMember2021-01-012021-12-310001421461ipi:OilFieldServicesMemberipi:WaterProductMember2021-01-012021-12-310001421461ipi:WaterProductMemberus-gaap:IntersegmentEliminationMember2021-01-012021-12-310001421461ipi:WaterProductMember2021-01-012021-12-310001421461ipi:SaltMemberipi:PotashMember2021-01-012021-12-310001421461ipi:TrioMemberipi:SaltMember2021-01-012021-12-310001421461ipi:OilFieldServicesMemberipi:SaltMember2021-01-012021-12-310001421461ipi:SaltMemberus-gaap:IntersegmentEliminationMember2021-01-012021-12-310001421461ipi:SaltMember2021-01-012021-12-310001421461ipi:MagnesiumChlorideMemberipi:PotashMember2021-01-012021-12-310001421461ipi:TrioMemberipi:MagnesiumChlorideMember2021-01-012021-12-310001421461ipi:OilFieldServicesMemberipi:MagnesiumChlorideMember2021-01-012021-12-310001421461ipi:MagnesiumChlorideMemberus-gaap:IntersegmentEliminationMember2021-01-012021-12-310001421461ipi:MagnesiumChlorideMember2021-01-012021-12-310001421461ipi:PotashMemberipi:BrinesMember2021-01-012021-12-310001421461ipi:TrioMemberipi:BrinesMember2021-01-012021-12-310001421461ipi:OilFieldServicesMemberipi:BrinesMember2021-01-012021-12-310001421461ipi:BrinesMemberus-gaap:IntersegmentEliminationMember2021-01-012021-12-310001421461ipi:BrinesMember2021-01-012021-12-310001421461ipi:PotashMemberus-gaap:ProductAndServiceOtherMember2021-01-012021-12-310001421461ipi:TrioMemberus-gaap:ProductAndServiceOtherMember2021-01-012021-12-310001421461ipi:OilFieldServicesMemberus-gaap:ProductAndServiceOtherMember2021-01-012021-12-310001421461us-gaap:IntersegmentEliminationMemberus-gaap:ProductAndServiceOtherMember2021-01-012021-12-310001421461us-gaap:ProductAndServiceOtherMember2021-01-012021-12-310001421461ipi:PotashMemberus-gaap:MineralMember2021-01-012021-12-310001421461ipi:TrioMemberus-gaap:MineralMember2021-01-012021-12-310001421461ipi:OilFieldServicesMemberus-gaap:MineralMember2021-01-012021-12-310001421461us-gaap:IntersegmentEliminationMember2021-01-012021-12-310001421461ipi:PotashMemberipi:PotashMember2020-01-012020-12-310001421461ipi:TrioMemberipi:PotashMember2020-01-012020-12-310001421461ipi:OilFieldServicesMemberipi:PotashMember2020-01-012020-12-310001421461ipi:PotashMemberus-gaap:IntersegmentEliminationMember2020-01-012020-12-310001421461ipi:PotashMember2020-01-012020-12-310001421461ipi:PotashMemberipi:TrioMember2020-01-012020-12-310001421461ipi:TrioMemberipi:TrioMember2020-01-012020-12-310001421461ipi:OilFieldServicesMemberipi:TrioMember2020-01-012020-12-310001421461ipi:TrioMemberus-gaap:IntersegmentEliminationMember2020-01-012020-12-310001421461ipi:TrioMember2020-01-012020-12-310001421461ipi:PotashMemberipi:WaterProductMember2020-01-012020-12-310001421461ipi:TrioMemberipi:WaterProductMember2020-01-012020-12-310001421461ipi:OilFieldServicesMemberipi:WaterProductMember2020-01-012020-12-310001421461ipi:WaterProductMemberus-gaap:IntersegmentEliminationMember2020-01-012020-12-310001421461ipi:WaterProductMember2020-01-012020-12-310001421461ipi:SaltMemberipi:PotashMember2020-01-012020-12-310001421461ipi:TrioMemberipi:SaltMember2020-01-012020-12-310001421461ipi:OilFieldServicesMemberipi:SaltMember2020-01-012020-12-310001421461ipi:SaltMemberus-gaap:IntersegmentEliminationMember2020-01-012020-12-310001421461ipi:SaltMember2020-01-012020-12-310001421461ipi:MagnesiumChlorideMemberipi:PotashMember2020-01-012020-12-310001421461ipi:TrioMemberipi:MagnesiumChlorideMember2020-01-012020-12-310001421461ipi:OilFieldServicesMemberipi:MagnesiumChlorideMember2020-01-012020-12-310001421461ipi:MagnesiumChlorideMemberus-gaap:IntersegmentEliminationMember2020-01-012020-12-310001421461ipi:MagnesiumChlorideMember2020-01-012020-12-310001421461ipi:PotashMemberipi:BrinesMember2020-01-012020-12-310001421461ipi:TrioMemberipi:BrinesMember2020-01-012020-12-310001421461ipi:OilFieldServicesMemberipi:BrinesMember2020-01-012020-12-310001421461ipi:BrinesMemberus-gaap:IntersegmentEliminationMember2020-01-012020-12-310001421461ipi:BrinesMember2020-01-012020-12-310001421461ipi:PotashMemberus-gaap:ProductAndServiceOtherMember2020-01-012020-12-310001421461ipi:TrioMemberus-gaap:ProductAndServiceOtherMember2020-01-012020-12-310001421461ipi:OilFieldServicesMemberus-gaap:ProductAndServiceOtherMember2020-01-012020-12-310001421461us-gaap:IntersegmentEliminationMemberus-gaap:ProductAndServiceOtherMember2020-01-012020-12-310001421461us-gaap:ProductAndServiceOtherMember2020-01-012020-12-310001421461ipi:PotashMemberus-gaap:MineralMember2020-01-012020-12-310001421461ipi:TrioMemberus-gaap:MineralMember2020-01-012020-12-310001421461ipi:OilFieldServicesMemberus-gaap:MineralMember2020-01-012020-12-310001421461us-gaap:IntersegmentEliminationMember2020-01-012020-12-310001421461ipi:PotashMemberipi:PotashMember2019-01-012019-12-310001421461ipi:TrioMemberipi:PotashMember2019-01-012019-12-310001421461ipi:OilFieldServicesMemberipi:PotashMember2019-01-012019-12-310001421461ipi:PotashMemberus-gaap:IntersegmentEliminationMember2019-01-012019-12-310001421461ipi:PotashMember2019-01-012019-12-310001421461ipi:PotashMemberipi:TrioMember2019-01-012019-12-310001421461ipi:TrioMemberipi:TrioMember2019-01-012019-12-310001421461ipi:OilFieldServicesMemberipi:TrioMember2019-01-012019-12-310001421461ipi:TrioMemberus-gaap:IntersegmentEliminationMember2019-01-012019-12-310001421461ipi:TrioMember2019-01-012019-12-310001421461ipi:PotashMemberipi:WaterProductMember2019-01-012019-12-310001421461ipi:TrioMemberipi:WaterProductMember2019-01-012019-12-310001421461ipi:OilFieldServicesMemberipi:WaterProductMember2019-01-012019-12-310001421461ipi:WaterProductMemberus-gaap:IntersegmentEliminationMember2019-01-012019-12-310001421461ipi:WaterProductMember2019-01-012019-12-310001421461ipi:SaltMemberipi:PotashMember2019-01-012019-12-310001421461ipi:TrioMemberipi:SaltMember2019-01-012019-12-310001421461ipi:OilFieldServicesMemberipi:SaltMember2019-01-012019-12-310001421461ipi:SaltMemberus-gaap:IntersegmentEliminationMember2019-01-012019-12-310001421461ipi:SaltMember2019-01-012019-12-310001421461ipi:MagnesiumChlorideMemberipi:PotashMember2019-01-012019-12-310001421461ipi:TrioMemberipi:MagnesiumChlorideMember2019-01-012019-12-310001421461ipi:OilFieldServicesMemberipi:MagnesiumChlorideMember2019-01-012019-12-310001421461ipi:MagnesiumChlorideMemberus-gaap:IntersegmentEliminationMember2019-01-012019-12-310001421461ipi:MagnesiumChlorideMember2019-01-012019-12-310001421461ipi:PotashMemberipi:BrinesMember2019-01-012019-12-310001421461ipi:TrioMemberipi:BrinesMember2019-01-012019-12-310001421461ipi:OilFieldServicesMemberipi:BrinesMember2019-01-012019-12-310001421461ipi:BrinesMemberus-gaap:IntersegmentEliminationMember2019-01-012019-12-310001421461ipi:BrinesMember2019-01-012019-12-310001421461ipi:PotashMemberus-gaap:ProductAndServiceOtherMember2019-01-012019-12-310001421461ipi:TrioMemberus-gaap:ProductAndServiceOtherMember2019-01-012019-12-310001421461ipi:OilFieldServicesMemberus-gaap:ProductAndServiceOtherMember2019-01-012019-12-310001421461us-gaap:IntersegmentEliminationMemberus-gaap:ProductAndServiceOtherMember2019-01-012019-12-310001421461us-gaap:ProductAndServiceOtherMember2019-01-012019-12-310001421461ipi:PotashMemberus-gaap:MineralMember2019-01-012019-12-310001421461ipi:TrioMemberus-gaap:MineralMember2019-01-012019-12-310001421461ipi:OilFieldServicesMemberus-gaap:MineralMember2019-01-012019-12-310001421461us-gaap:IntersegmentEliminationMember2019-01-012019-12-310001421461us-gaap:RestrictedStockMember2021-12-310001421461us-gaap:EmployeeStockOptionMember2021-12-310001421461ipi:KeyEmployeesMemberipi:ServiceBasedVestingMemberus-gaap:RestrictedStockMember2021-01-012021-12-310001421461srt:DirectorMemberipi:ServiceBasedVestingMemberus-gaap:RestrictedStockMember2021-01-012021-12-310001421461ipi:ServiceBasedVestingMemberus-gaap:RestrictedStockMember2021-01-012021-12-310001421461ipi:ServiceBasedVestingMemberus-gaap:RestrictedStockMember2020-01-012020-12-310001421461ipi:ServiceBasedVestingMemberus-gaap:RestrictedStockMember2019-01-012019-12-310001421461ipi:ServiceAndMarketConditionBasedVestingMemberus-gaap:RestrictedStockMember2021-01-012021-12-310001421461ipi:ServiceAndMarketConditionBasedVestingMembersrt:ExecutiveOfficerMemberus-gaap:RestrictedStockMember2021-01-012021-12-310001421461ipi:ServiceAndMarketConditionBasedVestingMemberus-gaap:RestrictedStockMember2020-01-012020-12-310001421461ipi:ServiceAndMarketConditionBasedVestingMemberus-gaap:RestrictedStockMember2019-01-012019-12-310001421461ipi:ServiceAndMarketConditionBasedVestingMemberus-gaap:RestrictedStockMember2021-12-310001421461ipi:ServiceAndMarketConditionBasedVestingMemberus-gaap:RestrictedStockMember2020-12-310001421461ipi:ServiceAndMarketConditionBasedVestingMemberus-gaap:RestrictedStockMember2019-12-310001421461us-gaap:RestrictedStockMember2020-12-310001421461us-gaap:EmployeeStockOptionMember2020-12-310001421461us-gaap:EmployeeStockOptionMember2021-01-012021-12-3100014214612020-05-012020-05-310001421461ipi:ProtestantsExpeditedInterSeProceedingMember2019-02-012019-02-28utr:aft0001421461ipi:ProtestantsExpeditedInterSeProceedingMember2021-08-012021-08-310001421461ipi:ProtestantsExpeditedInterSeProceedingMember2017-01-012017-12-310001421461ipi:ProtestantsExpeditedInterSeProceedingMember2018-01-012018-12-310001421461ipi:WaterRightsMember2021-03-012021-03-310001421461ipi:WaterRightsMember2021-12-310001421461us-gaap:FairValueInputsLevel3Member2021-12-310001421461ipi:PotashMemberus-gaap:MineralMemberus-gaap:OperatingSegmentsMember2021-01-012021-12-310001421461ipi:TrioMemberus-gaap:MineralMemberus-gaap:OperatingSegmentsMember2021-01-012021-12-310001421461ipi:OilFieldServicesMemberus-gaap:MineralMemberus-gaap:OperatingSegmentsMember2021-01-012021-12-310001421461us-gaap:MineralMemberus-gaap:CorporateNonSegmentMember2021-01-012021-12-310001421461ipi:PotashMemberus-gaap:CargoAndFreightMemberus-gaap:OperatingSegmentsMember2021-01-012021-12-310001421461ipi:TrioMemberus-gaap:CargoAndFreightMemberus-gaap:OperatingSegmentsMember2021-01-012021-12-310001421461ipi:OilFieldServicesMemberus-gaap:CargoAndFreightMemberus-gaap:OperatingSegmentsMember2021-01-012021-12-310001421461us-gaap:CargoAndFreightMemberus-gaap:CorporateNonSegmentMember2021-01-012021-12-310001421461ipi:PotashMemberipi:WarehouseandHandlingMemberus-gaap:OperatingSegmentsMember2021-01-012021-12-310001421461ipi:TrioMemberipi:WarehouseandHandlingMemberus-gaap:OperatingSegmentsMember2021-01-012021-12-310001421461ipi:OilFieldServicesMemberipi:WarehouseandHandlingMemberus-gaap:OperatingSegmentsMember2021-01-012021-12-310001421461us-gaap:CorporateNonSegmentMemberipi:WarehouseandHandlingMember2021-01-012021-12-310001421461ipi:PotashMemberus-gaap:OperatingSegmentsMember2021-01-012021-12-310001421461ipi:TrioMemberus-gaap:OperatingSegmentsMember2021-01-012021-12-310001421461ipi:OilFieldServicesMemberus-gaap:OperatingSegmentsMember2021-01-012021-12-310001421461us-gaap:CorporateNonSegmentMember2021-01-012021-12-310001421461ipi:PotashMemberus-gaap:MineralMemberus-gaap:OperatingSegmentsMember2020-01-012020-12-310001421461ipi:TrioMemberus-gaap:MineralMemberus-gaap:OperatingSegmentsMember2020-01-012020-12-310001421461ipi:OilFieldServicesMemberus-gaap:MineralMemberus-gaap:OperatingSegmentsMember2020-01-012020-12-310001421461us-gaap:MineralMemberus-gaap:CorporateNonSegmentMember2020-01-012020-12-310001421461ipi:PotashMemberus-gaap:CargoAndFreightMemberus-gaap:OperatingSegmentsMember2020-01-012020-12-310001421461ipi:TrioMemberus-gaap:CargoAndFreightMemberus-gaap:OperatingSegmentsMember2020-01-012020-12-310001421461ipi:OilFieldServicesMemberus-gaap:CargoAndFreightMemberus-gaap:OperatingSegmentsMember2020-01-012020-12-310001421461us-gaap:CargoAndFreightMemberus-gaap:CorporateNonSegmentMember2020-01-012020-12-310001421461ipi:PotashMemberipi:WarehouseandHandlingMemberus-gaap:OperatingSegmentsMember2020-01-012020-12-310001421461ipi:TrioMemberipi:WarehouseandHandlingMemberus-gaap:OperatingSegmentsMember2020-01-012020-12-310001421461ipi:OilFieldServicesMemberipi:WarehouseandHandlingMemberus-gaap:OperatingSegmentsMember2020-01-012020-12-310001421461us-gaap:CorporateNonSegmentMemberipi:WarehouseandHandlingMember2020-01-012020-12-310001421461ipi:PotashMemberus-gaap:OperatingSegmentsMember2020-01-012020-12-310001421461ipi:TrioMemberus-gaap:OperatingSegmentsMember2020-01-012020-12-310001421461ipi:OilFieldServicesMemberus-gaap:OperatingSegmentsMember2020-01-012020-12-310001421461us-gaap:CorporateNonSegmentMember2020-01-012020-12-310001421461ipi:PotashMemberus-gaap:MineralMemberus-gaap:OperatingSegmentsMember2019-01-012019-12-310001421461ipi:TrioMemberus-gaap:MineralMemberus-gaap:OperatingSegmentsMember2019-01-012019-12-310001421461ipi:OilFieldServicesMemberus-gaap:MineralMemberus-gaap:OperatingSegmentsMember2019-01-012019-12-310001421461us-gaap:MineralMemberus-gaap:CorporateNonSegmentMember2019-01-012019-12-310001421461ipi:PotashMemberus-gaap:CargoAndFreightMemberus-gaap:OperatingSegmentsMember2019-01-012019-12-310001421461ipi:TrioMemberus-gaap:CargoAndFreightMemberus-gaap:OperatingSegmentsMember2019-01-012019-12-310001421461ipi:OilFieldServicesMemberus-gaap:CargoAndFreightMemberus-gaap:OperatingSegmentsMember2019-01-012019-12-310001421461us-gaap:CargoAndFreightMemberus-gaap:CorporateNonSegmentMember2019-01-012019-12-310001421461ipi:PotashMemberipi:WarehouseandHandlingMemberus-gaap:OperatingSegmentsMember2019-01-012019-12-310001421461ipi:TrioMemberipi:WarehouseandHandlingMemberus-gaap:OperatingSegmentsMember2019-01-012019-12-310001421461ipi:OilFieldServicesMemberipi:WarehouseandHandlingMemberus-gaap:OperatingSegmentsMember2019-01-012019-12-310001421461us-gaap:CorporateNonSegmentMemberipi:WarehouseandHandlingMember2019-01-012019-12-310001421461ipi:PotashMemberus-gaap:OperatingSegmentsMember2019-01-012019-12-310001421461ipi:TrioMemberus-gaap:OperatingSegmentsMember2019-01-012019-12-310001421461ipi:OilFieldServicesMemberus-gaap:OperatingSegmentsMember2019-01-012019-12-310001421461us-gaap:CorporateNonSegmentMember2019-01-012019-12-31ipi:markets0001421461us-gaap:GeographicConcentrationRiskMemberus-gaap:SalesRevenueNetMembercountry:US2021-01-012021-12-310001421461us-gaap:GeographicConcentrationRiskMemberus-gaap:SalesRevenueNetMembercountry:US2020-01-012020-12-310001421461us-gaap:GeographicConcentrationRiskMemberus-gaap:SalesRevenueNetMembercountry:US2019-01-012019-12-310001421461us-gaap:SubsequentEventMember2022-03-040001421461us-gaap:ValuationAllowanceOfDeferredTaxAssetsMember2018-12-310001421461us-gaap:ValuationAllowanceOfDeferredTaxAssetsMember2019-01-012019-12-310001421461us-gaap:ValuationAllowanceOfDeferredTaxAssetsMember2019-12-310001421461us-gaap:InventoryValuationReserveMember2018-12-310001421461us-gaap:InventoryValuationReserveMember2019-01-012019-12-310001421461us-gaap:InventoryValuationReserveMember2019-12-310001421461us-gaap:AllowanceForCreditLossMember2018-12-310001421461us-gaap:AllowanceForCreditLossMember2019-01-012019-12-310001421461us-gaap:AllowanceForCreditLossMember2019-12-310001421461us-gaap:ValuationAllowanceOfDeferredTaxAssetsMember2020-01-012020-12-310001421461us-gaap:ValuationAllowanceOfDeferredTaxAssetsMember2020-12-310001421461us-gaap:InventoryValuationReserveMember2020-01-012020-12-310001421461us-gaap:InventoryValuationReserveMember2020-12-310001421461us-gaap:AllowanceForCreditLossMember2020-01-012020-12-310001421461us-gaap:AllowanceForCreditLossMember2020-12-310001421461us-gaap:ValuationAllowanceOfDeferredTaxAssetsMember2021-01-012021-12-310001421461us-gaap:ValuationAllowanceOfDeferredTaxAssetsMember2021-12-310001421461us-gaap:InventoryValuationReserveMember2021-01-012021-12-310001421461us-gaap:InventoryValuationReserveMember2021-12-310001421461us-gaap:AllowanceForCreditLossMember2021-01-012021-12-310001421461us-gaap:AllowanceForCreditLossMember2021-12-31
UNITED STATES
SECURITIES AND EXCHANGE COMMISSION
Washington, D.C. 20549
FORM 10-K
| | | | | | | | | | | |
☒ | Annual Report Pursuant to Section 13 or 15(d) of the Securities Exchange Act of 1934 |
For the fiscal year ended December 31, 2021
| | | | | |
or |
☐ | Transition Report Pursuant to Section 13 or 15(d) of the Securities Exchange Act of 1934 |
For the transition period from to
Commission File Number: 001-34025
INTREPID POTASH, INC.
(Exact Name of Registrant as Specified in its Charter)
| | | | | |
Delaware | 26-1501877 |
(State or other jurisdiction of incorporation or organization) | (I.R.S. Employer Identification No.) |
1001 17th Street, Suite 1050 | |
Denver, | |
Colorado | 80202 |
(Address of principal executive offices) | (Zip Code) |
(303) 296-3006
(Registrant's telephone number, including area code)
Securities registered pursuant to Section 12(b) of the Act: | | | | | | | | |
Title of each class | Trading Symbol | Name of each exchange on which registered |
Common Stock, par value $0.001 per share | IPI | New York Stock Exchange |
Securities registered pursuant to Section 12(g) of the Act: None
Indicate by check mark if the registrant is a well-known seasoned issuer, as defined in Rule 405 of the Securities Act. Yes ¨ No x
Indicate by check mark if the registrant is not required to file reports pursuant to Section 13 or 15(d) of the Act. Yes ¨ No x
Indicate by check mark whether the registrant (1) has filed all reports required to be filed by Section 13 or 15(d) of the Securities Exchange Act of 1934 during the preceding 12 months (or for such shorter period that the registrant was required to file such reports), and (2) has been subject to such filing requirements for the past 90 days. Yes x No ¨
Indicate by check mark whether the registrant has submitted electronically every Interactive Data File required to be submitted pursuant to Rule 405 of Regulation S-T (§ 232.405 of this chapter) during the preceding 12 months (or for such shorter period that the registrant was required to submit and post such files.) Yes x No ¨
Indicate by check mark whether the registrant is a large accelerated filer, an accelerated filer, a non-accelerated filer, smaller reporting company, or an emerging growth company. See the definitions of "large accelerated filer," "accelerated filer," "smaller reporting company," and "emerging growth company" in Rule 12b-2 of the Exchange Act. | | | | | | | | | | | | | | | | | | | | | | | |
Large accelerated filer | ¨ | Accelerated filer | x | Non-accelerated filer | ¨ | | |
Smaller reporting company | ¨ | Emerging growth company | ¨ | | | | |
If an emerging growth company, indicate by check mark if the registrant has elected not to use the extended transition period for complying with any new or revised financial accounting standards provided pursuant to Section 13(a) of the Exchange Act. ¨
Indicate by check mark whether the registrant has filed a report on and attestation to its management's assessment of the effectiveness of its internal control over financial reporting under Section 404(b) of the Sarbanes-Oxley Act (15 U.S.C. 7262(b)) by the registered public accounting firm that prepared or issued its audit report. x
Indicate by check mark whether the registrant is a shell company (as defined by Rule 12b-2 of the Act). Yes ☐ No x
The aggregate market value of the registrant's common stock held by non-affiliates of the registrant, based upon the closing sale price of the common stock on June 30, 2021, the last trading day of the registrant's most recently completed second fiscal quarter, of $31.86 per share as reported on the New York Stock Exchange was $266 million. Shares of common stock held by each director and executive officer and by each person who owns 10% or more of the registrant's outstanding common stock and is believed by the registrant to be in a control position were excluded. The determination of affiliate status for this purpose is not a conclusive determination of affiliate status for any other purposes.
As of February 28, 2022, the registrant had 13,528,556 shares of common stock, par value $0.001, outstanding.
DOCUMENTS INCORPORATED BY REFERENCE
Certain information required by Items 10, 11, 12, 13 and 14 of Part III is incorporated by reference from portions of the registrant's definitive proxy statement relating to its 2022 annual meeting of stockholders to be filed within 120 days after December 31, 2021.
INTREPID POTASH, INC.
TABLE OF CONTENTS
PART I
Unless the context otherwise requires, the following definitions apply throughout this Annual Report on Form 10-K:
•"Intrepid," "our," "we," or "us" means Intrepid Potash, Inc. and its consolidated subsidiaries.
•"East," "North," and "HB" mean our three operating facilities in Carlsbad, New Mexico. "Moab" means our operating facility in Moab, Utah. "Wendover" means our operating facility in Wendover, Utah. "West" means our previous operating facility in Carlsbad, New Mexico, which was placed in care-and-maintenance mode in mid‑2016. "Intrepid South" refers to certain land, water rights, and other related assets in southeast New Mexico we acquired from Dinwiddie Cattle Company in May 2019. You can find more information about our facilities in Item 2 of this Annual Report on Form 10-K.
•"Ton" means a short ton, or a measurement of mass equal to 2,000 pounds.
To supplement our consolidated financial statements, which are presented in this Annual Report on Form 10-K and which are prepared and presented in accordance with generally accepted accounting principles ("GAAP"), we use "average net realized sales price per ton," which is a non‑GAAP financial measure to monitor and evaluate our performance. You can find more information about average net realized sales price per ton, including a reconciliation of this measure to the most comparable GAAP measure, in Item 7. Management's Discussion and Analysis of Financial Condition and Results of Operations under the heading "Non-GAAP Financial Measure."
CAUTIONARY NOTE REGARDING FORWARD‑LOOKING STATEMENTS
This Annual Report on Form 10-K contains forward‑looking statements within the meaning of the Securities Exchange Act of 1934, as amended (the "Exchange Act"), and the Securities Act of 1933, as amended. These forward‑looking statements are made pursuant to the safe harbor provisions of the Private Securities Litigation Reform Act of 1995. All statements in this Annual Report on Form 10-K other than statements of historical fact are forward‑looking statements. Forward-looking statements include, but are not limited to, statements about our future results of operations and financial position, our business strategy and plans, and our objectives for future operations, among other things. In some cases, you can identify these statements by forward‑looking words, such as "estimate," "expect," "anticipate," "project," "plan," "intend," "believe," "forecast," "foresee," "likely," "may," "should," "goal," "target," "might," "will," "could," "predict," and "continue." Forward‑looking statements are only predictions based on our current knowledge, expectations, and projections about future events.
These forward-looking statements are subject to a number of risks, uncertainties, and assumptions, which are described in Item 1A. Risk Factors in this Annual Report on Form 10-K.
In addition, new risks emerge from time to time. It is not possible for our management to predict all risks that may cause actual results to differ materially from those contained in any forward-looking statements we may make.
In light of these risks, uncertainties, and assumptions, the future events and trends discussed in this Annual Report on Form 10-K may not occur and actual results could differ materially and adversely from those anticipated or implied in these forward-looking statements. As a result, you should not place undue reliance on these forward-looking statements. We undertake no obligation to publicly update any forward-looking statements, except as required by law.
Reverse Stock Split
On July 24, 2020, we received notice from the New York Stock Exchange ("NYSE") that we were not in compliance with Section 802.01C of the NYSE Listed Company Manual that requires listed companies to maintain an average closing share price of at least $1.00 over a period of 30 consecutive trading days. Due to our reduced stock price, before we received notice of non-compliance we provided notice of a special meeting of stockholders to vote on four proposals that would allow our Board of Directors to effect a reverse stock split at a ratio between 1:3 and 1:15. On July 28, 2020, we held the special meeting and all the reverse stock split proposals were approved.
On August 10, 2020, the Board of Directors approved an amendment to our Certificate of Incorporation to effect a reverse stock split of our common stock, par value $0.001 per share, by a ratio of one-for-ten. The reverse stock split became effective August 14, 2020. Additionally, the total number of authorized shares of our common stock was reduced to 40,000,000 shares. Unless otherwise indicated, all share amounts, per share data, share prices, exercise prices and conversion rates set forth in this Annual Report on Form 10-K have, where applicable, been adjusted retroactively to reflect this reverse stock split.
ITEM 1.BUSINESS
General
We are a diversified mineral company that delivers potassium, magnesium, sulfur, salt, and water products essential for customer success in agriculture, animal feed and the oil and gas industry. We are the only U.S. producer of muriate of potash (sometimes referred to as potassium chloride or potash), which is applied as an essential nutrient for healthy crop development, utilized in several industrial applications, and used as an ingredient in animal feed. In addition, we produce a specialty fertilizer, Trio®, which delivers three key nutrients, potassium, magnesium, and sulfate, in a single particle. We also provide water, magnesium chloride, brine and various oilfield products and services.
Our extraction and production operations are conducted entirely in the continental United States. We produce potash from three solution mining facilities: our HB solution mine in Carlsbad, New Mexico, our solution mine in Moab, Utah and our brine recovery mine in Wendover, Utah. We also operate our North compaction facility in Carlsbad, New Mexico, which compacts and granulates product from the HB mine. We produce Trio® from our conventional underground East mine in Carlsbad, New Mexico.
We have permitted, licensed, declared and partially adjudicated water rights in New Mexico under which we sell water primarily to support oil and gas development in the Permian Basin near our Carlsbad facilities. We continue to work to expand our sales of water. In May 2019, we acquired certain land, water rights, state grazing leases for cattle, and other related assets from Dinwiddie Cattle Company. We refer to these assets and operations as "Intrepid South." Due to the strategic location of Intrepid South, part of our long-term operating strategy is selling small parcels of land, including restricted use agreements of surface or subsurface rights to customers, where such sales provide a solution to a customer's operations in the oil and gas industry.
Our principal offices are located at 1001 17th Street, Suite 1050, Denver, Colorado 80202, and our telephone number is (303) 296-3006. Intrepid was incorporated in Delaware in 2007.
Our Products and Services
Our three primary products are potash, Trio®, and water. We also sell salt, magnesium chloride, metal recovery salts, brines, and water that are derived as part of our mining processes. Product sales as a percentage of total sales for the last three years were as follows:
| | | | | | | | | | | | | | | | | | | | |
| | Year Ended December 31, |
| | 2021 | | 2020 | | 2019 |
Potash | | 48 | % | | 47 | % | | 47 | % |
Trio® | | 34 | % | | 33 | % | | 29 | % |
Water | | 8 | % | | 10 | % | | 12 | % |
Salt | | 4 | % | | 4 | % | | 6 | % |
Magnesium Chloride | | 3 | % | | 2 | % | | 2 | % |
Brines | | 1 | % | | 1 | % | | 1 | % |
Other | | 2 | % | | 3 | % | | 3 | % |
Total | | 100 | % | | 100 | % | | 100 | % |
Potash
We sell potash into three primary markets: the agricultural market as a fertilizer input, the industrial market as a component in drilling and fracturing fluids for oil and gas wells and an input to other industrial processes, and the animal feed market as a nutrient supplement. Potash is sold in different product sizes, such as granular, standard, and fine standard. The agricultural market predominately uses granular-sized potash, while the industrial and animal feed markets mostly use standard- and fine standard-sized product. We have the flexibility to produce all of our product in a granular form, which decreases our dependence on sales of any one particular size of potash and any particular market.
We manage sales and marketing operations centrally. This allows us to evaluate the product needs of our customers and then centrally determine which of our production facilities is best suited, typically based on geographic location, to use to fill customer orders in a manner designed to realize the highest average net realized sales price per ton. Average net realized sales price per ton is a non-GAAP measure that we calculate as sales less byproduct sales and freight costs and then divided by product sales tons. We also monitor product inventory levels and overall production costs centrally.
During 2021, we supplied approximately 0.4% of annual world potassium consumption and approximately 3.5% of annual U.S. potassium consumption.
Substantially all of our potash is sold in the United States, and many of our potash sales are geographically concentrated in the central and western United States. Fertilizer sales are affected by weather and planting conditions in these regions, as well as farmer economics. For more information, please see "Seasonality." A significant portion of our industrial sales are derived from oil and gas customers and vary based on the price of potash, the availability and price of substitute products, and changes in industry preferences.
Trio®
Trio® is our specialty fertilizer that delivers potassium, sulfate, and magnesium in a single particle and has the added benefit of being low in chloride. This unique combination of nutrients makes Trio® an attractive fertilizer across diverse crops and geographies. We produce Trio® in premium, granular, standard, and fine standard sizes for sale both domestically and internationally.
Oilfield Solutions
We have permitted, licensed, declared and partially adjudicated water rights in New Mexico under which we sell water primarily for industrial uses in the oil and gas services industry. We also offer potassium chloride ("KCl") real-time mixing services on location for hydraulic fracturing operations and trucking services. In May 2019, we acquired certain land, water rights, state grazing leases for cattle, and other related assets from Dinwiddie Cattle Company that support oil and gas development in the Permian Basin in southeast New Mexico. Our other oilfield related products and service offerings include, but are not limited to, caliche, right-of-way agreements, surface damages and easements, and a produced water royalty. We refer to these assets and operations as "Intrepid South." Due to the strategic location of Intrepid South, part of our long-term operating strategy is selling small parcels of land, including restricted use agreements of surface or subsurface rights, to customers, where such sales provide a solution to a customer's operations in the oil and gas industry. We sell water on Intrepid South under a joint marketing agreement with NGL Energy Partners, a land and water rights owner adjacent to our South property. Under this agreement, we are responsible for the marketing, sale, and delivery of water to various customers across our combined acreage. Demand for water and other oilfield related products and services is due to oil and gas activity and development in southeast New Mexico.
Byproducts
We also sell salt, magnesium chloride, metal recovery salts, brines, and water that are derived as part of our mining processes. Our salt is used in a variety of markets including animal feed, industrial applications, pool salt, and the treatment of roads and walkways for ice melting or to manage road conditions. Magnesium chloride is typically used as a road treatment agent for both deicing and dedusting. Our brines contain salt and potassium and are used primarily by the oil and gas industry to support well workover and completion activities. When the water that we sell was previously used in the production process for potash or Trio®, it is considered a byproduct of the underlying product. We continue to work to expand sales of byproducts, particularly to serve the oil and gas markets near our operating facilities. Sales of byproducts are accounted for within the segment that produced the byproduct. In each of the last three years, the majority of our byproduct sales were accounted for in the potash segment.
Production Facilities
We produce potash from three solar evaporation solution mining facilities: our HB solution mine in Carlsbad, New Mexico, a solution mine in Moab, Utah, and a brine recovery mine in Wendover, Utah. We also operate our North compaction facility in Carlsbad, New Mexico, which compacts and granulates product from the HB mine. Solution mining is a process by which potash is extracted from mineralized beds by injecting a salt-saturated brine into a potash ore body and recovering a brine that contains potash and other minerals. The brine is brought to the surface for mineral recovery through solar evaporation. For solar evaporation, the brine is placed in ponds and solar energy is used to evaporate water thus crystallizing out the potash and minerals contained in the brine. The resulting mineral evaporates are then processed to separate the minerals for sale. Solution mining does not require employees or machines to be underground.
We produce Trio® from our conventional underground East mine in Carlsbad, New Mexico. A conventional underground mine uses a mechanical method of extracting minerals from underground. Underground mining consists of multiple shafts or entry points and a network of tunnels to provide access to minerals and conveyance systems to transport materials to the surface. Underground mining machines are used to remove the ore and a series of pillars are left behind to provide the appropriate level of ground support to ensure safe access and mining.
We have a current estimated annual designed productive capacity of approximately 390,000 tons of potash from our solar evaporation solution mines. We also have an estimated annual designed productive capacity of 400,000 tons of Trio®.
Our annual production rates for potash and Trio® are less than our estimated productive capacity. Actual production is affected by operating rates, the grade of ore mined, recoveries, mining rates, evaporation rates, product pricing, product demand, and the amount of development work that we perform. Therefore, as with other producers in our industry, our production results tend to be lower than reported productive capacity.
We also have pipelines and ponds that we use to deliver water to customers. As mentioned above, we acquired Intrepid South in May 2019 which increased our water rights and water delivery infrastructure.
Industry Overview
Fertilizer serves a fundamental role in global agriculture by providing essential crop nutrients that help sustain both the yield and the quality of crops. The three primary nutrients required for plant growth are nitrogen, phosphate, and potassium. There are no known substitutes for these nutrients. A proper balance of each of the three nutrients is necessary to maximize their effectiveness. Potassium helps regulate plants' physiological functions and improves plant durability, providing crops with protection from drought, disease, parasites, and cold weather. Unlike nitrogen and phosphate, the potassium contained in naturally occurring potash does not require additional chemical conversion to be used as a plant nutrient.
In addition to the primary nutrients, which are required in the greatest quantities in crop nutrition, important secondary nutrients such as sulfur and magnesium are also essential in crop nutrition. Intrepid's Trio® product contains the primary nutrient potassium and two secondary nutrients, sulfur and magnesium.
Long-term global fertilizer demand has historically been driven primarily by population growth and global economic conditions with annual demand variations based on planted acreage, agricultural commodity yields and prices, inventories of grains and oilseeds, application rates of fertilizer, weather patterns, and farm sector income. We expect these key variables to continue to have an impact on global fertilizer demand for the foreseeable future. Sustained per capita income growth and agricultural policies in the developing world also affect global demand for fertilizer. Fertilizer demand is affected by other geopolitical factors such as temporary disruptions in fertilizer trade related to government intervention and changes in the buying patterns of key consuming countries. Volatility in agricultural commodity prices also may impact farmer fertilizer buying decisions.
The world potash market has long been characterized by nameplate production capacities that exceed demand. A significant portion of this capacity is controlled by a few companies and this concentration increased in early 2018 with the merger of two Canadian producers. Historically, these larger producers have managed production levels to approximate world demand. Several international brownfield and greenfield expansions have also begun production, with increases in production rates expected over the next few years. Due to the increased production, near-term potash pricing will likely depend on the larger producers' ability to continue to manage this supply and demand balance through decreased utilization rates. Increases in world fertilizer demand, due mainly to population growth and limitations on arable land, are expected to eventually lessen the burden on producers, although recent increases in productive capacities and the continued progress of key expansion projects, specifically BHP's approval of the Jansen Stage 1 potash project, add additional uncertainty to the long-term supply and demand balance for the potash market.
The United States potash market is also impacted by the volume of imports. A change in the volume of imports could result in a material change to potash prices in the United States. Sanctions were recently announced on Belarusian potash imports and are expected to take effect in April 2022. Belarusian potash has historically accounted for approximately 7% of annual demand in the United States. We expect other suppliers will increase their volume of imports in response to the sanctions although timing of these changes and the overall effect of the sanctions on the potash market are uncertain.
Virtually all of the world's potash is currently extracted from 19 commercial deposits. According to the International Fertilizer Industry Association and data published by potash mining companies, six countries accounted for approximately 88% of the world's aggregate potash production during 2020. During this time period, the top nine potash producers supplied approximately 96% of world production. Two major Canadian producers participate in the Canpotex marketing group that supplied approximately 29% of the global potash production in 2020, one producer in Russia supplied approximately 16% of global potash production in 2020 and one producer in Belarus supplied approximately 15% of the global potash production in 2020. Another Russian producer is currently undertaking a significant increase in potash production. If this producer achieves its goals, it could grow from approximately 2% of global potash production in 2020 to approximately 6% in the next few years.
Hydraulically fractured horizontal wells account for the majority of oil and gas wells drilled in the United States today and are responsible for the record amount of fossil fuels produced in the United States in recent years. The use of horizontal drilling in oil and gas production allows a well to remain in contact with the targeted formation, increasing production compared to a vertically drilled well. This process has resulted in longer wells, with some horizontal drilling sections reaching several miles long. The increase in horizontal drilling has also increased the use of fresh water, with a single frac potentially using millions of gallons. In the frac process, water and sand are used to move proppant and other frac additives into the targeted rock formation. Fresh water is important in the fracking process, as impurities in the water can impact the overall effectiveness of the frac. The majority of water used in fracking is transported by pipeline to the frac site, where it is stored in ponds or storage tanks. While fresh water remains a key input for many fracs, some operators have switched to using exclusively recycled water or a combination of fresh water and recycled water when completing wells. We believe this change is due to the growing focus on environmentally friendly operations and a response to the large amounts of produced water that is present in certain basins and formations, such as the Delaware Basin in southeast New Mexico. By recycling and reusing produced water, operators are able to reduce fresh water purchases and decrease the cost of transporting and disposing of produced water into disposal wells.
The most productive region in the United States for oil production is the Permian Basin, which spans from west Texas to southeastern New Mexico. As of January 2022, the Permian Basin produced approximately 5.0 million barrels of oil per day. For comparison, the next most productive region in the United States produced approximately 1.2 million barrels of oil per day. In addition to producing wells, the Permian Basin also had approximately 1,450 drilled but uncompleted wells as of December 2021.
Competition and Competitive Strategy
We sell into commodity markets and compete based on delivered price, our ability to deliver product in a timely manner, and product quality. We also compete based on the durability, particle size, and potassium oxide content of our potash and Trio® products. For potash, we compete primarily with much larger potash producers, principally Canadian producers and, to a lesser extent, producers located in Russia, Belarus, Chile, Germany, and Israel. For Trio®, we compete with one other producer of langbeinite as well as producers of other specialty nutrients and blended products. For water, we compete primarily with water-specialty companies, farmers, and ranchers operating in or near the Permian Basin in New Mexico. Some of our competitors and potential competitors may have significant advantages over us, including greater name recognition, longer operating histories, pre-existing relationships with current or potential customers, significantly greater financial, marketing and other resources, ownership of more diverse assets and products, geographically and/or access to less expensive mining assets, any of which could allow them to respond more quickly to new or changing opportunities.
Our competitive strategy is focused on the following:
•Maximize potash gross margin and optimize potash production. All of our potash production comes from solar solution mines, which carry fewer fixed costs than our conventional potash mines. Our per-ton costs are lower for solution mining than conventional mining as solar solution mining requires less labor, energy, and equipment. In addition, we have the advantage of being located close to the markets we serve, and the North American market is significantly larger than our production capacity. As a result, we are able to selectively participate in the markets that we believe will provide the highest average net realized sales price per ton. We also attempt to maximize our gross margin by leveraging our freight advantage to key geographies, our diverse customer and market base, and our flexible marketing approach. Long-term, we have optimization and expansion opportunities at our solution mining facilities, that, over time, could further reduce our per-ton costs and increase our potash production.
•Expand Trio® sales and maximize gross margin. We plan to continue to expand our sales and marketing efforts for Trio® in domestic markets and select international markets. Our efforts include continued crop nutrition education and increased marketing efforts targeting organic agriculture and high-value specialty crop markets. In order to maximize gross margin, we are working to optimize our production process to produce more granular-sized product, which is preferred by most markets. We currently operate our Trio® facility at a reduced production level and expect to continue to do so for the foreseeable future.
•Expand offerings of oilfield solutions. We intend to continue working to expand sales of water, particularly to service the oil and gas markets near our operating plants in New Mexico. We have a meaningful amount of water rights under which we sell water primarily for industrial uses such as in the oil and gas services industry. In addition, as described above, in May 2019, we acquired certain land, water rights, state grazing leases for cattle, and other related assets from Dinwiddie Cattle Company in the Permian Basin which we operate as Intrepid South. We expect to increase the amount of water available for sale on the Intrepid South property over the next few years through additional infrastructure investments and permitting. Our other oilfield related products and service offerings include, but are not limited to, caliche, right-of-way agreements, surface damages and easements, and a produced water royalty. With an increasing focus on environmentally friendly operations and due to the large amounts of produced water in the Delaware Basin, operators are using increasing amounts of recycled water when completing wells. We acquired multiple recycle units in the second half of 2021 and have begun hiring employees with the plan to enter the recycled water market in 2022. In 2020, we sold approximately 320 acres of our fee land on Intrepid South to an oil and gas operator, which only allows the buyer to drill Acid Gas Injection ("AGI") wells on the property to dispose of natural gas with high concentrations of hydrogen sulfide ("H2S"). Due to the strategic location of Intrepid South, part of our long-term operating strategy is selling small parcels of land, including restricted use agreements of surface or subsurface rights, to customers, where such sales provide a solution to a customer's operations in the oil and gas industry.
•Continue diversification of products and services. We recover magnesium chloride, salt, brines, and water during the production of potash and Trio®. These byproducts offer additional diversity to our portfolio of product and service offerings. As we continue to look for opportunities to diversify our revenue sources, we may enter into new or complementary businesses that expand our product and service offerings. We may also expand into oil and natural gas exploration and production, or into new products or services in our current industry or other industries.
Competitive Strengths
•U.S.-based producer. We are the only producer of potash in the United States. We are located in a market that consumes significantly more potash than we can currently produce on an annual basis. Our geographic location provides us with a transportation advantage over our competitors for shipping our product to our customers. In general, this allows us to obtain a higher average net realized sales price per ton than our competitors, who must ship their products across longer distances to consuming markets, which increases their costs and reduces their gross margin. Our location allows us to target sales to the markets in which we have the greatest transportation advantage, maximizing our average net realized sales price per ton. Our access to strategic rail destination points and our location along major agricultural trucking routes also support this advantage.
As a U.S. producer, we enjoy a significantly lower total production tax and royalty burden than our principal competitors, which operate primarily in Saskatchewan, Canada. The Saskatchewan tax system for potash producers includes a capital tax and several potash mineral taxes, none of which are imposed on us as a U.S. producer. We currently pay an average royalty rate of approximately 4.7% of our potash and Trio® sales less their related freight costs, which compares favorably to that of our competitors in Canada. The relative tax and royalty advantage for U.S. producers becomes more pronounced when profits per ton increase due primarily to the profit tax component of the Saskatchewan potash mineral tax.
•Solar evaporation operations. All of our potash production comes from solar solution mines. Solar evaporation is a cost-efficient production method because it significantly reduces labor and energy consumption, which are two of the largest costs of production. Our understanding and application of low-cost solution mining, combined with our reserves being located where a favorable climate for evaporation exists, make solar solution mining difficult for other producers to replicate. We also have significant reserves for future expansion of our solution mining operations.
•Participation in specialty markets. Given the greater scarcity of langbeinite relative to potash and its agronomic suitability for certain soils and crops, we believe there is a market for Trio® outside of our core potash markets. We also believe that there is a market for Trio® beyond the United States, although freight expense and competition from substitute products have made this a difficult market to penetrate. We also offer Organic
Materials Review Institute ("OMRI") listed organic potash and Trio® products that provide essential minerals for growing certified organic crops. Through our existing operations and assets, we also have the potential to grow our offerings of salt, water, and brine with low capital investments.
•Water rights. Water rights in New Mexico are real property rights, which authorize a water right owner to use a specific amount of water, diverted from a specific location, for a specific purpose of use, in a specific place. Water rights are limited to the amount of water put to beneficial use. In New Mexico, the New Mexico Office of the State Engineer (“OSE”) administers water rights. The validity of water rights are ultimately confirmed or denied by a court in an adjudication proceeding. Prior to an adjudication, a water right may be acquired through the OSE’s permitting or licensing process. If a water right existed before the OSE had authority to issue permits, a water rights owner may file a declaration with the OSE. The OSE issues permits for both surface and groundwater appropriations. These permits are inchoate rights, which allow a permittee to put the water to beneficial use as prescribed by the agency. Once the OSE confirms that water diversion works have been completed and water has been put to beneficial use, the water right is licensed. A declaration is made when water was put to beneficial use either before New Mexico adopted its current water code in 1907 for surface water declarations, or before the OSE declared an underground water basin for groundwater declarations. A water right claimant must apply to the OSE for a permit to make changes to a water right, including changes in the place or purpose of use. The validity of water rights are ultimately confirmed or denied by courts in an adjudication process. We have permitted, licensed, declared and partially adjudicated water rights in New Mexico under which we sell water primarily for industrial uses such as in the oil and gas services industry. We continue to work to expand sales of water, especially to support oil and gas development in the Permian Basin near our Carlsbad facilities. The Intrepid South property increased our total water rights available for sale and our footprint in and around the Delaware Basin, a sub-basin of the Permian Basin. We continue working to permit additional water rights on the Intrepid South property. This has expanded our relationships with oil and gas producers, which we may be able to use to expand sales of our industrial potash products, byproducts, and services.
•Diversity of potash markets. We sell potash into three different markets—the agricultural, industrial, and feed markets. During 2021, these markets represented approximately 78%, 6%, and 16% of our 2021 potash sales, respectively, and during 2020, these markets represented approximately 79%, 3%, and 18%, of our 2020 potash sales, respectively. The agricultural market supplies farmers producing a wide range of crops in different geographies. Because of our geographic proximity to areas that have seen recent increases in oil and gas drilling activity, we believe that we have an opportunity to promote the benefits of potash in drilling activities and to increase our industrial sales volumes.
•Marketing flexibility. We have the ability to convert all of our standard-sized potash product into granular-sized product as market conditions warrant. We also produce Trio® in premium, granular, standard and fine standard sizes. This provides us with increased marketing flexibility as well as decreased dependence on any one particular market.
•Significant reserve life. Our potash and langbeinite reserves each have substantial years of reserve life, with remaining reserve lives for our actively mined areas ranging from approximately 24 years to more than 100 years, based on proven and probable reserve estimates. In addition to our reserves, we have water rights and access to additional mineralized areas of potash for potential future exploitation.
•Existing facilities and infrastructure. Constructing a new potash production facility requires substantial time and extensive capital investment in mining, milling, and infrastructure to extract, process, store, and ship product. Our operations already have significant facilities and infrastructure in place. We also have the ability to expand our business using existing installed infrastructure, in less time and with lower expenditures than would be required to construct entirely new mines.
Seasonality
The sales pattern for potash sold into the agricultural market is seasonal. Over the last three years, our monthly potash sales volume has been highest in February through May and September through November when purchasers are looking to have product on hand in advance of the spring and fall application seasons in the United States. In turn, our monthly potash sales volume has been the lowest in June, July and December. The specific timing of when farmers apply potash remains highly weather dependent and varies across the numerous growing regions within the U.S. The timing of potash sales is significantly influenced by the marketing programs of potash producers, as well as storage volumes closer to the farm gate.
The sales pattern for Trio® sold into the domestic agricultural market is also seasonal. Over the last three years, our domestic Trio® sales volume has been highest in March and April, as Trio® products are typically applied to crops in the United
States during the spring planting season. Demand for the spring planting season generally runs from December to May, during which we have sold approximately 60% of our domestic Trio® volumes over the past three years. As we expand our Trio® sales efforts outside of the United States, we expect the overall seasonality of our Trio® sales to be impacted by the timing of deliveries to warehouses as we generally ship in larger volumes to minimize per ton transportation costs.
The month-to-month seasonality of our agricultural sales is somewhat moderated due to the variety of crops, industries, distribution strategies, and geographies that we serve. Because all of our potash production comes from our solar solution mines, our potash production is also seasonal. Our solar solution mines suspend potash production activities from early spring through late summer, the peak solar evaporation period. Accordingly, we manage our inventories during the low demand periods of the year in order to ensure timely product availability during the peak sales seasons, as well as during the summer evaporation period when we have no potash being produced. The seasonality of fertilizer demand results in our sales volumes being the highest during the spring and our working capital requirements being the highest just before the start of the spring season. We have observed fertilizer dealers in North America instituting practices that are designed to reduce their risk of changes in the price of fertilizer products through consignment-type programs. These programs tend to make the timing of the spring and fall seasonal demand profile less predictable within the season. Further, through technological advances, the farmers in the United States have gained efficiencies in planting and harvesting their crops, which has compressed the application seasons.
Our quarterly financial results can also vary from one year to the next due to weather‑related shifts in planting schedules and purchasing patterns.
Demand for our oilfield products and services is highly correlated to oil and gas exploration activities and can vary from quarter to quarter.
Major Customers
Within the agricultural market, we supply a diversified customer base of distributors, cooperatives, retailers, and dealers, which in turn supply farmers producing a wide range of crops in different geographies. We sell into the industrial and feed markets through sales to distributors and directly to end users. For water, we sell to a diverse set of customers through a combination of spot sales and multi-year contracts.
In each of 2021, 2020 and 2019, no customer accounted for more than 10% of our total sales.
Environmental, Safety, and Health Matters
We are subject to an evolving set of federal, state, and local environmental, safety, and health laws that regulate, among other things; (1) soil, air, and water quality standards for our facilities; (2) disposal, storage, and management of hazardous and solid wastes; (3) post-mining land reclamation and closure; (4) conditions of mining and production operations; (5) employee and contractor safety and occupational health; and (6) product content and labeling. We employ and consult with professionals who assist in monitoring our compliance with these laws and who work with management to ensure that appropriate strategies and processes are in place to promote a culture that prioritizes safety and environmental responsibility.
In 2021, we had approximately $0.3 million of capital investments, and $1.4 million in other expenses, relating to environmental compliance, environmental studies, and remediation efforts. We expect to spend $1.0 million to $3.0 million for environmental related capital and reclamation projects in both 2022 and 2023. Future capital expenditures are subject to a number of uncertainties, including changes to environmental regulations and interpretations, and enforcement initiatives. If potential negative effects to the environment are discovered, or if the potential negative effects are of a greater magnitude than currently estimated, material expenditures could be required in the future to remediate the identified effects. We expect that continued emphasis on environmental issues will result in increased future investments for environmental controls at our operations. See Item 1A. Risk Factors “Risks Related to Our Business - Environmental laws and regulations could subject us to significant liability and require us to incur additional costs.”
Product Registration Requirements
We are required to register fertilizer products with each U.S. state and foreign country where products are sold. Each brand and grade of commercial fertilizer must be registered with the appropriate state agency before being offered for sale, sold, or distributed in that jurisdiction. In most cases, these product registrations impose specific requirements relating to guaranteed analysis, product labeling, and regular reporting of sales.
Some states require similar registration and reporting for feed grade products. Industrial-grade products typically do not require registration or reporting.
Operating Requirements and Government Regulations
Permits
We are subject to numerous environmental laws and regulations, including laws and regulations regarding land use and reclamation; release of emissions to the atmosphere or water; plant and animal life; and the generation, treatment, storage, disposal, and handling of hazardous substances and wastes. These laws include the Clean Air Act; the Clean Water Act; the Resource Conservation and Recovery Act; the Comprehensive Environmental Response, Compensation, and Liability Act ("CERCLA"); the Toxic Substances Control Act; and various other federal, state, and local laws and regulations. Violations can result in substantial penalties, court orders to install pollution‑control equipment, civil and criminal sanctions, permit revocations, and facility shutdowns. In addition, environmental laws and regulations may impose joint and several liability, without regard to fault, for cleanup costs on potentially responsible parties who have released, disposed of, or arranged for release or disposal of hazardous substances in the environment.
We hold numerous environmental, mining, and other permits or approvals authorizing operations at each of our facilities. Our operations are subject to permits for, among other things, extraction of salt and brine, discharges of process materials and waste to air and surface water, injection of brine, and appropriation of water. Some of our proposed activities may require waste storage permits. A decision by a government agency to deny or delay issuing a new or renewed permit or approval, or to revoke or substantially modify an existing permit or approval, could limit or prevent us from mining at these properties. In addition, changes to environmental and mining regulations or permit requirements could limit our ability to continue operations at the affected facility. In many cases, environmental permits and approvals are also required for an expansion of, or changes to, our operations. As a condition to procuring the necessary permits and approvals, we may be required to comply with financial assurance regulatory requirements. The purpose of these requirements is to assure the government that sufficient company funds will be available for the ultimate reclamation, closure, and post-closure care at our facilities. We obtain bonds as financial assurance for these obligations. These bonds require annual payment and renewal.
We believe we are in compliance with existing regulatory programs, permits, and approvals where non-compliance could have a material adverse effect on our operating results or financial condition. In 2016, the OSE determined that our East tailing impoundment embankments are considered jurisdictional dams. We continue to work with the OSE to determine required dam modifications associated with this determination. We may be required to spend a significant amount of capital to bring the impoundments into compliance with requirements for jurisdictional dams or modify our operations to no longer use impoundments that may qualify as jurisdictional dams.
From time to time, we have received notices from governmental agencies that we are not in compliance with certain environmental laws, regulations, permits, or approvals. For example, although designated as zero discharge facilities under the applicable water quality laws and regulations, our East, North, and Moab facilities at times may experience some water and brine discharges during periods of significant rainfall or due to other circumstances. We have implemented several initiatives to address discharge issues, including the reconstruction or modification of certain impoundments, increasing evaporation, and reducing process water usage and discharges and improved management systems. State and federal officials are aware of these issues and have visited the sites to review our corrective efforts and action plans.
Air and Drinking Water
In the ordinary course of our business, from time to time, we receive notices from the New Mexico Environment Department of alleged air or drinking water quality control violations. Upon receipt of these notices, we evaluate the matter and take any required corrective actions. In some cases, we may be required to pay civil penalties for these notices of violation. The Utah Division of Air Quality conducts periodic compliance inspections at our Moab and Wendover facilities and affirms our compliance with applicable approval orders.
Safety and Health Regulation and Programs
Certain of our facilities are subject to the Federal Mine Safety and Health Act of 1977, the Occupational Safety and Health Act, related state statutes and regulations, or a combination of these laws.
The Mine Safety and Health Administration ("MSHA") is the governing agency for our conventional underground mines and related surface facilities in New Mexico. As required by MSHA, these operations are regularly inspected by MSHA personnel. Item 4 and Exhibit 95.1 to this Annual Report on Form 10-K provide information concerning certain mine safety violations.
Our New Mexico facilities participate in MSHA's Region 8 "Partnership Program." There is a formally signed document and plan, pursuant to which each party commits to specific actions and behaviors. Examples of principles include working for an open, cooperative environment; agreeing to citation and conflict processes; and improving training. Our New Mexico facilities are serviced by a trained mine rescue team, which is ready to respond to on-site incidents or assist in local
incidents, if needed. The team practices and participates at state and federal events and competitions. In addition, our New Mexico facilities participate in a basin agreement with other natural resource and hazardous waste facilities to provide mine rescue support.
The Occupational Safety and Health Administration ("OSHA") is the governing agency relating to the safety standards at our Utah facilities, as well as our HB mine and plant. Training and other certifications are provided to employees as needed based upon their work duties.
Remediation at Intrepid Facilities
Many of our current facilities have been in operation for a number of years. Operations by us and our predecessors have involved the historical use and handling of potash, salt, related potash and salt byproducts, process tailings, hydrocarbons and other regulated substances. Some of these operations resulted, or may have resulted, in soil, surface water, or groundwater contamination. At some locations, there are areas where process waste, building materials (including asbestos‑containing transite), and ordinary trash may have been disposed or buried, and have since been properly closed and maintained.
At many of these facilities, spills or other releases of regulated substances may have occurred previously and potentially could occur at any of our facilities in the future, possibly requiring us to undertake or fund cleanup efforts under CERCLA or state laws governing cleanup or disposal of hazardous and solid waste substances.
We work closely with governmental authorities to obtain the appropriate permits to address identified site conditions. For example, buildings located at our facilities in both Utah and New Mexico have a type of siding that contains asbestos. We have adopted programs to encapsulate and stabilize portions of the siding through use of an adhesive spray and to remove the siding, replacing it with an asbestos-free material. Also, we have trained asbestos abatement crews that handle and dispose of the asbestos‑containing siding and related materials. We have a permitted asbestos landfill in Utah and have worked closely with Utah officials to address asbestos‑related issues at our Moab mine.
Reclamation Obligations
Mining and processing of potash generates residual materials that must be managed both during the operation of the facility and upon facility reclamation and closure. Potash tailings, consisting primarily of salt and fine sediments that remain after potash is removed from ore during processing, are stored in surface disposal sites. Some of these tailing materials may also include other contaminants, such as lead, that were introduced as reagents during historic processing methods that may require additional management and could cause additional disposal and reclamation requirements to be imposed. For example, at least one of our New Mexico mining facilities may have legacy issues regarding lead in the tailings pile resulting from production methods utilized prior to our acquisition of these assets. During the life of the tailings management areas, we have incurred, and will continue to incur, significant costs to manage potash residual materials in accordance with environmental laws and regulations and with permit requirements. Additional legal and permit requirements will take effect when these facilities are closed.
Our surface permits require us to reclaim property disturbed by operations at our facilities. Our operations in Utah and New Mexico have specific obligations related to reclamation of the land after mining and processing operations are concluded. The discounted present value of our estimated reclamation costs for our facilities as of December 31, 2021, is approximately $27.0 million, which is reflected in our audited financial statements found elsewhere in this Annual Report on Form 10-K. Various permits and authorization documents negotiated with or issued by the appropriate governmental authorities include these estimated reclamation costs on an undiscounted basis.
It is difficult to estimate and predict the potential actual costs and liabilities associated with remediation and reclamation, and there is no guarantee that we will not be identified in the future as potentially responsible for additional remediation and reclamation costs, either as a result of changes in existing laws and regulations or as a result of the identification of additional matters subject to remediation and/or reclamation obligations or liabilities.
Royalties
The potash, langbeinite, water, and byproducts we produce and sell from leased land may be subject to royalty payments. We produce and sell from leased land owned by the U.S. government, the States of New Mexico and Utah, and private landowners. The terms of the royalty payments are determined at the time of the issuance or renewal of the leases. Some royalties are determined as a fixed percentage of revenue and others vary based upon ore grade. Additionally, some of our leases are subject to overriding royalty interest payments paid to various owners. In 2021, we paid $10.8 million in royalties and other taxes. The royalty rates on our state and federal leases in New Mexico are currently set at various rates from 2.0% to 5.0%. The royalty rates on our state and federal leases in Utah are currently set at rates from 3.0% to 5.0%. The royalty rates for the private leaseholds are between 5.0% and 8.0%. For certain water sales we pay an $0.11 per barrel sold royalty to the State of New Mexico.
Human Capital Resources
Headcount
We believe that our employees and contractors are significant contributors to our success and the future success of our Company, which depends on our ability to attract, retain, and motivate qualified personnel. The skills, experience and industry knowledge of key employees significantly benefit our operations and performance. As of December 31, 2021, we had 440 employees distributed across our four main locations. Our workforce is well-tenured providing invaluable experience and insight into our operations.
| | | | | | | | |
Location | Number of Employees | Average Tenure (in years) |
Denver | 39 | 6 |
Moab | 61 | 12 |
New Mexico | 284 | 10 |
Wendover | 56 | 16 |
We have a collective bargaining agreement with a labor organization representing our hourly employees in Wendover, Utah, which expires on May 31, 2023. This is the eighth agreement negotiated between us and the United Steel, Paper and Forestry, Rubber, Manufacturing, Energy, Allied Industrial and Service Workers International Union, Local 867. We consider our relationships with our employees to be good.
Employee Development and Training
We believe in providing opportunities for employees to continue to develop and grow their careers. We offer a tuition reimbursement program and ongoing support of continuing education for professional certifications and other credentials. We also provide a comprehensive Career Path program for our hourly employees that clearly outlines the proficiencies necessary for each job level as well as the development steps to progress through various job levels.
Competitive Pay and Benefits
We have structured our compensation programs to balance incentive earnings for both short-term and long-term performance. We provide employee wages that are competitive and consistent with employee positions, skill levels, experience, knowledge, and geographic location. We align our executives' long-term equity compensation with our shareholders' interests by linking realizable pay with stock performance.
We are also committed to providing comprehensive benefit options and it is our intention to offer benefits that will allow our employees and their families to live healthier and more secure lives. Some examples of our wide ranging benefits offered are: health insurance, telemedicine, an employee assistance program, paid and unpaid leaves, life insurance, short-term disability insurance and a retirement savings plan with a company match. We also offer a variety of voluntary benefits that allow employees to select the options that meet their needs, including flexible time-off, adoption assistance, prescription savings solutions, and a wellness program.
Diversity and Inclusion
We are committed to building a culture where diversity and inclusion are core philosophies across our operations, including, but not limited to, our decisions around recruitment, promotion, transfer, leaves of absence, compensation, opportunities for career support and advancement, job performance and other relevant job-related criteria. We embrace an approach to hiring and advancement that considers the value of diversity, and we are also committed to making opportunities for development and progress available to all employees so their talents can be fully developed to maximize our and their success. We believe that creating an environment that cultivates a sense of belonging requires encouraging employees to continue to educate themselves about each other’s experiences, and we strive to promote the respect and dignity of all persons. We also believe it is important that we foster education, communication and understanding about diversity, inclusion and belonging. Finally, in line with our commitments to equal employment opportunity and diversity and inclusion, we expect recruiters operating on our behalf to provide us with a diverse pool of candidates.
Health and Safety
The health and safety of our employees is our highest priority, and this is consistent with our operating philosophy. We are committed to providing a safe, functional, and effective work environment for anyone who comes on our properties. We have implemented several safety policies and protocols at each of our locations.
In response to the COVID-19 pandemic, we have implemented significant changes that we believe to be in the best interest of our employees, as well as the communities in which we operate, and that comply with government orders. These include having our office employees work from home to the extent they are able and implementing additional safety measures, including increased cleaning protocols and social distancing procedures at all facilities, and other recommended public health measures for our field and other employees (including on-site contract workers) continuing critical on-site work.
Environmental, Social, and Governance
We are committed to a goal of providing consistent returns to our shareholders while maintaining a strong sense of good corporate citizenship that places a high value on the welfare of our employees, the communities in which we operate, the customers we serve, and the world as a whole. We believe that prioritizing, improving, and managing our Environmental, Social, and Governance (“ESG”) goals will allow us to better create long-term value for our investors. We have made our ESG program a key initiative for our management team and we are committed to a plan to provide focused reporting on those ESG issues that we believe are the most relevant to our business and important to our stakeholders. We understand that clearly disclosing the goals and metrics related to our ESG programs will allow our stakeholders to be informed about our progress and we look forward to expanding our disclosures in future periods. A summary of our ESG goals under the United Nations Sustainable Development Goals framework is available on our website at intrepidpotash.com. An update on recent ESG highlights and initiatives is shown below.
Commitment to the Environment
We rely on the environments, resources and ecosystems surrounding our locations in all segments of our business. We work closely with our communities and make it a priority to protect the natural resources surrounding our operations.
–Full-Cycle Water Management - We are actively developing water treatment and recycling operations in the Delaware Basin. Recycled water will reduce the amount of produced water that is injected into produced water disposal wells.
–Solar solution mining potash - All of our potash is currently produced at solar solution mines, one of the most environmentally friendly and energy efficient mining techniques. We inject a naturally occurring, salt saturated brine solution into underground caverns or previously shuttered mine workings. This brine selectively dissolves the remaining potash, which is then pumped back to the surface and into evaporation ponds. During the spring and summer months, the brine naturally evaporates, leaving only the salt and potash solids in the ponds, which we then process into the products we sell. By using solar energy, we do not need to burn natural gas or coal to evaporate our brine ponds.
–Salt laydown at the Bonneville Salt Flats - We are committed to helping maintain the environments in which we operate, one of which is the Bonneville Salt Flats near our Wendover, UT mine. Since 2005, we have donated free of cost to the BLM nearly 7 million tons of salt that has been deposited on the racetrack to help preserve this unique attraction in northwest Utah. We drilled an additional brackish well in 2021 to increase the brine available for the salt laydown project.
–We are the only OMRI-listed potash and langbeinite producer in the United States. We became OMRI-listed in 2007 for our langbeinite, or Trio®, product, and in 2018 for our potash products at our Moab and Wendover operating facilities. We are also registered in the Organic Input Material Program through the California Department of Food and Agriculture, a program which registers fertilizers that can be used in organic crop and food production.
–We work closely with the Bureau of Land Management and other government and regulatory agencies to preserve historical sites near our operations such as the Maroon Cliffs in Carlsbad, New Mexico and petroglyphs near our Utah operations. We also work with and have supported agencies dedicated to studying and protecting endangered species near our operations such as the sand dune lizards in New Mexico.
Our Social Impact and Supporting our Communities
Our employees live and work in small, tight-knit communities and we are deeply involved in volunteering and being active community members.
Our New Mexico operations have partnered with the United Way of Carlsbad and South Eddy County since 2004, participating in a variety of community-focused events and activities such as United Way's annual Day of Caring event. We encourage all our employees to volunteer in their communities and we offer all our full-time employees three paid volunteer days each year to support either a charitable organization of their choosing or participate in an Intrepid sponsored volunteer project.
Our Commitment to a Diverse Workforce
We are committed to a recruitment and hiring process that emphasizes and embraces diversity. We believe a diverse workforce leads to greater collaboration, innovation, and improves shareholder returns and we celebrate the great value the differences in our people bring to our organization. We support a variety of organizations within our communities including the Women's Leadership Foundation, a Colorado based organization with the goal of opening more board of director positions to women leaders in Colorado and beyond.
Our Commitment to Safety
Safety audits are conducted across all our locations to ensure a thoughtful approach can be taken that increases the safe execution of all tasks. Through our audits and dialogue, we educate ourselves and understand the potential hazards present, create best practices that can be shared, and address areas where improvements can be made. Prior to each task, employees are required to: assemble the proper personal protection equipment, tools, permits, etc., ensure the area is safe for employees and contractors, discuss the task with all stakeholders, and understand how the task is related to the overall business.
We conduct safety audits of our operations on a monthly basis. The data from these safety audits is collected to analyze where, what, and why gaps exist, and to provide meaningful information that results in safer work for our employees.
In August 2021, our East Mine operation in Carlsbad, New Mexico received the National 2020 Sentinels of Safety Award in the large underground nonmetal category. The Sentinels of Safety Award is presented by the National Mining Association each year to recognize the outstanding safety achievements of mining operations across a variety of categories.
Business Ethics
Since inception, Intrepid has placed the highest emphasis on conducting its business with honesty and integrity. These standards are expected of management and employees alike, and we continuously strive to create a corporate culture of honesty, integrity, and trust.
The policies we have developed are intended to:
–Maintain and communicate our core value of integrity and disseminate our core values and the legal requirements applicable to good business conduct and ethical behavior.
–Annual refresher training on company policies, values, interpreting laws, and handling a variety of potential company-related issues and situations.
–Resources for employees to report any suspected violations of our company policies, including an anonymous employee hotline via phone and internet.
–Provide clear and well-defined procedures by which employees can easily obtain information, ask questions, and, if necessary, report any suspected violations of any of our Business Ethics policies.
–Maintain and communicate a Code of Business Conduct and Ethics which clearly articulates the company’s values, culture, and practices.
Available Information
We file or furnish with the U.S. Securities and Exchange Commission (the "SEC") reports, including our Annual Reports on Form 10-K, Quarterly Reports on Form 10-Q, Current Reports on Form 8-K, proxy statements, and any amendments to these reports filed or furnished pursuant to Section 13(a) or Section 15(d) of the Exchange Act. These reports are available free of charge on our website at www.intrepidpotash.com as soon as reasonably practicable after they are electronically filed with or furnished to the SEC. These reports also can be obtained at www.sec.gov.
We routinely post important information about us and our business, including information about upcoming investor presentations, on our website, www.intrepidpotash.com, under the Investor Relations tab. We encourage investors and other interested parties to enroll on our website to receive automatic email alerts or Really Simple Syndication (RSS) feeds regarding new postings. The information found on, or that can be accessed through, our website is not part of this or any other report we file with, or furnish to, the SEC.
Executive Officers
The following section includes biographical information for our executive officers:
| | | | | | | | | | | | | | |
Name | | Age | | Position |
Robert P. Jornayvaz III | | 63 | | Executive Chairman of the Board and Chief Executive Officer |
E. Brian Stone | | 59 | | President and Chief Operational Officer |
Robert E. Baldridge | | 60 | | Senior Vice President - New Mexico |
Matthew D. Preston | | 37 | | Chief Financial Officer |
Kyle R. Smith | | 48 | | Vice President, General Counsel and Secretary |
| | | | |
Robert P. Jornayvaz III has served as our Executive Chairman of the Board since 2010 and as our Chief Executive Officer since August 2014. Mr. Jornayvaz served as our Chairman of the Board and Chief Executive Officer from our formation in 2007 until 2010. Mr. Jornayvaz served, directly or indirectly, as a manager of our predecessor, Intrepid Mining LLC, from 2000 until its dissolution at the time of our initial public offering in 2008. Mr. Jornayvaz is the sole owner of Intrepid Production Corporation. Mr. Jornayvaz and Intrepid Production Corporation together beneficially own 15.2% of our common stock, as of January 31, 2021.
E. Brian Stone has served as President since August 2021 and our Chief Operating Officer since December 2019. Prior to joining Intrepid, Mr. Stone was the Chief Operating Officer for Hupecol Operating Co. LLC, an international oil and gas company focused on South America and Europe, from 2005 to 2019.
Robert E. Baldridge has served as our Senior Vice President - New Mexico since December 2019. Mr. Baldridge served as General Manager of our New Mexico operations from July 2010 to December 2019 and Manager of Mines since our formation in 2007. Previously Mr. Baldridge served as Mine Manager of Intrepid Mining from 2003 until its dissolution at the time of our IPO in 2008. Prior to joining Intrepid, Mr. Baldridge held various positions with Mississippi Potash, Inc. from 1988 to 2003. Mr. Baldridge has over 30 years of experience in the potash mining industry.
Matthew D. Preston has served as our Chief Financial Officer since December 2021. Mr. Preston also serves as our principal financial officer and principal accounting officer. Mr. Preston served as our Vice President of Finance from November 2019 to December 2021 and our Director of Budget and Forecast from April 2016 to November 2019. Previously, Mr. Preston served in successively more senior finance roles since joining Intrepid in 2008, including Senior Manager of Budget and Forecast, Manager of Budget and Forecast, and Financial Analyst.
Kyle R. Smith has served as our Vice President, General Counsel and Secretary since December 2019. Before joining Intrepid, Mr. Smith served as General Counsel for an Alaska Native Claims Settlement Act Regional Corporation. Prior to that, Mr. Smith was in private practice from July 2017 to January 2019, served as Executive Vice President and General Counsel for Echo Energy, a start-up pure-play oil and gas operator from December 2016 to June 2017, and as Assistant General Counsel for Operations for Continental Resources, a large independent upstream producer, from June 2014 to June 2016.
ITEM 1A.RISK FACTORS
You should carefully consider the following risk factors. Our future performance is subject to a variety of risks and uncertainties that could materially and adversely affect our business, financial condition, and results of operations, and the trading price of our common stock. We may be subject to other risks and uncertainties not presently known to us. See "Cautionary Note Regarding Forward-Looking Statements."
Summary Risk Factors
Below is a summary of some of the principal risks that could adversely affect our business, operations and financial results:
Risks Related to Our Business
•The COVID-19 pandemic has, and may continue to, disrupt our business, including, among other things, demand for our products, our personnel and production processes, each of which has and could continue to materially affect our operations, liquidity, financial condition and results of operations.
•Our potash sales are subject to price and demand volatility resulting from periodic imbalances of supply and demand, which could negatively affect our results of operations.
•We are working to expand our sales of Trio®, and our sales and results of operations could be negatively impacted if we are unsuccessful in our plans.
•We may not be successful in our efforts to sustain or expand water sales due to the status of our water rights, challenges to our water rights, changes in the demand for water in the areas around our facilities, or other events, which could adversely impact our financial condition and results of operations.
•A decline in oil and gas drilling or a reduction in the use of potash in drilling fluids could decrease our revenue.
•We may alter or expand our operations or continue to pursue acquisitions, which could adversely affect our business if we are unable to manage any expansion or acquisition effectively.
•Aggressive pricing or operating strategies by our competitors could adversely affect our sales and results of operations.
•The seasonal demand for our products, and the resulting variations in our cash flows from quarter to quarter, could have an adverse effect on our results of operations and working capital requirements.
•Our Trio® profitability could be affected by market entrants or the introduction of langbeinite alternatives.
•International sales could present risks to our business.
•If potash or Trio® prices decline, or oil and gas activity declines, we could be required to record write-downs of our long-lived and indefinite-lived assets, which could adversely affect our results of operations and financial condition.
•If we are required to write down the value of our inventories, our financial condition and results of operations would be adversely affected.
•Weakening of foreign currencies against the U.S. dollar could lead to lower domestic potash prices, which would adversely affect our results of operations. Currency fluctuations could cause our results of operations to fluctuate.
•Our business depends on skilled and experienced workers, and our inability to find and retain quality workers could have an adverse effect on our development and results of operations.
•Increases in the prices of energy and other important materials used in our business, or disruptions to their supply, could adversely impact our sales, results of operations, or financial condition.
•Increased costs could affect our per-ton profitability.
•A shortage of railcars or trucks for transporting our products, increased transit times, or interruptions in railcar or truck transportation could result in customer dissatisfaction, loss of sales, higher transportation or equipment costs, or disruptions in production.
•We rely on our management personnel for the development and execution of our business strategy, and the loss of one or more members of our management team could harm our business.
•We have less product diversification than nearly all of our competitors, which could have an adverse effect on our financial condition and results of operations.
•Heavy precipitation or low evaporation rates at our solar solution mines could impact our potash production at those facilities, which could adversely affect our sales and results of operations.
•Inflows of water into our langbeinite mine from heavy rainfall or groundwater could result in increased costs and production downtime and could require us to abandon the mine, any of which could adversely affect our results of operations.
•A significant disruption to our information technology systems could adversely affect our business and operating results.
•Our business may be adversely affected by union activities.
•We will be subject to a number of uncertainties while we pursue the initial public offering of Intrepid Acquisition Corporation I (“IACI”), and during the timeframe when IACI pursues an initial business combination, which could adversely affect our business, financial condition, results of operations, cash flows and stock price.
Risks Related to Our Industry
•Changes in the agricultural industry could exacerbate the cyclical nature of the prices and demand for our products or adversely affect the markets for our products.
•Mining is a complex process that frequently experiences production disruptions, which could adversely affect our results of operations.
•Mining is a hazardous process, and accidents could result in significant costs or production delays.
•The grade of ore that we mine could vary from our projections due to the complex geology and mineralogy of reserves, which could adversely affect our production and our results of operations.
•If the assumptions underlying our reserve estimates are inaccurate or if future events cause us to negatively adjust our previous assumptions, the quantities and value of our reserves, and in turn our financial condition and results of operations, could be adversely affected.
•Existing and further oil and gas development in the Designated Potash Area could impair our potash reserves, which could adversely affect our financial condition or results of operations.
•The mining business is capital intensive, and our inability to fund necessary or desirable capital expenditures could have an adverse effect on our growth and profitability.
Risks Related to Financial Position, Indebtedness and Additional Capital Needs
•The execution of strategic projects could require more time and money than we expect, which could adversely affect our results of operations and financial condition.
•Future indebtedness could adversely affect our financial condition and impair our ability to operate our business.
•Despite our current level of indebtedness, we may incur more debt and undertake additional obligations. Incurring such debt or undertaking such additional obligations could further exacerbate the risks to our financial condition.
•The phase out of the London Interbank Offered Rate ("LIBOR") could adversely affect our financial results.
•Adverse conditions in the global economy and disruptions in the financial markets could negatively affect our results of operations and financial condition.
•Market upheavals due to military actions, terrorist attacks, other catastrophic events, or economic repercussions from those events could reduce our sales or increase our costs.
Risks Related to Compliance, Regulatory and Legal
•Changes in laws and regulations affecting our business, or changes in enforcement practices, could have an adverse effect on our financial condition or results of operations.
•If we are unable to obtain and maintain the required permits, governmental approvals, and leases necessary for our operations, our business could be adversely affected.
•Anti-corruption laws and regulations could subject us to significant liability and require us to incur costs.
Risks Related to the Environment and Climate
•Physical effects of climate change, and climate change legislation, could have a negative effect on us and our customers, and, in turn, our results of operations.
•Environmental laws and regulations could subject us to significant liability and require us to incur additional costs.
Risks Related to Our Common Stock
•The price of our common stock may be volatile and you could lose all or part of your investment.
•The market price of our common stock may be adversely affected by the future issuance and sale of additional shares of our common stock, or by our announcement that the issuances and sales may occur.
•We do not anticipate paying cash dividends on our common stock.
•Provisions in our charter documents and Delaware law may delay or prevent a third party from acquiring us.
•We may issue additional securities, including securities that are senior in right of dividends, liquidation, and voting to our common stock, without your approval, which would dilute your existing ownership interests.
•If securities or industry analysts do not publish research or reports about our business, if they adversely change their recommendations regarding our stock, or if our operating results do not meet their expectations, our stock price could decline.
Risks Related to Our Business
The COVID-19 pandemic has, and may continue to, disrupt our business, including, among other things, demand for our products, our personnel and production processes, each of which has and could continue to materially affect our operations, liquidity, financial condition and results of operations.
The COVID-19 pandemic has, and could continue to, negatively affect our operations, liquidity, financial condition and results of operations. During 2020, measures designed to contain the spread of COVID-19 had a negative impact on the global economy. Oil demand decreased and, as a result, we saw a significant decline in oil and gas activity near our Carlsbad, New Mexico operations. We experienced a significant decrease in the sale of water and other oilfield related products and services, which negatively impacted our overall results. During 2021, many of these restrictions were reduced or removed and overall economic activity and our financial results improved. The situation remains dynamic and subject to rapid and possibly material change, including, but not limited to, changes that may materially affect the demand for our products, our mining operations, and the operations of our customers and supply chain partners. These changes could result in material negative effects on our business, results of operations, financial condition, liquidity position and ability to maintain compliance with our debt covenants.
Our efforts to manage and mitigate the risks may be unsuccessful, and the effectiveness of these efforts depends on factors beyond our control, including the duration and severity of COVID-19 and related variants, the efficacy and adoption of vaccines against COVID-19 and related variants, as well as third party actions taken to contain the spread of COVID-19 and related variants and mitigate public health effects. The rapid development and fluidity of the pandemic precludes any prediction as to the ultimate impact of COVID-19. The full extent of the impact and effects of COVID-19 on our future business, operations, liquidity, financial condition, and results of operations remain uncertain at this time.
Our potash sales are subject to price and demand volatility resulting from periodic imbalances of supply and demand, which could negatively affect our results of operations.
The market for potash is cyclical, and the prices and demand for potash can fluctuate significantly. Periods of high demand, increasing profits, and high-capacity utilization lead to new plant investment and increased production. This growth continues until the market is over-saturated, leading to decreased prices and lower-capacity utilization until the cycle repeats. Global productive capacity remains higher than demand and we expect this will last for at least the next few years, although individual potash producers have, at times, independently suspended production in response to market outlook. As a result of these factors, the prices and demand for potash can be volatile. This volatility can reduce profit margins and negatively affect our results of operations. We sell most of our potash into the spot market in the U.S. In addition, there is no active hedge market for potash as there is for many other commodities. As a result, we do not have protection from this price and demand volatility.
We are working to expand our sales of Trio®, and our sales and results of operations could be negatively impacted if we are unsuccessful in our plans.
One of our strategies is to continue to expand our sales of Trio® in domestic and select international markets. Our expansion efforts may not be successful, which would temper any Trio® sales growth. With respect to international sales, it is difficult to determine if or how international demand and pricing for Trio® may develop. Our international sales often result in lower gross margins than domestic sales due to higher costs. These costs could include higher transportation costs, importation costs, and costs associated with duties, trade requirements, or other import or export control laws and regulations. We also face price pressure and competition in some international markets where substitutes are more prevalent. Any of these items could negatively impact our results of operations. In addition, international sales may occur on an irregular basis, which could cause volatility in our inventories and our results of operations. See also "International sales could present risks to our business."
We may not be successful in our efforts to sustain or expand water sales due to the status of our water rights, challenges to our water rights, changes in the demand for water in the areas around our facilities, or other events, which could adversely impact our financial condition and results of operations.
We have permitted, licensed, declared and partially adjudicated water rights in New Mexico under which we sell water primarily for industrial uses such as in the oil and gas services industry. We continue to work to expand sales of water, especially to support oil and gas development in the Permian Basin near our New Mexico facilities. If there are changes in state or federal regulations regarding oil and gas production or water usage, this could materially impact our ability to monetize our water rights. Third parties regularly challenge our applications to the OSE to change our water rights permits so that we authorized to sell water to oil and gas producers. We may not be successful in our efforts to obtain the requisite permit changes. In many cases, sales of water require governmental permits or approvals. A decision to deny, delay, revoke, or modify a permit or approval could prevent us from selling water, increase the cost to provide water, or result in our having to refund
prepayments that we have received for future water sales. If oil or gas prices decline, if oil and gas development in the Permian Basin decreases, or if demand for fresh water in the Permian Basin declines for other reasons, the demand for water under our water rights could be adversely affected. In addition, we could be required to expend capital to meet customer needs. Any of these events could adversely impact our financial condition and results of operations.
Water rights in New Mexico are subject to a stated place of withdrawal, purpose and place of use. Some of our water right permits, declarations and licenses were originally issued for uses relating to our mining operations. To sell water under these rights for oil and gas development, we must apply for a permit from the OSE to change the point of diversion, purpose and/or place of use of the underlying water rights. The OSE reviews such applications and makes a determination as to the validity of the right and, will approve the proposed change if it determines the requested change will not impair existing water rights, will not be contrary to the conservation of water within the state, and will not be detrimental to the public welfare of the state. In some situations, the OSE can issue a preliminary authorization for the change, which allows for the proposed change to go into effect immediately while pending further administrative review. Such authorizations for water sales are often subject to repayment if the underlying water rights were ultimately found to be invalid. Third parties may protest an application to change a point of diversion, purpose or place of use or a preliminary authorization at minimal cost and frequently do so. Once protested, an administrative process begins, whereby the OSE will ultimately determine if the subject application or preliminary authorization will impair existing water rights, will be contrary to the conservation of water within the state or will be detrimental to the public welfare of the state. The OSE’s findings can be appealed to a New Mexico district court. A significant portion of our water sales are being made under preliminary authorizations issued by the OSE. Additionally, some of our water rights are permitted water rights for which we still need to provide proof of completion of works and proof of beneficial use to the OSE. Please see Note 14 of the Notes to Consolidated Financial Statements for an update on challenges to our water rights.
We may face political and regulatory issues relating to the potential use of the maximum amount of our rights. Any decrease in our water rights could materially impact our ability to monetize our water rights.
A decline in oil and gas drilling or a reduction in the use of potash in drilling fluids could decrease our revenue.
A portion of our revenue comes from the sale of water and potassium chloride for use in oil and gas development. A decline in oil and gas drilling, especially in the Permian Basin, could reduce our sales of water and potassium chloride. For example, the decline in oil and gas drilling in 2020 due to restrictions implemented by local, state and federal authorities in response to the COVID-19 pandemic and the resulting impacts of these restrictions on the global economy as a whole, reduced our sales of water and potassium chloride into industrial markets in 2020. In addition, oil and gas developers are regularly looking for ways to use more produced, or recycled, water instead of fresh water in oil and gas development. Also, there are other products available that have some of the same clay-inhibiting properties as our potassium chloride. These alternative products could temporarily or permanently replace some of our sales of water or potassium chloride. We also have other oilfield product and service offerings, such as caliche and brine products, the sales of which were negatively impacted by the decline in oil and gas development in 2020, and may be further impacted in the future by declines in oil and gas development.
We may alter or expand our operations or continue to pursue acquisitions, which could adversely affect our business if we are unable to manage any expansion or acquisition effectively.
We continue to look for opportunities designed to maximize the value of our existing assets, such as through increased production and sales of water, salt, and brine. For example, in 2019 we purchased water and real property assets in southeastern New Mexico, which we refer to as Intrepid South, in an effort to expand our water sales and other revenue from the oil and gas industry. In addition, we may enter into new or complementary businesses that expand our product offerings beyond our existing assets, which may include leveraging our existing oil and gas businesses in southeast New Mexico and expand into additional oil and gas midstream and upstream activities. For instance, as part of this strategy, in May 2020, we acquired an 11% equity stake in the W.D. Von Gonten Laboratories, a global industry leader in drilling and completion chemistry and a strong supporter of the use of potassium chloride in oil and gas drilling and completion activities. We may also expand into new products or services in our current industry or other industries. However, we may not ultimately be successful in implementing any alteration or expansion initiatives. Further, we may not be able to fully realize any anticipated benefits of these initiatives. Any expansion initiatives may require significant capital investments and those investments may not produce the expected benefits
As part of this growth strategy, we may consider the acquisition of other companies or assets that complement or expand our business. We may not be able to successfully identify suitable acquisition opportunities, prevail against competing potential acquirers, negotiate appropriate acquisition terms, obtain necessary financing, complete proposed acquisitions, successfully integrate acquired businesses or assets into our existing operations, or expand into new markets. An acquisition may require us to use a significant portion of available cash or may result in significant dilution to our stockholders. We may be required to assume unanticipated liabilities or contingencies as part of an acquisition, or we may face substantial costs, delays, or other problems as part of the integration process. In addition, acquired businesses or assets may not achieve the desired
effects or otherwise perform as we expect. We may not realize the synergies that we expect to achieve. Additionally, while we execute these acquisitions and related integration activities, our attention may be diverted from our ongoing operations, which could have a negative impact on our business.
Any of these items could negatively impact our financial condition and results of operations.
Aggressive pricing or operating strategies by our competitors could adversely affect our sales and results of operations.
The potassium-fertilizer industry is concentrated, with a small number of producers accounting for the majority of global production. Many of these producers have significantly larger operations and more resources than we do. These larger producers may have greater leverage in pricing negotiations with customers and transportation providers. They also have a broader product portfolio, which may allow them to offer rebates or bundle products to offer discounts or incentives to gain a competitive advantage. They may also be able to mine their potash or langbeinite at a lower cost due to economies of scale or other competitive advantages. In addition, they may decide to pursue aggressive pricing or operating strategies that disrupt the global and U.S. markets. These disruptions could cause lower prices or demand for our product, which would adversely affect our sales and results of operations.
The seasonal demand for our products, and the resulting variations in our cash flows from quarter to quarter, could have an adverse effect on our results of operations and working capital requirements.
The fertilizer business is seasonal. With respect to domestic sales, we typically experience increased sales during the North American spring and fall application seasons. The degree of seasonality can change significantly from one year to the next due to weather-related shifts in planting schedules and purchasing patterns. We and our customers generally build inventories during low-demand periods of the year to ensure timely product availability during high-demand periods, resulting in increased working capital requirements just before the start of these seasons. If we are unable to accurately predict the timing of demand for our products due to variations in seasonality from year to year, our results of operations and working capital could be adversely affected. Similarly, if we do not have adequate storage capacity to manage varying inventory needs, we may need to reduce production or lower the price at which we sell product, either of which would adversely affect our results of operations.
In mid-2016, we transitioned our East mine to Trio®-only, resulting in an increased supply of Trio®. Previously, Trio® was supply-constrained, which meant that we did not see as much seasonality with respect to purchases as we did for potash. As purchasers have gained increased confidence in our ability to supply this product closer to the traditional spring application season in the U.S., these purchasers have moved to more of a just-in-time purchasing model. As a result, we now experience more traditional seasonality with respect to our domestic Trio® sales, which exposes us to inventory and demand risks similar to those with respect to our potash.
We market Trio® in various countries around the world, all of which have different climates and fertilizer-application patterns. As a result, seasonality in our international Trio® sales may develop, which could cause volatility in our results of operations.
Our Trio® profitability could be affected by market entrants or the introduction of langbeinite alternatives.
Langbeinite is produced by us and one other company from a single resource located in Carlsbad, New Mexico. Additional competition in the market for langbeinite and comparable products exists and could increase in the future. Other companies could seek to create and market chemically similar alternatives to langbeinite, some of which could be superior to langbeinite, or less costly to produce. In addition, companies sometimes blend several nutrients to obtain a product with similar agronomic benefits as langbeinite. The market for langbeinite and our Trio® sales could be affected by the success of these and other products that are competitive with langbeinite, which could adversely affect the viability of our Trio® business and our results of operations and financial condition. Further, recent increases in the supply of langbeinite by us and the other producer may continue to pressure the sales price of Trio®.
International sales could present risks to our business.
Sales of Trio® into international markets often require more resources and management attention than domestic sales and may subject us to economic, regulatory, and political risks that are different from those in the United States. These risks include accounts receivable collection; the need to adapt marketing and sales efforts for specific countries; new and different sources of competition; disputes and losses associated with overseas shipping; tariffs, export controls, and trade duties; additional time and effort to obtain product certifications; adverse tax consequences; restrictions on the transfer of funds; changes in legal and regulatory requirements or import policies; compliance with potentially unfamiliar local laws and customs; and political and economic instability. International sales may also be subject to fluctuations in currency exchange rates, which could increase the price of our products outside the United States and expose us to foreign currency exchange rate risk. Certain
international markets require significant time and effort on the part of management to develop relationships and gain market acceptance for our products. Overall, there are additional logistical requirements associated with international sales, which may increase the time between production and our ability to recognize related revenue. Our failure to manage any of these risks successfully could harm our future international operations and our overall business.
If potash or Trio® prices decline, or oil and gas activity declines, we could be required to record write-downs of our long-lived and indefinite-lived assets, which could adversely affect our results of operations and financial condition.
We evaluate our long-lived assets for impairment when events or changes in circumstances indicate that the related carrying amount may not be recoverable. Impairment is considered to exist if an asset's total estimated future cash flows on an undiscounted basis are less than the carrying amount of the related asset. An impairment loss is measured and recorded based on the discounted estimated future cash flows.
We also have certain indefinite-lived intangible assets that we evaluate for impairment at least annually or more frequently when events or changes in circumstances indicate the fair value may have changed. An impairment loss is measured and recorded based on the current fair value of the asset.
Although we believe the carrying values of our long-lived and indefinite-lived assets were realizable as of the balance sheet dates, future events could cause us to conclude otherwise. These future events could include further significant and sustained declines in potash or Trio® prices, further significant or sustained declines in water prices and demand, or higher production and operating costs. Further, based on our analysis of the profitability of any of our facilities, we may decide to terminate or suspend operations at additional facilities. These events could require a further write-down of the carrying value of our assets, which would adversely affect our results of operations and financial condition.
If we are required to write down the value of our inventories, our financial condition and results of operations would be adversely affected.
We carry our inventories at the lower of cost or net realizable value. In periods when the market prices for our products fall below our cost to produce them and the lower prices are not expected to be temporary, we are required to write down the value of our inventories. Any write-down of our inventory would adversely affect our financial condition and results of operations, possibly materially.
Weakening of foreign currencies against the U.S. dollar could lead to lower domestic potash prices, which would adversely affect our results of operations. Currency fluctuations could cause our results of operations to fluctuate.
The U.S. imports the majority of its potash, including from Canada, Russia, and Belarus. If the local currencies for foreign suppliers strengthen in comparison to the U.S. dollar, foreign suppliers realize a smaller margin in their local currencies unless they increase their nominal U.S. dollar prices. Strengthening of these local currencies therefore tends to support higher U.S. potash prices as the foreign suppliers attempt to maintain their margins. However, if these local currencies weaken in comparison to the U.S. dollar, foreign suppliers may lower prices to increase sales volume while again maintaining a margin in their local currency. Changes in the strength of the U.S. dollar compared to other currencies could cause our sales prices and results of operations to decrease or fluctuate significantly.
Our business depends on skilled and experienced workers, and our inability to find and retain quality workers could have an adverse effect on our development and results of operations.
The success of our business depends on our ability to attract and retain skilled managers, engineers, and other workers. At times, we may not be able to find or retain qualified workers. In particular, the labor market around Carlsbad, New Mexico, is competitive and employee turnover is generally high. In that market, we compete for experienced workers with several other employers, including natural resource and hazardous waste facilities, oil and gas producers, and another producer of langbeinite. If we are not able to attract and retain quality workers, the development of our business could suffer, or we could be required to raise wages to keep our employees, hire less qualified workers, or incur higher training costs. These risks may be exacerbated in times when we need to reduce our workforce due to economic conditions. The occurrence of any of these events could have an adverse effect on our results of operations. For example, in mid-2016, we idled our West mine and transitioned our East mine to Trio®-only, resulting in our laying off a significant number of skilled employees in New Mexico. This may make it more difficult for us to re-hire skilled employees in the future.
Increases in the prices of energy and other important materials used in our business, or disruptions to their supply, could adversely impact our sales, results of operations, or financial condition.
Natural gas, electricity, chemicals, diesel, and gasoline are key materials that we purchase and use in the production of our products. The prices of these commodities are volatile.
Our sales and profitability are impacted by the price and availability of these materials. A significant increase in the price of these materials that is not recovered through an increase in the price of our products, or an extended interruption in the supply of these materials to our production facilities, could adversely affect our results of operations or financial condition. In addition, high natural gas or other fuel costs could increase input costs for end-users of our products, which could cause them to spend less on our products.
Increased costs could affect our per-ton profitability.
A substantial portion of our operating costs is comprised of fixed costs that do not vary based on production levels. These fixed costs include labor and benefits, base energy usage, property taxes, insurance, maintenance expenditures, and depreciation. Any increase in fixed costs or decrease in production generally increases our per-ton costs and correspondingly decreases our per-ton operating margin. We operate our East Plant at less than full capacity in order to curtail our Trio® production to match expected demand and manage inventory levels. A significant increase in costs at any of our facilities could have an adverse effect on our profitability and cash flows, particularly during periods of lower potash and Trio® prices.
A shortage of railcars or trucks for transporting our products, increased transit times, or interruptions in railcar or truck transportation could result in customer dissatisfaction, loss of sales, higher transportation or equipment costs, or disruptions in production.
We rely heavily upon truck and rail transportation to deliver our products to our customers. In addition, the cost of transportation is an important component of the price of our products. A shortage of trucks or railcars for carrying product or increased transit times due to accidents, highway or railway disruptions, congestion, high or compressed demand, labor disputes, adverse weather, natural disasters, changes to transportation systems, or other events could prevent us from making timely delivery to our customers or lead to higher transportation costs. As a result, we could experience customer dissatisfaction or a loss of sales. Similarly, disruption within the transportation systems could negatively affect our ability to obtain the supplies and equipment necessary to produce our products. We may also have difficulty obtaining access to vessels to deliver our products to overseas customers.
We rely on our management personnel for the development and execution of our business strategy, and the loss of one or more members of our management team could harm our business.
Our management personnel have significant relevant industry and company-specific experience. Our senior management team has developed and implemented first-of-their-kind processes and other innovative ideas that are important to our business. If we are unable to retain these individuals, our operations could be disrupted and we may be unable to achieve our business strategies and grow effectively. We do not currently maintain "key person" life insurance on any of our management personnel.
We have less product diversification than nearly all of our competitors, which could have an adverse effect on our financial condition and results of operations.
A significant portion of our revenue comes from the sale of potash and langbeinite, whereas nearly all of our competitors are diversified, primarily into nitrogen- or phosphate-based fertilizer businesses or other chemical or industrial businesses. In addition, a majority of our sales are to customers in the U.S., and generally these customers are concentrated in key geographies where we have a freight advantage. As a result, we could be impacted more acutely by factors affecting our industry or the regions in which we operate than we would if our business was more diversified and our sales more global. A decrease in the demand for potash and langbeinite would have an adverse effect on our financial condition and results of operations. Similarly, in periods when production exceeds demand, the price at which we sell our potash and langbeinite and our sales volumes would likely fall, which would adversely affect our results of operations and financial condition more than our diversified competitors.
Heavy precipitation or low evaporation rates at our solar solution mines could impact our potash production at those facilities, which could adversely affect our sales and results of operations.
All of our potash production comes from our solar solution mines. These facilities use solar evaporation ponds to form potash crystals from brines. Weather conditions at these facilities could negatively impact potash production. For example, heavy rainfall in September and October, just after the evaporation season ends, can reduce the amount of potash we produce in that year or the following year by causing the potash crystals to dissolve and consume pond capacity. Similarly, lower‑than‑average temperatures or higher-than-average seasonal rainfall would reduce evaporation rates and therefore impact production. We experienced significant rainfall in the summer of 2019 at our Wendover facility which reduced the product available for sale in 2020, and at our HB facility in the summer of 2021, which led to fewer tons available for sale in the second half of 2021 and we expect will result in fewer tons than our historical average available in the spring of 2022. If we experience heavy rainfall or low evaporation rates at any of our solar solution mines, we would have less potash available for sale, and our
sales and results of operations would be adversely affected. Reduced potash available for sale could also affect our ability to produce and sell byproducts such as salt and magnesium chloride.
Inflows of water into our langbeinite mine from heavy rainfall or groundwater could result in increased costs and production downtime and could require us to abandon the mine, any of which could adversely affect our results of operations.
Major weather events such as heavy rainfall can result in water inflows into our underground, langbeinite mine. The presence of water-bearing strata in many underground mines carries the risk of water inflows into the mines. If we experience water inflows at our langbeinite mine, our employees could be injured and our equipment and mine shafts could be seriously damaged. We could be forced to shut down the mine temporarily, potentially resulting in significant production delays, and spend substantial funds to repair or replace damaged equipment. Inflows may also destabilize the mine shafts over time, resulting in safety hazards for employees and potentially leading to the permanent abandonment of the mine.
A significant disruption to our information technology systems could adversely affect our business and operating results.
We rely on a variety of information technology and automated operating systems to manage or support our operations. In particular, we depend on our information technology systems for a variety of functions, including, but not limited to, financial reporting, inventory management, procurement, invoicing and email. We also have access to, and we create and store, sensitive data, including our proprietary business information and that of our customers, and personally identifiable information of our employees. The proper functioning of these systems and the security of this data is critical to the efficient operation and management of our business. In addition, these systems could require modifications or upgrades as a result of technological changes or growth in our business. These changes could be costly and disruptive to our operations and could impose substantial demands on management time. Our systems, and those of third-party providers, also could be vulnerable to damage or disruption caused by catastrophic events, power outages, natural disasters, computer system or network failures, viruses or malware, physical or electronic break-ins, unauthorized access, and cyber-attacks. Although we take steps to secure our systems and electronic information, these cybersecurity measures may not be adequate. Any security breaches could compromise our networks and the information stored on them could be improperly accessed, disclosed, lost or stolen. Any such access, disclosure or other loss of information could disrupt our operations and the services we provide to customers, damage our reputation or our relationships with our customers or result in legal claims or proceedings, any of which could adversely affect our business, reputation, and operating results.
Our business may be adversely affected by union activities.
Hourly employees at our Wendover facility are represented by a labor union. These employees represent approximately 9% of our workforce. Our current collective bargaining agreement with the union expires on May 31, 2023. Although we believe that our relations with our unionized employees are good, we may not be successful in negotiating a new collective bargaining agreement as a result of general economic, financial, competitive, legislative, political, and other factors beyond our control. Any new agreement could result in a significant increase in our labor costs. In addition, a breakdown in negotiations or failure to timely enter into a new collective bargaining agreement could materially disrupt our Wendover operations.
From time to time, efforts have been made to unionize employees at our other facilities. Additional unionization efforts could disrupt our business, consume management attention, or increase our operating costs. In addition, if these efforts were successful, we could experience increased labor costs, an increased risk of work stoppages, and limits on our flexibility to run our business in the most efficient manner to remain competitive.
We will be subject to a number of uncertainties while we pursue the initial public offering of Intrepid Acquisition Corporation I (“IACI”), and during the timeframe when IACI pursues an initial business combination, which could adversely affect our business, financial condition, results of operations, cash flows and stock price.
While we have announced our intention to pursue an initial public offering of IACI, a newly formed special purpose acquisition company (“SPAC”) and our indirect subsidiary, there has recently been heightened regulatory focus on SPACs, including recently issued accounting guidance, resulting in substantial uncertainty in the SPAC markets. Pursuing the initial public offering of a SPAC in this uncertain environment has resulted in, and may continue to result in, additional costs as instrument terms are reevaluated, delays in the SPAC initial public offering process and attention from our management and employees. There is no assurance that we will be able to consummate IACI’s initial public offering on favorable terms or at all. Further, in the event the initial public offering of IACI is completed, the accounting guidance applicable to SPACs could subsequently be revisited, potentially necessitating restatements of IACI’s financial statements, which could then impact and necessitate restatements of our financial statements, as well as leading to delays as IACI pursues a suitable business transaction and requiring us to devote extensive management and employee attention and resources to these matters.
If we are unable to consummate IACI’s initial public offering on favorable terms or at all, or if we complete the initial public offering and IACI is unable to consummate a suitable business transaction during the prescribed time period set forth in the terms of IACI’s initial public offering, we may experience negative reactions from the financial markets and from our stockholders. In addition, in the event that IACI is able to find a suitable initial business combination, or if the initial business combination is unsuccessful, there is no assurance that we will realize the anticipated value from such transaction. Further, we will be required to devote significant management and employee attention and resources to matters relating to the initial public offering and the initial business combination. These matters have the potential to disrupt us from conducting business operations or pursuing other business strategies and could adversely affect our business, financial condition, results of operations and cash flows.
Risks Related to Our Industry
Changes in the agricultural industry could exacerbate the cyclical nature of the prices and demand for our products or adversely affect the markets for our products.
Farmers attempt to apply the optimum amounts of fertilizer to maximize their economic returns. A farmer's decision about the application rate for each fertilizer, or the decision to forgo the application of a fertilizer, particularly potash and Trio®, varies from year to year depending on a number of factors. These factors include crop types, crop prices, weather patterns, fertilizer and other crop input costs, and the level of crop nutrients remaining in the soil following the previous harvest. Farmers are more likely to increase application rates of fertilizers when crop prices are relatively high, fertilizer and other crop input costs are relatively low, or the level of crop nutrients remaining in the soil is relatively low. Conversely, farmers are likely to reduce application of fertilizers when farm economics are weak or declining or the level of crop nutrients remaining in the soil is relatively high. This variability in application rates can impact the cyclical nature of the prices and demand for our products. In addition, farmers may buy and apply potash or Trio® in excess of current crop needs, which results in a build-up of potassium in the soil that can be used by crops in subsequent crop years. If this occurs, demand for our products could be delayed to future periods.
State and federal governmental policies, including farm and ethanol subsidies and commodity support programs, may also influence the number of acres planted, the mix of crops planted, and the use of fertilizers. In addition, there are various city, county, and state initiatives to regulate the use and application of fertilizers due to various environmental concerns. If U.S. agricultural production or fertilizer use decreased significantly due to one or more of these factors, our results of operations could be adversely affected.
Mining is a complex process that frequently experiences production disruptions, which could adversely affect our results of operations.
The process of mining is complex. Production delays can occur due to equipment failures, unusual or unexpected geological conditions, environmental hazards, acts of nature, and other unexpected events or problems. Furthermore, production is dependent upon the maintenance and geotechnical structural integrity of our tailings and storage ponds. The amounts that we are required to spend on maintenance and repairs may be significant.
Our East mine, surface, and support facilities are over 50 years old. As mining progresses at an underground mine, operations typically move further away from the shafts and, despite modernization through sustaining capital, fixed assets may require increased repair or refurbishment. These conditions increase the exposure to higher operating costs or the increased probability of incidents.
Mining is a hazardous process, and accidents could result in significant costs or production delays.
The process of mining is hazardous and involves various risks and hazards that can result in serious accidents. If accidents or unforeseen events occur, or if our safety procedures are not effective, we could be subject to liabilities arising out of personal injuries or death, our operations could be interrupted, or we could be required to shut down or abandon affected facilities. Accidents could cause us to expend significant amounts to remediate safety issues or repair damaged facilities.
Existing or expanded oil and gas development near our mines could result in methane gas leaking from an oil and gas well into our mines. We test our mines regularly for methane gas. However, unlike coal mines, our mines are not constructed or equipped to deal with methane gas. Any intrusion of methane gas into our mines could cause a fire or an explosion resulting in loss of life or significant property damage or could require the suspension of all mining operations until the completion of extensive modifications and re-equipping of the mine. The costs of modifying our mines and equipment could make it uneconomical to reopen our mines. You can find more information about the co-development of potash and oil and gas resources near our New Mexico facilities under the risk factor below entitled "-Existing and further oil and gas development in the Designated Potash Area could impair our potash reserves, which could adversely affect our financial condition or results of operations."
The grade of ore that we mine could vary from our projections due to the complex geology and mineralogy of reserves, which could adversely affect our production and our results of operations.
Ore bodies have complex geology. Our production is affected by the mineral content and other mineralogy of the ore. Our projections of ore grade may not be accurate. There are numerous uncertainties inherent in estimating ore grade, including many factors beyond our control. As the grade of our remaining ore reserves decreases over time, we need to process more ore to produce the same amount of saleable-grade product, increasing our costs and slowing our production. In addition, there are few opportunities to acquire more reserves in the areas around our current operations. If we are unable to process more ore to maintain current production levels, if the processing of more ore materially increases our costs, or if our ore grade projections are not accurate, our results of operations would be adversely affected.
If the assumptions underlying our reserve estimates are inaccurate or if future events cause us to negatively adjust our previous assumptions, the quantities and value of our reserves, and in turn our financial condition and results of operations, could be adversely affected.
There are numerous uncertainties inherent in estimating our potash and langbeinite reserves. As a result, our reserve estimates necessarily depend upon a number of assumptions, including the following:
•geologic and mining conditions, which may not be fully identified by available exploration data and may differ from our experiences in areas where we currently mine or operate
•future potash and Trio® prices, operating costs, capital expenditures, royalties, severance and excise taxes, and development and reclamation costs
•future mining technology improvements
•the effects of governmental regulation
•variations in mineralogy
In addition, because reserves are estimates built on various assumptions, they cannot be audited for the purpose of verifying exactness. It is only after extraction that reserve estimates can be compared to actual values to adjust estimates of the remaining reserves. If any of the assumptions that we make in connection with our reserve estimates are incorrect, the amounts of potash and langbeinite that we are able to economically recover from our mines could be significantly lower than our reserve estimates. In addition, we periodically review the assumptions underlying our reserve estimates. If future events cause us to negatively adjust our previous assumptions, our reserve estimates could be adversely affected. In any of these events, our financial condition and results of operations could be adversely affected.
Existing and further oil and gas development in the Designated Potash Area could impair our potash reserves, which could adversely affect our financial condition or results of operations.
The U.S. Department of the Interior regulates the development of federal mineral resources-both potash and oil and gas-on federal lands in the Designated Potash Area. This 497,000-acre region outside of Carlsbad, New Mexico, includes all of our New Mexico operations and facilities. In 2012, the U.S. Department of the Interior issued an updated order that provides guidance to the U.S. Bureau of Land Management ("BLM") and industry on the co-development of these resources.
It is possible that oil and gas drilling in this area could limit our ability to mine valuable potash and langbeinite reserves or mineralized deposits because of setbacks from oil and gas wells and the establishment of unminable buffer areas around oil or gas wells. It is also possible that the BLM could determine that the size of these unminable buffer areas should be larger than they are currently, which could impact our ability to mine our reserves. We review applications for permits to drill oil and gas wells as they are publicly disclosed by the BLM and the State of New Mexico. When appropriate, we protest applications for drilling permits that we believe should not be drilled consistent with the operative federal and state rules and that could impair our ability to mine our reserves or put at risk the safety of our employees. We may not prevail in these protests or be able to prevent wells from being drilled in the vicinity of our reserves. If, notwithstanding our protests and appeals, a sufficient number of wells are drilled through or near our reserves, our reserves could be significantly impaired, which could adversely affect our financial condition or results of operations.
The mining business is capital intensive, and our inability to fund necessary or desirable capital expenditures could have an adverse effect on our growth and profitability.
The mining business is capital intensive. We may find it necessary or desirable to make significant capital expenditures in the future to sustain or expand our existing operations and may not have, or have access to, the financial resources to pursue these expenditures. If costs associated with capital expenditures increase or if our earnings decrease significantly or we do not have access to the capital markets, we could have difficulty funding any necessary or desirable capital expenditures at an acceptable rate or at all. This could limit the expansion of our production or make it difficult for us to sustain
our existing operations at optimal levels. Increased costs for capital expenditures could also have an adverse effect on the profitability of our existing operations and returns from our most recent strategic projects.
Risks Related to Financial Position, Indebtedness and Additional Capital Needs
The execution of strategic projects could require more time and money than we expect, which could adversely affect our results of operations and financial condition.
From time to time, we invest in strategic projects. The completion of these projects could require significantly more time and money than we expect. In some cases, the construction or commissioning processes could force us to slow or shut down normal operations at the affected facility for a period of time, which would cause lower production volume and higher production costs per ton. In addition, our management team and other employees may be required to spend a significant amount of time addressing strategic projects, which could mean that our normal operations receive less time and attention. As we proceed with one or more of these strategic projects, we may not realize the expected benefits despite substantial investments, they may cost significantly more than we expect, or we may encounter additional risks that we did not initially anticipate.
Future indebtedness could adversely affect our financial condition and impair our ability to operate our business.
As of December 31, 2021, we had no outstanding borrowings under a revolving credit facility that allows us to borrow up to $75 million. We may incur additional indebtedness in the future. The agreements governing the credit facility restrict, but do not prohibit, us from incurring additional indebtedness.
Future indebtedness could have important consequences, including the following:
•it could limit our ability to borrow additional money or sell additional shares of common stock to fund our working capital, capital expenditures, and debt service requirements
•it could limit our flexibility in planning for, or reacting to, changes in our business
•we could be more highly leveraged than some of our competitors, which could place us at a competitive disadvantage
•it could make us more vulnerable to a downturn in our business or the economy
•it could require us to dedicate a substantial portion of our cash flows from operations to the repayment of our indebtedness, thereby reducing the availability of our cash flows for other purposes
•it could adversely affect our business and financial condition if we default on or are unable to service our indebtedness, are unable to refinance such indebtedness on favorable terms or are unable to obtain additional financing, as needed
Our debt agreement contains financial and other restrictive covenants. For example, the agreement includes financial covenants that require us to maintain a maximum leverage ratio (as these ratios are defined under the agreement). For more information about financial covenants, see Item 7. "Management's Discussion and Analysis of Financial Condition and Results of Operations - Liquidity and Capital Resources."
These covenants could limit our ability to engage in activities that are in our long-term best interests. Our failure to comply with these covenants would result in an event of default that, if not waived, could result in the acceleration of all outstanding indebtedness. The credit facility is secured by substantially all of our assets. As such, an event of default could also result in our lenders foreclosing on some or all of our assets.
The credit facility expires in 2024. In the future, we may be unable to obtain new financing or refinancing on acceptable terms.
Despite our current level of indebtedness, we may incur more debt and undertake additional obligations. Incurring such debt or undertaking such additional obligations could further exacerbate the risks to our financial condition.
Although the agreement governing our indebtedness contains restrictions on our incurrence of additional indebtedness, these restrictions are subject to a number of qualifications and exceptions and the indebtedness incurred in compliance with these restrictions could increase. To the extent new debt is added to our current debt levels, the risks to our financial condition would increase.
While the agreement governing our indebtedness also contains restrictions on our ability to make loans and investments, these restrictions are subject to a number of qualifications and exceptions, and the investments incurred in compliance with these restrictions could be substantial.
The phase out of the London Interbank Offered Rate ("LIBOR") could adversely affect our financial results.
Borrowings under our revolving credit facility bear interest at LIBOR plus an applicable margin. In July 2017, the United Kingdom's Financial Conduct Authority (the authority that regulates LIBOR) announced that it intends to phase out LIBOR by the end of 2021. LIBOR is in the process of being discontinued. While certain U.S. Dollar LIBOR settings will
continue to be published on the current basis until June 30, 2023, all other LIBOR settings either are no longer being published or are being published only for a limited time and only on a “synthetic” basis (i.e., not on the basis of submissions made by panel banks). The regulator of the administrator of LIBOR has prohibited any new use of LIBOR by firms subject to its supervision, and certain regulators in the United States have stated that no new contracts using U.S. Dollar LIBOR should be entered into after 2021. In light of these recent announcements, the future of LIBOR at this time is uncertain and any changes in the methods by which LIBOR is determined or regulatory activity related to LIBOR’s phaseout could cause LIBOR to perform differently than in the past or cease to exist.
At this time, the Alternative Reference Rates Committee, a steering committee comprised of large U.S. financial institutions convened by the U.S. Federal Reserve, has recommended the Secured Overnight Financing Rate (“SOFR”) as a more robust reference rate alternative to U.S. Dollar LIBOR. SOFR is calculated based on short-term repurchase agreements, backed by Treasury securities. SOFR is observed and backward looking, which stands in contrast with LIBOR under the current methodology, which is an estimated forward-looking rate and relies, to some degree, on the expert judgment of submitting panel members. Given that SOFR is a secured rate backed by government securities, it is a rate that does not take into account bank credit risk, as is the case with LIBOR. SOFR is therefore likely to be lower than LIBOR and is less likely to correlate with the funding costs of financial institutions. Because of these and other differences, there is no assurance that SOFR will perform in the same way as LIBOR would have performed at any time, and there is no guarantee that it is a comparable substitute for LIBOR. Whether or not SOFR attains market traction as a LIBOR replacement tool remains in question and the future of LIBOR at this time is uncertain.
The agreement governing our revolving credit facility is indexed to USD-LIBOR and we are monitoring this activity and evaluating the related risks. However, the consequences of the adoption of any such alternative reference rates cannot be predicted and could have an adverse impact on the amount of interest and commitment fees that we pay under the agreement governing our revolving credit facility. Likewise, the unavailability of LIBOR may have an adverse impact on interest rates and other financing costs under other debt instruments and other financial obligations of ours, as well as the market value of and the payments we receive under any LIBOR-linked securities or investments that we may own from time to time. In addition, financial markets generally may be adversely affected by the discontinuation of LIBOR, the uncertainties regarding its discontinuation, the alternative reference rates that are being or may be used in place of LIBOR and other issues related to LIBOR. Any of the foregoing could adversely affect our results of operations and financial condition.
At this time, it is not possible to predict the effect of any such changes, any establishment of alternative reference rates or any other reforms to LIBOR that may be enacted in the United Kingdom or elsewhere. Uncertainty as to the nature of such potential changes, alternative reference rates, including SOFR, or other reforms may adversely affect the trading market for LIBOR-based securities. Furthermore, we may need to renegotiate our revolving credit facility which expires on August 1, 2024 and utilizes LIBOR as a factor in determining the interest rate to replace LIBOR with the new standard that is established. There is currently no definitive information regarding the future utilization of LIBOR or of any particular replacement rate. As such, potential effect of any such event on our business, financial condition and results of operations cannot yet be determined.
Adverse conditions in the global economy and disruptions in the financial markets could negatively affect our results of operations and financial condition.
Global economic volatility and uncertainty can create uncertainty for farmers and customers in the geographic areas where we sell our products. If farmers reduce, delay, or forgo their potash and Trio® purchases due to this uncertainty, our results of operations would be adversely affected. Moreover, volatility and disruptions in the financial markets could limit our customers' ability to obtain adequate financing or credit to purchase and pay for our products, which would decrease our sales volume and increase our risk of non-payment by customers. Changes in governmental banking, monetary, and fiscal policies to restore liquidity and increase credit availability may not be effective. It is difficult to determine the extent of economic and financial market problems and the many ways in which they could negatively affect our customers and business. In addition, if we are required to raise additional capital or obtain additional credit during an economic downturn, we could be unable to do so on favorable terms or at all.
Market upheavals due to military actions, terrorist attacks, other catastrophic events, or economic repercussions from those events could reduce our sales or increase our costs.
Actual or threatened armed conflicts, terrorist attacks, military or trade disruptions, or other catastrophic events affecting the areas where we or our competitors do business could disrupt the global market for potassium-based products. As a result, our competitors may increase their sales efforts in our geographic markets and pricing of our products could suffer. If this occurs, we could lose sales to our competitors or be forced to lower our prices. In addition, due to concerns related to terrorism or the potential use of certain fertilizers as explosives, local, state, and federal governments could implement new regulations impacting the production, transportation, sale, or use of potassium-based products. These new regulations could result in lower sales or higher costs.
Risks Related to Compliance, Regulatory and Legal
Changes in laws and regulations affecting our business, or changes in enforcement practices, could have an adverse effect on our financial condition or results of operations.
We are subject to numerous federal and state laws and regulations covering a wide variety of business practices. Changes in these laws or regulations could require us to modify our operations, objectives, or reporting practices in ways that adversely impact our financial condition or results of operations. In addition, new laws and regulations, or new interpretations of or enforcement practices with respect to existing laws and regulations, could similarly impact our business.
For example, we are subject to significant regulation under MSHA and OSHA. High-profile mining accidents could prompt governmental authorities to enact new laws and regulations that apply to our operations or to more strictly enforce existing laws and regulations. See also “Environmental laws and regulations could subject us to significant liability and require us to incur additional costs.”
If we are unable to obtain and maintain the required permits, governmental approvals, and leases necessary for our operations, our business could be adversely affected.
We hold numerous environmental, mining, safety, and other permits and governmental approvals authorizing the operations at each of our facilities. A decision by a governmental agency to deny or delay a new or renewed permit or approval, or to revoke or substantially modify an existing permit or approval, could prevent or limit us from continuing our operations at the affected facility, which could have an adverse effect on our business, financial condition, and results of operations. In addition, we could be required to expend significant amounts to obtain these permits, approvals, and leases, or we could be required to make significant capital investments to modify or suspend our operations at one or more of our facilities.
Any expansion of our existing operations would require us to secure the necessary environmental and other permits and approvals. We may not be able to obtain these permits and approvals in a timely manner or at all. In addition, the federal government must consider and study a project's likely environmental impacts. Based on the federal government's conclusion, it could require an environmental assessment or an environmental impact statement as a condition of approving a project or permit, which could result in significant time delays and costs. Furthermore, many of our operations take place on land that is leased from federal and state governmental authorities. Expansion of our existing operations could require securing additional federal and state leases. We may not be able to obtain or renew these leases on favorable terms or at all. In addition, our existing leases generally require us to commence mining operations within a specified time frame and to continue mining in order to retain the lease. The loss or non-renewal of a lease could adversely affect our ability to mine the associated reserves.
Also, certain of our existing leases require us to make royalty payments based on the revenue generated by the potash, langbeinite, water, or byproducts that we extract from the leased land. The royalty rates are subject to change whenever we renew our leases, which could lead to significant increases in these rates. As of December 31, 2021 approximately 20% of our state, federal and private lease acres at our New Mexico facilities (including leases at the HB and North mines) and 43% of our state and federal lease acres at our Utah operations will be up for renewal within the next five years. Increases in royalty rates would reduce our profit margins and, if the increases were significant, would adversely affect our results of operations. Reporting of royalties is subject to periodic audits by federal and state officials. The Office of Natural Resources Revenue ("ONRR") completed their draft audit report of our New Mexico royalty reporting in September 2019. As of February 2022, we are continuing to progress on the audit in cooperation with ONRR.
Anti-corruption laws and regulations could subject us to significant liability and require us to incur costs.
As a result of our international sales, we are subject to the U.S. Foreign Corrupt Practices Act (the "FCPA") and other laws that prohibit improper payments or offers of payments to foreign governments and their officials for the purpose of obtaining or retaining business. Our international activities create the risk of unauthorized payments or offers of payments in violation of the FCPA or other anti-corruption laws by one of our employees, consultants, sales agents, or distributors even though these persons are not always subject to our control. Although we have implemented policies and training designed to promote compliance with these laws, these persons may take actions in violation of our policies. Any violations of the FCPA or other anti-corruption laws could result in significant civil or criminal penalties and have an adverse effect on our reputation.
Risks Related to the Environment and Climate
Physical effects of climate change, and climate change legislation, could have a negative effect on us and our customers, and, in turn, our results of operations.
The prospective impact of climate change on our operations and our customers’ operations remains uncertain, but the physical effects of climate change could have an adverse effect on us and our customers as experts believe that climate change may be associated with more extreme weather conditions. These effects could include, but may not be limited to, changes in regional weather patterns, including drought and rainfall levels, timing and duration of wintry precipitation and snow events,
water availability, sea levels, storm patterns and intensities and temperature levels, including increased volatility in seasonal temperatures via excessively hot or cold temperatures. These extreme weather conditions could vary by geographic location.
Severe climate change could have an adverse effect on our costs, production, or sales, especially with respect to our solar operations, which require hot, arid summer weather conditions. Prolonged periods of precipitation or cooler weather during the evaporation season could reduce evaporation rates, leading to decreases in our production levels. Similarly, drought or decreased mountain snowfall and associated freshwater run-off could change brine levels, impacting our mineral harvesting process at our Wendover facility. The occurrence of these events at our solar operations could lead to decreased production levels, increased operating costs and require us to make significant additional capital expenditures. Furthermore, weather conditions have historically caused volatility in the agricultural industry and, as a result, in our results of operations, by causing crop failures or significantly reduced harvests, which can adversely affect application rates, demand for our products and our customers’ creditworthiness. Weather conditions can also lead to drought or wild fires, which could adversely impact growers’ crop yields and the uptake of our products, which would reduce the need for application of our products for the following planting season, which could result in lower demand for our products and negatively impact the prices of our products. Finally, salt and magnesium chloride sales into the deicing market and our ability to utilize certain water rights for sale into oil and gas markets may be adversely affected by weather conditions in our markets. Any prolonged change in weather patterns in our markets, as a result of climate change or otherwise, could have a material impact on the results of our operations. In addition, in recent years, the United States Congress has considered legislation to reduce emissions of greenhouse gases (“GHGs”). These initiatives could restrict our or our customers’ operations, require us or our customers to make changes in our respective businesses that would increase our operating costs, reduce our efficiency or limit our output, require us to make capital improvements to our facilities, increase our energy, raw material and transportation costs or limit their availability, or otherwise materially adversely affect our financial condition and results of operations. As of the date of this Annual Report on Form 10-K, it appears unlikely that comprehensive climate legislation will be passed by either house of Congress in the near future, although energy legislation and other regulatory initiatives are expected to be proposed that may be relevant to GHG emissions issues. In addition, a number of states are addressing GHG emissions, primarily through the development of emission inventories or regional GHG cap and trade programs. Depending on the particular program, we and our customers could be required to control GHG emissions or to purchase and surrender allowances for GHG emissions resulting from our operations.
Independent of Congress, the Environmental Protection Agency ("EPA") has adopted regulations controlling GHG emissions under its existing authority under the Clean Air Act (the “CAA”). For example, following its findings that emissions of GHGs present an endangerment to human health and the environment because such emissions contributed to warming of the earth’s atmosphere and other climate changes, the EPA has adopted regulations under existing provisions of the CAA that, among other things, establish construction and operating permit reviews for GHG emissions from certain large stationary sources that are already potential major sources for conventional pollutants. In addition, the EPA has adopted rules requiring the monitoring and reporting of GHG emissions from specified production, processing, transmission and storage facilities in the United States on an annual basis.
Further, in December 2015, over 190 countries, including the United States, reached an agreement to reduce global GHG emissions, also known as the Paris Agreement. The Paris Agreement entered into force in November 2016 after more than 170 nations, including the United States, ratified or otherwise indicated their intent to be bound by the agreement. After previously withdrawing, the United States rejoined the Paris Agreement in January 2021. Actions taken by the United States and other countries to implement the Paris Agreement or otherwise impose regulations on our industry or our customers’ industries aimed at reducing GHG emissions could have an adverse effect on our business.
It is also possible that future legislation or regulation addressing climate change, including in response to the Paris Agreement or any new international agreements, could adversely affect our operations, energy, raw material and transportation costs, results of operations, liquidity or capital resources, and these effects could be material or adversely impact us. In addition, to the extent climate change restrictions imposed in countries where our competitors operate, such as Canada, Russia, and Belarus, are less stringent than in the United States, our competitors could gain cost or other competitive advantages over us.
We have also made certain public statements regarding our commitment to the environment and our focus on protecting the environments, resources, and ecosystems surrounding our locations. Although we intend to work closely with communities and make it a priority to protect the natural resources surrounding our operation, we may be required to expend significant resources to do so, which could increase our operational costs. Further, there can be no assurance of the extent to which our goals will be achieved, or that any future investments we make in furtherance of achieving such target and goal will meet investor expectations or legal standards, if any, regarding sustainability performance. Moreover, we may determine that it is in the best interest of our Company and our stockholders to prioritize other business, social, governance or sustainable investments over the achievement of our current plans based on economic, technological developments, regulatory and social factors, business strategy or pressure from investors, activist groups or other stakeholders. If we are unable to meet these commitments, then we could incur adverse publicity and reaction from investors, activist groups or other stakeholders, which
could adversely impact the perception of us and our products and services by current and potential customers, as well as investors, which could in turn adversely impact our results of operations.
Environmental laws and regulations could subject us to significant liability and require us to incur additional costs.
We are subject to many environmental, safety, and health laws and regulations, including laws and regulations relating to mine safety, mine land reclamation, remediation of hazardous substance releases, and discharges into the soil, air, and water.
Our operations, as well as those of our predecessors, have involved the use and handling of regulated substances, hydrocarbons, potash, salt, related potash and salt byproducts, and process tailings. These operations resulted, or may have resulted, in soil, surface water, and groundwater contamination. At some locations, salt-processing waste, building materials (including asbestos-containing material), and ordinary trash may have been disposed of or buried in areas that have since been closed and covered with soil and other materials.
We could incur significant liabilities under environmental remediation laws such as CERCLA with regard to our current or former facilities, adjacent or nearby third-party facilities, or off-site disposal locations. Under CERCLA and similar state laws, in some circumstances liability may be imposed without regard to fault or legality of conduct and one party may be required to bear more than its proportional share of cleanup costs at a site. Liability under these laws involves inherent uncertainties.
We are also subject to federal and state environmental laws that regulate discharges of pollutants and contaminants into the environment, such as the U.S. Clean Water Act and the CAA. For example, our water disposal processes rely on dikes and reclamation ponds that could breach or leak, resulting in a possible prohibited release into the environment. Moreover, although the North and East mines in New Mexico and the Moab mine in Utah are designated as zero discharge facilities under the applicable water quality laws and regulations, these mines could experience some water discharges during significant rainfall events.
We expect that we will be required to continue to invest in environmental controls at our facilities and that these expenses could be significant. In addition, violations of environmental, safety, and health laws could subject us to civil and, in some cases, criminal sanctions. We could also be required to invest in additional equipment, facilities, or employees, or could incur significant liabilities, due to any of the following:
•changes in the interpretation of environmental laws
•modifications to current environmental laws
•the issuance of more stringent environmental laws
•malfunctioning process or pollution control equipment
The mining and processing of potash and langbeinite also generate residual materials that must be managed both during the operation of the facility and upon facility closure. For example, potash tailings, consisting primarily of salt, iron, and clay, are stored in surface disposal sites and require management. At least one of our New Mexico facilities, the HB mine, may have issues regarding lead in the tailings pile as a result of operations conducted by previous owners. During the life of the tailings management areas, we have incurred and will continue to incur significant costs to manage potash residual materials in accordance with environmental laws and regulations and permit requirements.
As a potash producer, we currently are exempt from certain State of New Mexico mining laws related to reclamation obligations. If this exemption were to be eliminated or restricted, we could be required to incur significant expenses related to reclamation at our New Mexico facilities.
For more information about environmental, safety and health matters affecting our business, see "Business-Environmental, Safety, and Health Matters."
Risks Related to our Common Stock
The price of our common stock may be volatile and you could lose all or part of your investment.
The market price of our common stock has historically experienced, and may continue to experience, volatility. For example, during 2021, the market price of our common stock ranged between $21.92 and $52.91. These fluctuations may continue because of numerous factors, including, but not limited to, the following:
▪our operating performance and the performance of our competitors
▪the public's reaction to our press releases, other public announcements, or filings with the SEC
▪changes in earnings estimates or recommendations by research analysts who follow us or other companies in our industry
▪variations in general economic, market, and political conditions
▪changes in commodity prices or foreign currency exchange rates
▪substantial sales of common stock by us in connection with future acquisitions or capital raising activities
▪actions of our current stockholders, including sales of common stock by our directors and executive officers
▪the arrival or departure of key personnel
▪other developments affecting us, our industry, or our competitors
▪the other risks described in this Annual Report on Form 10-K
Our financial position, cash flows, results of operations, and stock price could be materially adversely affected if commodity prices decline. In addition, in recent years the stock market has experienced extreme price and volume fluctuations. This volatility has had a significant effect on the market prices of securities issued by many companies for reasons unrelated to their operating performance. Our stock price may experience extreme volatility due to uncertainty regarding, among other things, commodity prices. These market fluctuations, regardless of the cause, may materially and adversely affect our stock price, regardless of our operating results.
Our stock is currently listed on the NYSE. For continued listing, we are required to meet specified listing standards, including a minimum stock price, market capitalization, and stockholders’ equity. If we are unable to meet the NYSE’s listing standards the NYSE would delist our common stock. At that point, it is possible that our common stock could be quoted on the over-the-counter bulletin board or the pink sheets. This could have negative consequences, including reduced liquidity for stockholders; reduced trading levels for our common stock; limited availability of market quotations or analyst coverage of our common stock; stricter trading rules for brokers trading our common stock; and reduced access to financing alternatives for us. We also would be subject to greater state securities regulation if our common stock was no longer listed on a national securities exchange. Volatility of our common stock may make it difficult for you to resell shares of our common stock when you want or at attractive prices.
The market price of our common stock may be adversely affected by the future issuance and sale of additional shares of our common stock, or by our announcement that the issuances and sales may occur.
We cannot predict the size of future issuances or sales of shares of our common stock in connection with future acquisitions or capital raising activities, or the effect, if any, that the issuances or sales may have on the market price of our common stock. The issuance and sale of substantial amounts of shares of our common stock or announcement that the issuances and sales may occur, could adversely affect the market price of our common stock.
We do not anticipate paying cash dividends on our common stock.
We currently intend to retain earnings to reinvest for future operations and growth of our business and do not anticipate paying any cash dividends on our common stock. Accordingly, realization of any gain on our common stock will depend on the appreciation of the price of the shares of our common stock, which may never occur. However, our board of directors, in its discretion, may decide to declare a dividend at an appropriate time in the future, subject to the terms of our revolving credit agreement. A decision to pay a dividend would depend upon, among other factors, our results of operations, financial condition, and cash requirements and the terms of our revolving credit agreement at the time a payment is considered.
Provisions in our charter documents and Delaware law may delay or prevent a third party from acquiring us.
We are a Delaware corporation and the anti-takeover provisions of Delaware law impose various barriers to the ability of a third party to acquire control of us, even if a change of control would be beneficial to our existing stockholders. In addition, our current certificate of incorporation and bylaws contain several provisions that may make it more difficult for a third party to acquire control of us without the approval of our board of directors. These provisions may make it more difficult or expensive for a third party to acquire a majority of our outstanding common stock. Among other things, these provisions:
•allow our board of directors to create and issue preferred stock with rights senior to those of our common stock without prior stockholder approval, except as may be required by NYSE rules
•do not permit cumulative voting in the election of directors, which would otherwise allow less than a majority of stockholders to elect director candidates
•prohibit stockholders from calling special meetings of stockholders
•prohibit stockholders from acting by written consent, thereby requiring all stockholder actions to be taken at a meeting of our stockholders
•require vacancies and newly created directorships on the board of directors to be filled only by affirmative vote of a majority of the directors then serving on the board
•establish advance notice requirements for submitting nominations for election to the board of directors and for proposing matters that can be acted upon by stockholders at a meeting
•classify our board of directors so that only some of our directors are elected each year
These provisions also may delay, prevent, or deter a merger, acquisition, tender offer, proxy contest, or other transaction that might otherwise result in our stockholders receiving a premium over the market price of the common stock they own.
We may issue additional securities, including securities that are senior in right of dividends, liquidation, and voting to our common stock, without your approval, which would dilute your existing ownership interests.
Our board of directors may issue shares of preferred stock or additional shares of common stock without the approval of our stockholders, except as may be required by NYSE rules. Our board of directors may approve the issuance of preferred stock with terms that are senior to our common stock in right of dividends, liquidation, or voting. Our issuance of additional common shares or other equity securities of equal or senior rank will have the following effects:
•our pre-existing stockholders’ proportionate ownership interest in us will decrease
•the relative voting strength of each previously outstanding common share may diminish
•the market price of the common stock may decline
If securities or industry analysts do not publish research or reports about our business, if they adversely change their recommendations regarding our stock, or if our operating results do not meet their expectations, our stock price could decline.
The trading market for our common stock may be influenced by the research and reports that industry or securities analysts publish about us or our business. If one or more of these analysts cease coverage of Intrepid or fail to publish reports on us regularly, we could lose visibility in the financial markets, which in turn could cause our stock price or trading volume to decline. Moreover, if one or more of the analysts who cover Intrepid downgrade our stock or if our operating results do not meet their expectations, our stock price could decline.
ITEM 1B.UNRESOLVED STAFF COMMENTS
None.
ITEM 2.PROPERTIES
Overview of Properties
Our extraction and production operations are conducted entirely in the continental United States. We produce potash from three solution mining facilities: our HB solution mine in Carlsbad, New Mexico, our solution mine in Moab, Utah and our brine recovery mine in Wendover, Utah. We also operate our North compaction facility in Carlsbad, New Mexico, which compacts and granulates product from the HB mine. We produce Trio® from our conventional underground East mine in Carlsbad, New Mexico. We also have the West facility, which is a conventional underground potash mine that is not in operation and is in care-and-maintenance mode.
We also operate Intrepid South located in Lea County in southeastern New Mexico, which is comprised of 21,834 surface acres, 27,868 acres of BLM grazing leases and 10,097 acres of pending State of New Mexico grazing leases. In March 2020, we sold approximately 320 surface acres from our Intrepid South property, reducing our surface acre ownership from 22,154 acres acquired at the time of purchase, to the 21,834 acres we operate today.
We conduct most of our mining operations on properties that we lease from states or the federal government. These leases generally contain stipulations that require us to commence mining operations within a specified term and continue mining to retain the lease.
The stipulations on our leases are subject to periodic readjustment by the applicable state government and the federal government. The lease stipulations could change in the future, which could impact the economics of our operations. Our federal leases are for indefinite terms subject to readjustment of the lease stipulations, including the royalty payable to the federal government, every 20 years. Our leases with the State of New Mexico are issued for terms of 10 years and for as long thereafter as potash is produced in commercial quantities and are subject to readjustment of the lease stipulations, including the royalty payable to the state. Our leases with the State of Utah are for terms of 10 years subject to extension and possible readjustment of the lease by the State of Utah. Our leases for our Moab mine are operated as a unit under a unit agreement with the State of Utah, which extends the terms of all of the leases as long as operations are conducted on any portion of the leases. The term of the state leases for our Moab mine is currently extended until 2024 or so long as potash is being produced. As of December 31, 2021, approximately 20% of our state, federal, and private lease acres at our New Mexico facilities will be up for renewal within the next five years, and 43% of our state and federal lease acres at our Utah operations will be up for renewal within the next five years.
The following tables provide a summary of our mineral resources and reserves. Additional information is provided in the Individual Property Disclosures below.
| | | | | | | | | | | | | | | | | | | | | | | | | | | | | | | | | | | | | | | | | | | | | | | | | | |
Summary of Mineral Resources in Millions of Tons of Sylvinite and Langbeinite effective December 31, 2021. Based on 406 $/potash product ton mine site and 425 $/langbeinite product ton mine site. |
| | Measured Mineral Resources | | Indicated Mineral Resources | | Measured + Indicated Mineral Resources | | Inferred Mineral Resources |
| | Amount (Mt) | | Grade (%K2O) | | Amount (Mt) | | Grade (%K2O) | | Amount (Mt) | | Grade (%K2O) | | Amount (Mt) | | Grade (%K2O) |
Sylvinite | | | | | | | | | | | | | | | | |
New Mexico | | | | | | | | | | | | | | | | |
IPNM | | 370.0 | | 15.0 | | 200.0 | | 14.0 | | 570.0 | | 15.0 | | — | | — |
Utah | | | | | | | | | | | | | | | | |
Moab | | 106.0 | | 27.0 | | 190.0 | | 25.0 | | 296.0 | | 25.0 | | 38.0 | | 23.0 |
Wendover | | — | | — | | 80.5 | | 0.5 | | 80.5 | | 0.5 | | 109.0 | | 0.5 |
Total | | 476.0 | | 18.0 | | 471.0 | | 16.0 | | 946.5 | | 17.0 | | 147.0 | | 6.0 |
| | | | | | | | | | | | | | | | |
Langbeinite | | | | | | | | | | | | | | | | |
New Mexico | | | | | | | | | | | | | | | | |
IPNM | | 50.0 | | 10.0 | | 60.0 | | 10.0 | | 110.0 | | 10.0 | | — | | — |
Total | | 50.0 | | 10.0 | | 60.0 | | 10.0 | | 110.0 | | 10.0 | | — | | — |
| | | | | | | | | | | | | | | | | | | | | | | | | | | | | | | | | | | | | | |
Summary of Mineral Reserves in Millions of Product Tons of Potash and Langbeinite effective December 31, 2021. Based on 325 $/potash product ton mine site and 340 $/langbeinite product ton mine site. |
| | Proven Mineral Reserves | | Probable Mineral Reserves | | Total Mineral Reserves |
| | Amount (Mt) | | In Situ Grade (%K2O) | | Amount (Mt) | | In Situ Grade (%K2O) | | Amount (Mt) | | In Situ Grade (%K2O) |
Sylvinite | | | | | | | | | | | | |
New Mexico1 | | | | | | | | | | | | |
IPNM | | 4.1 | | 22.7 | | 0.2 | | 20.8 | | 4.3 | | 22.6 |
Utah | | | | | | | | | | | | |
Moab1 | | 1.6 | | 27.2 | | 0.9 | | 28.7 | | 2.5 | | 27.7 |
Wendover2 | | — | | — | | 1.8 | | 0.5 | | 1.8 | | 0.5 |
Total | | 5.7 | | 24.0 | | 2.9 | | 10.6 | | 8.6 | | 19.5 |
| | | | | | | | | | | | |
Langbeinite | | | | | | | | | | | | |
New Mexico3 | | | | | | | | | | | | |
IPNM | | 4.9 | | 8.5 | | 1.2 | | 9.1 | | 6.1 | | 8.6 |
Total | | 4.9 | | 8.5 | | 1.2 | | 9.1 | | 6.1 | | 8.6 |
1 - In situ grade corresponds to the amount of K2O in the contact area of the caverns |
2 - In situ grade corresponds to the amount of K2O in the brines |
3 - In situ grade corresponds to the amount of K2O in the langbeinite ore |
As noted, we have relatively long-lived proven and probable reserves and consequently expect to conduct limited and focused additional exploration in the coming five years. We plan to drill core holes in areas near our Carlsbad, New Mexico, facility, in order to further define the ore body. Development of the underground mines is expected to be coincident with the
continued advancement of ore zones. Development of the solution mine and brine evaporation operations is expected to be enhanced by the drilling of additional wells and flooding of new solution mine caverns. Although not in our current plans, we also have opportunities to rehabilitate the shafts at the currently idled North mine and additional surface infrastructure to accelerate mining of conventional reserves.
Our leased office space in Denver, Colorado, is approximately 19,000 square feet and has a term expiring on April 29, 2022.
We believe that all of our present facilities are adequate for our current needs and that additional space is available for future expansion on acceptable terms.
Individual Property Disclosure - New Mexico
Overview
Our New Mexico operations ("IPNM") consists of our HB Solar Solution, East, West, and North Mines and are located in southeastern New Mexico in Eddy and Lea Counties in the Carlsbad Potash District ("CPD"). The location is further defined by the boundary of the Known Potash Leasing Area ("KPLA"). This United States Bureau of Land Management ("BLM") managed area consists of that part of the KPLA where the co-development guidelines for oil and gas and potash are in effect for federal lands under Order 3324 issued by the Secretary of the Interior on December 4, 2012 ("2012 Secretary's Order"). The 2012 Secretary's Order revises and supersedes a previous Order issued in 1986 and corrected in 1987. The 2012 Secretary’s Order does not alter the boundaries of the area. The area also contains state lands that are managed by the State of New Mexico under the New Mexico Oil Conservation Division Order R‐111‐P ("R-111-P"). In general, the stated objective of the 2012 Secretary’s Order and R‐111‐P is to prevent waste of petroleum and mineral resources and maximize the economic recovery of oil, gas, and potash minerals in the area.
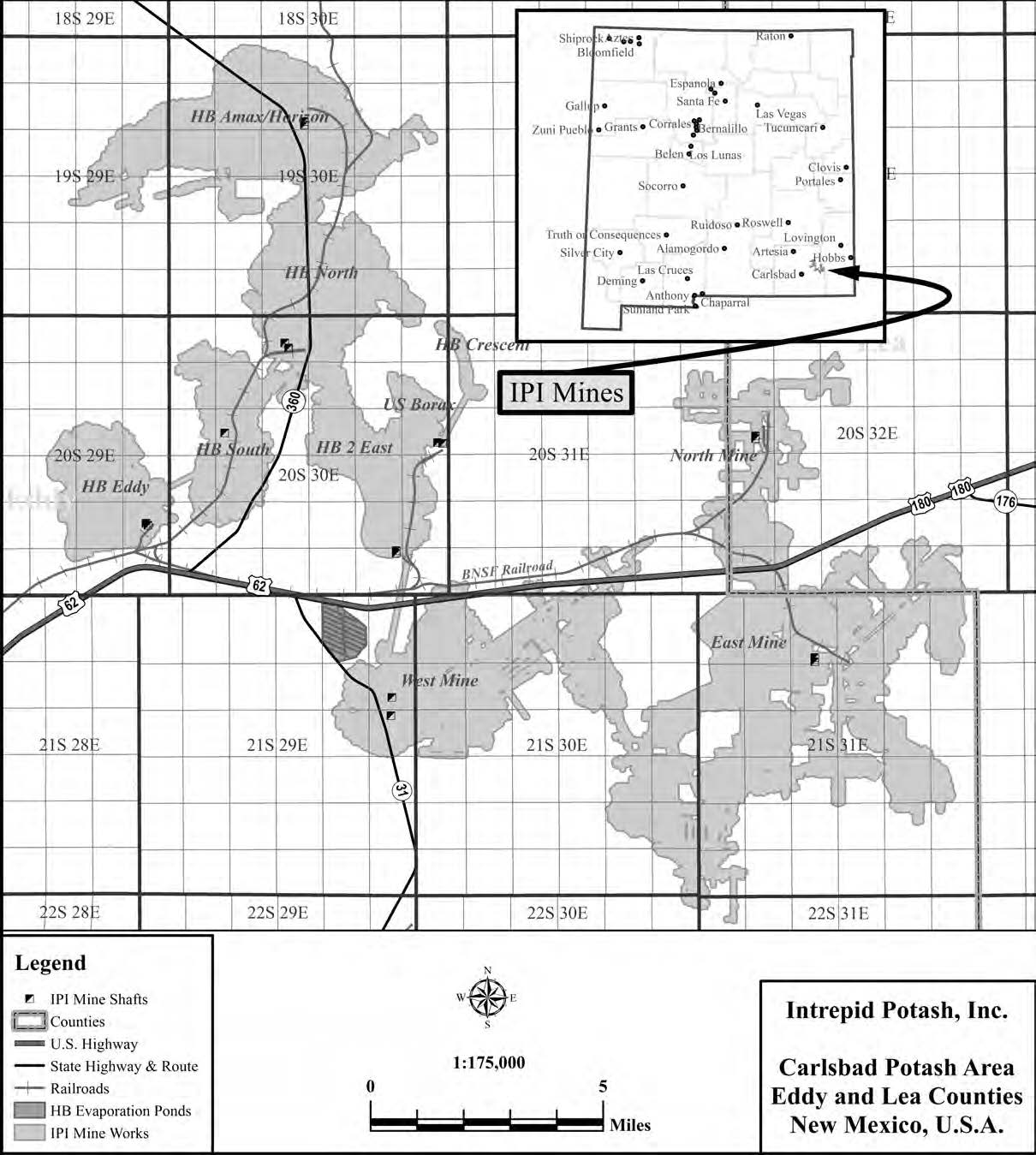
The geology of the potash‐bearing beds of the Carlsbad area has been well documented. Overall, the potash‐bearing beds may be described as bedded sedimentary rocks, deposited across the Delaware Basin and Northwest Shelf backreef from the Capitan Reef. The Carlsbad area falls within the Delaware Basin, part of the Permian Basin. The Delaware Basin has a maximum width of approximately 100 miles and a length of approximately 150 miles, extending from north of Carlsbad, New Mexico, to Pecos County, Texas.
The Permian Age sequence comprises the Ochoan, Guadalupe, Leonard, and Wolfcamp series in order of increasing age. Laterally extensive, evaporite beds containing deposits of halite, sylvite, langbeinite, kainite, carnallite, and other evaporite minerals are found within the Ochoan Series, whose top ranges from a depth of 2,000 feet near the Texas State line to approximately 200 feet below surface north of Carlsbad. Mining occurs in the Salado Formation which contains 12 potash ore zones, of which six have been or are currently being mined.
Sylvinite is currently being mined using solution methods in the 1st and 3rd ore zone. Historically, sylvinite has been conventionally underground mined in the 1st, 3rd, 5th, 7th, and 10th ore zones. Mechanical mining of langbeinite is currently occurring in the 3rd and 5th ore zones at the East Mine. Langbeinite is prevalent in the 3rd and 4th ore zones in the southern part of the Delaware Basin, and occurs mixed with sylvite in the 5th ore zone.
The property includes two operating mines, the East Underground and HB Solution Mines, one idled mine, the West Mine and the North Mine which was shut down in the early 1980’s. The property is located in Eddy and Lea Counties, near Carlsbad, New Mexico.
The two mining methods currently in practice at IPNM are high‐extraction mechanical underground room‐and‐pillar mining and solution mining. Mechanical mining is well suited to bedded deposits. All potash production at IPNM comes from the HB Solar Solution Mine in the 1st and 3rd ore zones. Trio® production is from langbeinite mined using room‐and‐pillar mechanical mining methods at the East Mine in the 3rd, 4th, and 5th ore zones. Historically, potash was sourced from the West Mine 5th, 7th, and 10th ore zones. Approximately 285 people are employed at the property.
There are no significant encumbrances on the property. A reclamation bond is currently in place for approximately $3.8 million and is expected to be adjusted to approximately $4.5 million with agency approval over time.
IPNM has all necessary operating permits and is in production, both underground and solution mining, and through permit reporting maintains environmental compliance. Environmental studies are conducted for major project expansions. The most recent Environmental Audit was completed in 2015 for the expansion of the HB In Situ Solution Mining project to include the solution mining of the abandoned Amax potash mine. The work referenced the initial Environment Impact Study ("EIS") for the HB In Situ Solar Solution Mining Project EIS.
East Mine and Plant
The East Mine is a high‐extraction, mechanical room‐and‐pillar mine. Potash was the primary product until mining progressed to the mixed langbeinite and potash ore in the 5th ore zone. The mixed ore was processed into two products: potash sourced from the sylvinite portion of the mixed ore, and Trio® sourced from the langbeinite portion of the mixed ore. The East Mine plant was converted to a langbeinite‐only operation in April 2016 and potash is no longer produced from the East Mine. The maximum productive capacity of the plant is 400,000 tons of Trio® concentrate annually.
There are five active sections with a miner and a shuttle car loading onto a belt conveyor. Each mining section produces approximately 240,000 tons of run‐of‐mine ore each year. The long‐range production balanced with sales projections results in a long‐term annual production of 1.2 million tons of ore for 250,000 tons of Trio® annually.
The East Plant was modified in 2003–2004 to allow dual processing to recover the K2O value from both the sylvite and langbeinite fractions of the ore. Langbeinite, marketed as Trio®, is recovered using dense media separation and a fine langbeinite recovery circuit. Currently about one million tons per year of ore is processed at a rate of 300 tons per hour. The ore is crushed, screened, pulped, and rescreened. Coarse material is forwarded to the dense media separation ("DMS") circuit. The DMS concentrate is water leached, debrined, and dried. The coarse product is separated into the three Trio® products. Fine material from the screening process is recovered using gravity separation, leaching, debrining, and drying. Fine material is upgraded to premium product using pelletization.
HB Mine and Plant
Historical room‐and-pillar mining operations at the HB complex recovered about 70% of the ore, leaving approximately 30% of the ore available for secondary recovery in pillars plus what can be recovered beyond the limits of the conventional mine works. Mining at the HB Solar Solution Mine recovers potash by injecting saturated saline NaCl brine into the old mine works to create underground leach lakes. Over time, the solution enriched with potash is pumped to the surface to solar evaporation ponds. Selective solar evaporation leaves behind a potash‐enriched salt that is collected using scrapers, pumped, and processed at the HB Plant. The solution mine comprises six injection wells, five extraction wells, and three monitoring wells.
In 2012, IPNM commenced filling the HB solar evaporation ponds. The extraction brine sourced from the mined‐out areas of the 1st ore zones of the former underground workings of portions of HB Eddy, HB South, HB North, and the HB Crescent, collectively referred to as the HB Mine, contains approximately 21.7% NaCl and 7.0% KCl. The brine is collected
and crystallized in 18 solar evaporation ponds. The HB flotation mill processes the harvested potash and salts from the solar evaporation ponds. Following the separation of KCl, the HB Solar Solution Mine also recovers significant quantities of NaCl.
The North Plant provides classification, compaction, quality control, and load‐out services for production from the HB Solar Solution Mine. Belly dump trucks unload HB product into a dump pocket. The material is then sent to surge bins. The product is screened, preheated, weighed, and sent to a compactor feed bin. Material is fed to the roll compactor, and resulting flakes are further reduced in size with the subsequent flake breaker and crusher. Product is then screened and sent to the curing dryer and screened once again before being sent to final product storage. The product is shipped to market in trucks or rail cars.
West Mine
The West Mine is a high‐extraction, mechanical room‐and‐pillar mine that was idled in July 2016 and placed in care‐and‐maintenance mode. The mine was last operated in the 5th, 7th, and 10th ore zones.
North Mine and Compaction Plant
The North Mine operated from 1957 to 1982 when it was idled, mainly due to low potash prices and a change in the mineralogy of the readily accessible remaining reserves which negatively impacted mineral processing. Although the mining and processing equipment has been removed, the mine shafts remain open. The compaction facility at the North Mine is where the HB potash product is granulated, stored, and shipped. The North Facility receives compactor feed from the HB Solar Solution Mine via truck and converts the compactor feed to finished granular‐sized product and standard‐sized product.
It is anticipated that a new sylvite processing facility will need to be constructed to handle the higher insoluble and higher carnallitic ores that are contained in the 8th and 10th ore zones. This new processing plant is expected to have a plant recovery of 75%, which is supported by the metallurgical test work done on the 10th ore zone ore by Tetra Tech in 2009 in support of Phase 1 of the North Mine Reopening Feasibility Study.
Leases and Permits
IPNM controls the right to mine approximately 143,000 acres in New Mexico. Of that acreage, 32,000 acres are leased from the State of New Mexico, 106,000 acres are leased from the United States government through the BLM, and 240 acres of mineral rights are leased from private owners. IPNM owns 4,700 surface acres near the mine site, adjacent to the federal and state mining leases. Most mining operations are on properties leased from the state or the federal government. These leases generally contain stipulations that require IPNM to commence mining operations within a specified term and continue mining to retain the lease. The stipulations on IPNM leases are subject to periodic readjustment by the applicable state government and the federal government. Federal leases are for indefinite terms subject to readjustment of the lease stipulations, including the royalty payable to the federal government, every 20 years. Leases with the State of New Mexico are issued for terms of 10 years and for as long thereafter as potash is produced in commercial quantities and are subject to readjustment of the lease stipulations, including the royalty payable to the state.
History of Operations
Potash was first discovered in southwest New Mexico in 1925 in Eddy County, New Mexico, in Snowden McSweeney Well No. I on a V. H. McNutt permit near the center of the portion of what is now the KPLA. Commercial shipments began in 1931. The mines have had numerous owners beginning with the U.S. Potash Company’s ownership of the West Mine from 1929 to 1956. Intrepid Mining, the predecessor to Intrepid Potash, acquired the mines, excluding the Amax Mine, from Mississippi Potash, Inc. in 2004. Intrepid acquired the lease to the Amax Mine in 2012. A full ownership history for each mine is included in section 5 of the technical summary report in Exhibit 96.1 to this annual report on Form 10-K.
Mineral Resource and Reserves Comparison to Prior Year
This is the first year of calculating reserves and resources for the New Mexico property using the new methodology. A comparison to prior periods will be included in next year's filing.
Mineral Resource and Reserves
Overview
We continue ongoing exploration as a part of operational long‐term planning. Core holes are drilled from the surface and underground, and channel samples are collected as mining advances. We provided Agapito Associates, Inc. ("Agapito") their dataset beginning in 2007. Since that time, multiple data points have been added and several drillholes were reassessed. Potash is also identified from gamma ray geophysical logs in oil and gas wells. Bed thickness and potash grade are estimated and quantified with input from 2,928 sample points. Extensive work was completed with geophysical tools in collaboration with the United States Geologic Survey ("USGS") to determine and verify potash grades from gamma logs. The dataset is from
oil and gas wells, surface core holes, underground core holes, channel samples, shaft samples, and roof bolt holes. The key sample types include 7,209 drillholes and channel samples and are broken down by mining zone.
The characterization of the hydrogeology was completed for the HB In Situ Solution Mine by AECCOM in 2011 and is included as part of the publicly available EIS. The study confirmed the availability of water for the initial flooding of the solution mines at a pumping rate ranging from 177 to 1,440 gallons per minute.
Mineral Resource
The exploration drillhole and channel sample data were compiled to form the database that serves as the basis for estimating the resources. The geologic setting was evaluated, and bed assignments reviewed. Of the data within the lease boundary, all data points contribute bed thickness, and several have assay information. The geology was modeled using Carlson Software (2020). A basic inverse distance squared algorithm was used with a search radius of ¾ mile to prepare the 100‐foot by 100‐foot grids for bed thickness and grade. The search radius was applied for Measured and Indicated Resources of ¼ mile and ¾ mile, respectively. Where data is dense, the nearest 25 data points were used to assign values for the grid block. The grids were multiplied by each other to compile a grade‐thickness ("GT") grid within the lease boundaries held by IPNM. The base grid was adjusted for each ore type cutoff. Key assumptions and parameters for resource estimation are listed in the tables below.
The classification of cutoff in terms of GT in units of feet-percent was defined in the Secretaries Order dated October 21, 1986 for mechanically mined potash deposits. The criteria are not dependent on thickness or grade, but on the product of the thickness and grade. To evaluate the viability of mining the IPNM mechanically mined resources, a break‐even cutoff GT was established. Inputs to the estimation of the break‐even cutoff analysis are cost of goods sold, product sale price, mill recovery, and nominal grade.
The cutoff for solution mining in flooded abandoned underground potash mines is a function of the grade of the brine being extracted which results in enough product tons to just cover the cost of production. The cutoff grade for resources of abandoned underground sylvinite is not a parameter for use in the estimation of solution mining resources but does establish an operational minimum limit for the brine grade reserves. The solution mining resources are the pillars remaining after mining and the fringe boundary of the mine. Resources could also be unmined ore left behind to provide geotechnical support. An operational limit of the flood elevation establishes the cutoff between resource and reserve for this deposit. When mining using solution methods in proximity to other mines, or other underground mines not within the control of IPNM, the critical factor in establishing a flood elevation is to keep adjoining properties dry or to protect structures such as shafts.
| | | | | | | | | | | | | | | | | | | | | | | | | | | | | | | | |
IPNM—Summary Mineral Resources in Millions of Tons of Sylvinite effective December 31, 2021 Based on 406 $/product ton mine site |
| | Resources | | Mechanical Mining Cutoff 2 (ft%K2O) | | Processing Recovery (%) |
| | Sylvinite 1 (Mt) | | Grade (%K2O) | | Contained K2O (Mt) | | |
| | | | | |
Measured mineral resources | | 370 | | 15 | | 56 | | 45-59 | | 75-85 |
Indicated mineral resources | | 200 | | 14 | | 29 | | 45-59 | | 75-85 |
Measured + Indicated resources | | 570 | | 15 | | 85 | | | | |
Inferred mineral resources | | — | | | | — | | | | |
| | | | | | | | | | |
IPNM—Summary of Mineral Resource in Millions of Tons of Langbeinite Mineralized Rock in Place effective December 31, 2021 Based on 425 $/product ton mine site |
| | Resources | | | | |
| | Langbeinite Mineralized Rock (Mt) | | | | | | Mechanical Mining Cutoff (ft%K2O) | | Processing Recovery (%) |
| | | Grade (%K2O) | | Contained K2O | | |
| | | | | |
Measured mineral resources | | 50 | | 10 | | 5 | | 32 | | 68 |
Indicated mineral resources | | 60 | | 10 | | 6 | | 32 | | 68 |
Measured + Indicated resources | | 110 | | | | 11 | | | | |
Inferred mineral resources | | — | | | | | | | | |
1 Sylvinite is a mixed evaporite containing NaCl and KCl. |
2 Solution mining resource cutoff is the old workings boundary. |
Mineral Resources were prepared by Agapito Associates, Inc., a qualified firm for the estimate and independent of Intrepid Potash. |
Mineral Resources are reported exclusive of Mineral Reserves, on a 100% basis. |
Mineral Resources are reported using Inverse Distance Squared estimation methods. |
Mt = million tons, % = percent, K2O = potassium oxide, ft = feet |
Additional information regarding the methodology and key assumptions used to calculate the mineral resource can be found in Section 11 of the technical report summary in Exhibit 96.1 to this Annual Report on Form 10-K.
Mineral Reserve
Mineral reserves that are to be mined using mechanical methods are estimated by the application of a detailed mine plan for the measured and indicated resources within the boundaries of the cutoff GT for reserves. The plan sets the basis for the estimation of annual production of product. The income from product sales and the operating and capital costs to mine the resource is fundamental to the cash flow used to establish economic viability.
Mineral reserves that are mined using solution mining methods are not subject to the traditional application of a cutoff grade but instead of operational limitations. An operational limit of the flood elevation establishes the cutoff between resource and reserve for this deposit.
By definition, modifying factors are the factors applied to indicated and measured mineral resources and then evaluated in order to establish the economic viability of mineral reserves. These factors for IPNM include mechanical and solution mining parameters; mineral processing; oil and gas drill islands and well locations; economic cutoff GT; deleterious minerology; and lease boundaries.
Mechanically Mined Reserves
Economic modeling indicates cutoff grades for reserves at the IPNM East Mine of 43 ft% K2O for langbeinite resource. Modeling also indicates a cutoff of 75 feet-percent K2O for the high‐insoluble sylvinite resources in the 8th and 10th
ore zones, which requires the capital investment of a new plant and refurbishment of shafts. A cutoff of 57 feet-percent K2O is indicated for the West Mine sylvinite resources which requires the processing plant, mine equipment, and associated infrastructure to be rehabilitated.
Solution Mined Reserves
Breakeven Cutoff for solution mined reserves is shown in the table below:
| | | | | | | | | | | | | | | | | | | | | | | | | | | | | | | | |
IPNM—Summary of Potash Mineral Reserves effective December 31, 2021 Based on 325 $/product ton mine site |
| | In-Place KCl (Mt) | | In Situ Grade1 (%K2O) | | Product (Mt) | | Brine Cutoff Grade2 (%K2O) | | Processing Recovery (%) |
| | | | | |
| | | | | |
Proven Mineral Reserves | | 5.5 | | 22.7 | | 4.1 | | 1.5 | | 85 |
Probable Mineral Reserves | | 0.3 | | 20.8 | | 0.2 | | 1.5 | | 85 |
Total Mineral Reserves4 | | 5.8 | | 22.6 | | 4.3 | | | | |
| | | | | | | | | | |
IPNM—Summary of Langbeinite Mineral Reserves effective December 31, 2021 Based on 340 $/product ton mine site |
| | ROM Ore (Mt) | | In Situ Grade3 (Diluted) (%K2O) | | Product (Mt) | | Cutoff Grade (ft%K2O) | | Processing Recovery (%) |
| | | | | |
| | | | | |
Proven Mineral Reserves | | 18.1 | | 8.5 | | 4.9 | | 43 | | 68 |
Probable Mineral Reserves | | 4.2 | | 9.1 | | 1.2 | | 43 | | 68 |
Total Mineral Reserves5 | | 22.3 | | 8.6 | | 6.1 | | | | |
1 In situ grade is the amount of K2O in the contact area of the caverns. |
2 Brine cutoff grade is the amount of K2O in the extracted brine necessary to cover the costs of production. |
3 In situ grade (diluted) is the amount of K2O in the ore body with consideration for dilution occurring during mining. |
4 Mineral Reserves are reported based on a flood elevation mining plan, dissolution factor of 96%, areal recovery of 100%, geologic factor of 94.2%, plant recovery of 85%, product purity of 95%, and cavern losses of 2%. |
5 Mineral Reserves are reported based on a detailed conventional mine plan, random impurities of 10%, plant recovery of 68%, and product purity of 94.4%. |
Mineral Reserves were prepared by Agapito Associates, Inc., a qualified firm for the estimate and independent of Intrepid Potash. |
Mineral Reserves are reported exclusive of Mineral Resources, on a 100% basis. |
Mt = million tons, % = percent, K2O = potassium oxide, ft = feet, ROM = Run-of-Mine |
Additional information regarding the methodology and key assumptions used to calculate the mineral reserve can be found in Section 12 of the technical report summary in Exhibit 96.1 to this Annual Report on Form 10-K.
Internal Controls
IPNM has an internal protocol that provides for well‐defined, safe practices. IPNM has standard operating procedures ("SOP's") in place for logging and sampling core from underground and surface core drilling. According to the SOP’s, the geologist uses gamma ray to initially select the sample interval prior to prepping the sample for analysis. The samples are assayed at the on‐site laboratory. The site laboratory has the capability to conduct X‐ray Diffraction ("XRD"), Total Organic Carbon, and flame photometry laboratory techniques. The mineral analysis for all core and channel samples is analyzed with the XRD. A sample of approximately 300–500 grams is collected. The sample is split down to around 100 g and run through a grinding mill to reduce the size down to approximately –100 mesh. A sample is weighed out to five grams and put into a micronizing mill that reduces the particle size to ~10 microns and pressed into a sample holder. The sample is inserted into the instrument and a diffraction pattern is retrieved. The diffraction pattern is then analyzed using the Rietveld refinement software,
reporting weight percent of solid mineral in the sample. The sample preparation, security, and laboratory analytical procedures are conventional industry practice and are adequate for the reporting of resources and reserves.
Individual Property Disclosure - Moab
Overview
The Moab property is a unique high‐altitude desert landscape formed from the sandstone of ancient seafloors and sand dunes. Elevations range from 3,900 feet (ft) to 4,400 ft above mean sea level. The property is located approximately 20 miles west of Moab, Utah, which is 234 miles southeast of Salt Lake City, Utah. The Colorado River runs north–south along the eastern operations boundary. Moab’s property covers an area of approximately 14,100 acres of land.
Moab’s potash leases include 10,100 acres from the State of Utah and approximately 200 acres from the US federal government through the U.S. Bureau of Land Management (BLM). Moab owns approximately 3,800 surface acres overlying and adjacent to portions of the mining leases with the State of Utah.
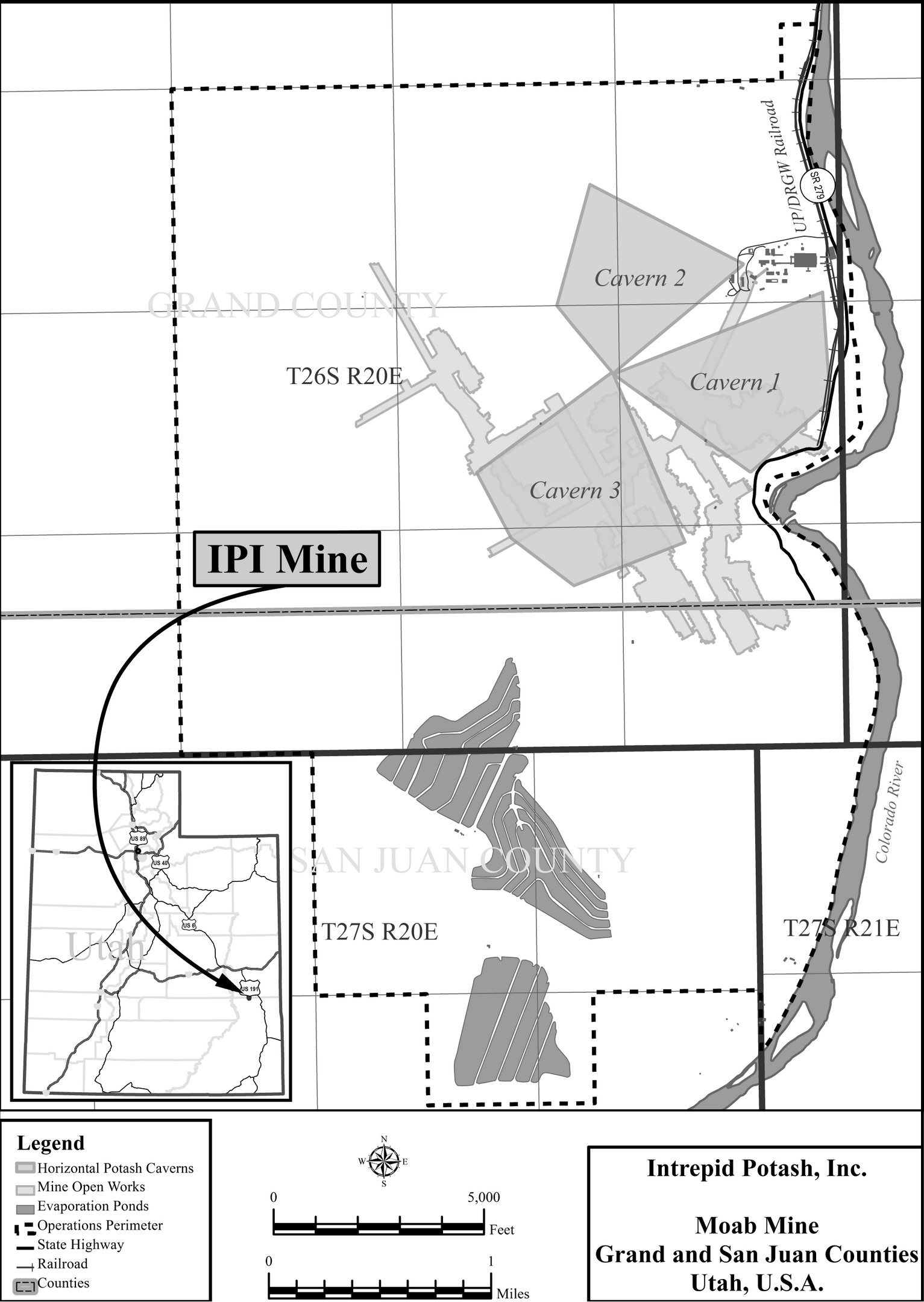
The depositional history of eastern Utah’s vast salt and potash resources begins during the regionally arid Pennsylvanian Period, 330–310 million years ago. An immense block of the Earth’s crust, in what is today western Colorado, was thrust upward to form the Uncompahgre Highlands and identified as the westernmost expression of the Ancestral Rocky Mountains. As is common throughout geologic history, dramatic uplift was coupled with subsidence in an adjoining area. The subsequent topographical basin was inundated by seawater as it subsided. Throughout the Pennsylvanian Period, sea levels rose and fell. With each retreat of the sea, the Paradox Basin, as it is called, became devoid of fresh sea water, allowing the process of evaporation to dominate which resulted in widespread precipitation of chloride minerals. This retreat/inflow cycle is known to have occurred a minimum of 29 times, with each marked by a specific and predictable sequence of sedimentary deposition. This series of depositional cycles is collectively known as the Paradox Formation. Potash is documented to exist in 17 of the 29 cycles, and it is from these formational cycles that commercial production of potash occurs. Of these 17, two are principally targeted by us for commercial potash production: Bed 5 and Bed 9.
Moab commercially produces potash from two zones, referred to as Bed 5 and Bed 9. These beds are part of a thick sequence of evaporite cycles predominantly composed of halite interspersed with sedimentary layers of black shale and anhydrite. Within Beds 5 and 9, the sylvinite is bounded above and below by occurrences of halite. Sylvite and halite are both water‐soluble by nature. By using water already saturated with sodium, it is possible to selectively dissolve a greater amount of the potassium chloride ore. The term ‘potash’ is used to describe a number of potassium‐bearing compounds. Of these, the mineral sylvite commands the greatest economic interest. Sylvite is commonly found mixed with halite, or sodium‐chloride (NaCl), to form the mineral sylvinite. Sylvinite is known to have a K2O content of up to 62% in its purest form.
Mining at Moab is by the solution mining technique referred to as “selective solution mining.” Selective solution mining dissolves only the KCl component of the sylvinite and leaves the sodium chloride component underground. KCl production is a function of brine grade and the well extraction rate and is limited by the solar ponds’ evaporation rate. Brine grade is a function of retention time within each bed.
Mining by solution methods ends with the delivery of the brine to the evaporation ponds. Mineral processing begins with pond sequencing to enhance crystallization of the potash. The crystals remaining in the ponds after solar evaporation are harvested and processed through the mill where the potash is separated from other salts, then concentrated by flotation. The concentrates are then dried, compacted, and screened into premium grades of white potash. The product is shipped to market in trucks or rail cars. Both potash and salt products are processed at the plant facility at a rate of 400 to 1,200 tons per day. The property exhibits the normal results of a surface salt-based operation and is in good working condition. A new compaction facility was installed in 2010.
Access to the property is predominantly via state highway 191 and state road 279, locally referred to as Potash Road. A Union Pacific/Denver and Rio Grande Western Railroad rail spur services the property. The nearest town to the Moab property is Moab, Utah (with an estimated population of about 5,250). Salt Lake City, Utah (population of 198,000) and Grand Junction, Colorado (population of 62,000), are located approximately 240 and 120 miles to the west and east, respectively, by road, and are the nearest major industrial and commercial airline terminals. Moab also has a commercial airline terminal with scheduled flights to Salt Lake City and other nearby cities depending on the season.
The nearby Colorado River provides the Moab mining operation with make‐up water under existing water rights with the State of Utah for a water supply of nine cubic feet per second. The Moab mine has been in operation as a solution mine since 1970 and, as a result, has the infrastructure and available personnel. The mining operation is accessible by a paved county road and accessible by rail. Electric power is fed from local utilities to a recently upgraded substation. The local area population is sufficient to support the Moab mine.
There are no significant encumbrances to the property, including current and future permitting requirements and associated timelines, permit conditions, and violations and fines. There are no significant factors and risks that may affect access, title, or the right or ability to perform work on the property. Moab holds numerous environmental and other permits and governmental approvals authorizing the operations at the facility.
Leases and Permits
Moab’s potash leases include 10,100 acres from the State of Utah and approximately 200 acres from the US federal government through the U.S. Bureau of Land Management (BLM). Moab owns approximately 3,800 surface acres overlying and adjacent to portions of the mining leases with the State of Utah.
History of Operations
Conventional underground mining began in 1964 by Texasgulf, Inc., but various mining problems caused management to convert to a system combining solution mining and solar evaporation in 1971. Prior to 1970, approximately 6.5 million tons of sylvinite ore was mined and from that, 1.7 million tons of potash produced. Mining was by continuous miners and made difficult by the irregular floor, gas, and high rock temperatures. The height mined was typically eight feet. The dip of the ore was such that maintaining the miners in the seam was difficult. The seam floor rolls and folds resulted in an irregular mine plan with many large areas left unmined as pillars. In some areas, secondary mining resulted in high extraction.
The Moab Salt operation was purchased by us in 1999. In 2000, we drilled two new recovery wells to revitalize production from Bed 5. Production from Bed 5 had declined from near 100,000 tons in 1994 to 60,000 tons in 1999. After completion of the two new recovery wells, the brine concentration improved, and production increased to near 100,000 tons in 2001. Maintaining production at or near the target rate of 100,000 tons per year was difficult from Bed 5 because of declining product concentration. It was believed that solution mining over the prior 32 years had solution mined most of the remnant pillars in the old workings and that active solution mining was restricted to the updip faces of the mine ribs.
Methods to enhance the production rate were evaluated by us and resulted in the decision to develop solution mining in Bed 9. Bed 9 is located 800 to 1,000 feet below Bed 5 and is of higher KCl content. Bed 9 had not been solution mined
previously, although, some test mining was completed by the prior owners in the late‐1960s. A novel method of solution mining was adopted for recovery of potash from Bed 9. Moab Salt‐27 and Moab Salt‐28 were drilled “horizontally” in 2002 in Bed 9 to connect and provide pathways for the liquor injected in Moab Salt‐27 to contact the sylvinite and differentially dissolve the sylvite before being lifted from Moab Salt‐28. Currently, Moab Salt‐29 connects Moab Salt‐27 and ‐28 and serves as an alternative to Moab Salt‐27 for injection.
Mineral Resource and Reserves Comparison to Prior Year
This is the first year of calculating reserves and resources for the Moab property using the new methodology. A comparison to prior periods will be included in next year's filing.
Mineral Resource and Reserves
Overview
The ore resource model created from the exploration and sampling database beginning in 2007 serves as the basis for this evaluation. Personal inspection of the properties has occurred over the years by Agapito personnel. The most recent inspection by Agapito took place on May 17, 2021. The inspection began with a tour of the tailings lake then the solar evaporating ponds. In addition, the injection and extraction wellfields, processing plant, product packaging and shipping areas were all inspected. During the site visit, harvesting was occurring, and the plant was operating. The plant is typically idle during the peak evaporation season from June 1 to September 1.
Mineral Resource
The property was evaluated using exploration drillhole and channel sample data to form the database that serves as the basis for estimating the resources. The geologic setting was evaluated, and zone assignments reviewed. All the core holes used in this resource estimation report both bed thickness and grade values that lie within the mine lease boundary. As an exception to this, the two potash exploration Wells 28 and IPI‐037, which report bed thicknesses with no assay data, are included in the resource estimate for thickness modeling.
The rationale for the measured, indicated, and Inferred limits is based on industry practice in the potash industry. Measured resources are within ¼ of a mile (1,320 feet) of a hole, conveying the highest level of confidence. In addition, the indicated resources are selected to be within ¾ of a mile (3,960 feet) of a hole and the inferred resources are selected to be within 1½ miles (7,920 feet) of a hole. Indicated tons exclude measured tons, inferred tons excludes the indicated and measured tons. This convention is considered reasonable for the geologic characteristics of the Cane Creek potash deposit.
The mineral resource for the Cane Creek Mine was estimated using Carlson Software 2020 ("Carlson 2020"), a commercially available geology and mine modeling software package. The resources within the property were segregated in the model into 100‐feet by 100‐feet blocks. The resource estimates included in this report are based on the 2018 modeling.
A deterministic estimate of the potash mineral resource was made using the inverse distance squared method. Invoking the theory that closer samples should be better predictors than those further away, the method assigns weights to samples inversely proportional to the separation distance between the estimation point and the sample point. The inverse distance squared method is useful for providing unbiased estimates of the overall resources.
The block grade and heights were generated within a 1.9‐mile search radius. The 1.9‐mile search radius was selected to capture more than one core hole in estimating block values in the areas of interest. The maximum number of drill holes for block estimation was limited to the 20 nearest drill holes. Inverse distance squared behaves as an exact interpolator. When calculating a block value, the weights assigned to the data points are fractions, and the sum of all the weights is equal to 1.0. An average unit density of 130 pounds per cubic foot was used to convert in‐place volume to tons. NaCl (salt) is not reported.
The proportion of the mineral deposit that is considered a resource depends on the following key factors: deposit thickness, deposit grade, and geologic factors. Areas where a bed thickness and potassium oxide (K2O) grade do not meet a 3‐foot and 18.95% K2O cutoff are excluded from the resource. The minimum thickness cutoff is used because sufficient recovery in thin beds by selective solution mining has not been demonstrated and because of difficulties in locating/maintaining horizontal holes within the bed. The grade cutoff is used because of the difficulty in selective mining in beds with less than 30% KCl content (18.95% K2O).
The gross in‐place sylvinite tonnage for each resource block was calculated by multiplying the net area of the block by the thickness of the bed and the density. The Measured, Indicated, and Inferred Mineral Resource tonnages were estimated within the prescribed radius from the sampling location.
The mineral resources for Bed 5 have been estimated using the end of year 2018 geologic model. Measured, Indicated, and Inferred resources were estimated by sampling blocks within a 1,320‐feet, 3,960‐feet, and 7,920‐feet radius of influence, respectively, from a sample location (drill hole).
The resource estimate for Bed 9 is based on cored intervals and assay data from 21 holes (19 with grade and thickness). A similar methodology used for the Bed 5 resource estimation was used in the resource estimate for Bed 9.
| | | | | | | | | | | | | | | | | | | | | | | | | | | | | | | | |
Moab—Summary of Mineral Resources in Millions of Tons of Sylvinite in Place effective December 31, 2021 Based on 406 $/product ton mine site |
| | Resources | | | | |
| | Sylvinite1 (Mt) | | Grade (%K2O) | | Contained K2O (Mt) | | Cutoff 2 | | Processing Recovery (%) |
| | | | | |
Measured mineral resources | | 106 | | 27 | | 28 | | Minimum of 3-ft and 18.95%K2O | | 83 |
Indicated mineral resources | | 190 | | 25 | | 47 | | Minimum of 3-ft and 18.95%K2O | | 83 |
Measured + Indicated mineral resources | | 296 | | 25 | | 75 | | | | |
Inferred mineral resources | | 38 | | 23 | | 9 | | Minimum of 3-ft and 18.95%K2O | | 83 |
1 Sylvinite is a mixed evaporite containing NaCl and KCl. |
2 Solution mining resource cutoff for flooded old workings is the mining extents boundary. |
Mineral Resources were prepared by Agapito Associates, Inc., a qualified firm for the estimate and independent of Intrepid Potash. |
Mineral Resources are reported exclusive of Mineral Reserves, on a 100% basis. |
Mineral Resources are reported using Inverse Distance Squared estimation methods. |
Mt = million tons, % = percent, K2O = potassium oxide, ft = feet |
Additional information regarding the methodology and key assumptions used to calculate the mineral resource can be found in Section 11 of the technical report summary in Exhibit 96.2 to this Annual Report on Form 10-K.
Mineral Reserve
Mineral reserves that are mined using solution mining methods are not subject to the traditional application of a cutoff grade but instead of operational limitations. By definition, modifying factors are the factors applied to a mine plan for the indicated and measured mineral resources and then evaluated in order to establish the economic viability of mineral reserves. The factors for Moab are solution mining parameters, mineral processing, and lease boundaries are shown below.
The reserve estimate is based on a mine plan developed for the Cane Creek Mine. The estimate is based on the geologic model and assigned thicknesses and grades for the flooded old mine workings updip boundary (Bed 5) mapped to the decline curve and the individual caverns (Bed 9).
The mine plan for Bed 5 was determined using a study developed to estimate the area of reserves that have been depleted through solution mining inside and around the perimeter of the old mine workings, with the exception of a large pillar within the perimeter. As such, this perimeter area has been excluded from the reserve estimates for Bed 5. Reserves were estimated for updip and horizontal areas outside of the perimeter. The mineral reserves were estimated as the difference between the reserves from the resource area and the net KCl tons extracted since 2001.
Although Bed 5 resources can be solution mined with additional horizontal caverns, the reserves estimate only focuses on the net reserves remaining in the old mine as the planned horizontal caverns in Bed 9 are more than enough to support the required mine life for this report.
The mine plan for Bed 9 includes the three existing operating caverns and three additional planned caverns. Estimate of the reserves within the current and future well system area use grade and thickness drillhole data and production to date. No estimate was made of the ore tons, average thickness, and average grade for the previously solution‐mined areas from Bed 9, only the equivalent tons of K2O and KCl were estimated. To date, about 830,000 tons of KCl have been mined from Bed 9. The modifying factors required to convert the in‐place tons into reserve tons are the same as those listed for Bed 5 with the exception of the dissolution factor. The Bed 9 dissolution factor was estimated using a concentration of 7.42% KCl by weight.
| | | | | | | | | | | | | | | | | | | | | | | | | | | | | | | | |
Moab—Summary of Potash Mineral Reserves effective December 31, 2021 Based on 325 $/product ton mine site |
| | In-Place KCl (Mt) | | In Situ Grade 1 (%K2O) | | Product (Mt) | | Brine Cutoff Grade 2 (%K2O) | | Processing Recovery (%) |
| | | | | |
| | | | | |
Proven Mineral Reserves | | 5.0 | | 27.2 | | 1.6 | | 1.9 | | 83.0 |
Probable Mineral Reserves | | 1.2 | | 28.7 | | 0.9 | | 1.9 | | 83.0 |
Total Mineral Reserves | | 6.2 | | 27.7 | | 2.5 | | | | |
1 In situ grade is the amount of K2O in the contact areas of the caverns. |
2 Brine cutoff grade is the amount of K2O n the extracted brine necessary to cover the costs of production. |
Mineral Reserves were prepared by Agapito Associates, Inc., a qualified firm for the estimate and independent of Intrepid Potash. |
Mineral Reserves are reported exclusive of Mineral Resources, on a 100% basis. |
Mineral Reserves are reported based on a solution mine plan, dissolution factor of 89%, areal recovery of 94%, geologic factor 94%, plant recovery of 83%, product purity of 95%. |
Mt = million tons, % = percent, K2O = potassium oxide, ft = feet |
Additional information regarding the methodology and key assumptions used to calculate the mineral reserve can be found in Section 12 of the technical report summary filed as Exhibit 96.2 to this Annual Report on Form 10-K.
Internal Controls
Moab has an internal protocol that provides for well‐defined, safe practices and uniform guidelines for gamma‐ray logging, core handling, and sample collection. The cores are collected and analyzed for ore zone identification. Cores are compared to the gamma‐ray log to determine sampling intervals. Duplicate samples are collected with one sample sent to the on‐site lab and the other stored with the corresponding core box from which the sample was sourced.
Individual Property Disclosure - Wendover
Overview
The Wendover operation is located near the Nevada-Utah border along the western edge of Utah’s Great Salt Lake Desert and is situated within the Bonneville Salt Flats ("BSF"). The BSF is an enclosed-subbasin that contains 150 square miles of salt crust. Because the basin is closed topographically and has no outlet, loss of water is ultimately through evaporation. The BSF was formed through the prolonged accumulation of evaporite minerals in conjunction with periodic lacustrine events. There are three aquifers known to exist beneath the BSF, in descending order, the shallow-brine aquifer, the alluvial-fan aquifer, and the deep-brine aquifer. Intrepid produces potash from the shallow-brine aquifer and the deep-brine aquifer. The climate in western Utah is arid with low precipitation and low relative humidity. Average rainfall is five inches and average evaporation is eighty inches.
Potash at Wendover is produced through solar evaporation of naturally occurring brines collected from the sedimentary basin adjacent to the processing facility via brine collection ditches and extraction wells. The potash content of the collected brine is concentrated by solar evaporation in a series of ponds to the point that solids are precipitated and can be collected. The precipitated solids are primarily sylvinite, a combination of NaCl and KCl. Harvested solid salts are hauled to the processing facility, where grinding and flotation processes are used to concentrate KCl. The concentrate is then leached with freshwater to remove most of the remaining NaCl. KCl is then dried, sized, and stored for shipment. Potash, NaCl, MgCL2, and metal recovery salt are shipped by truck and rail via Interstate 80 and the Union Pacific Railroad.
The Wendover potash operation is located in the westernmost part of Tooele County, Utah. The plant facilities and offices are located approximately three miles east of Wendover, Utah, on old US Highway 40. The site is approximately three miles east of the Nevada border and is primarily located south of Interstate 80, although portions of the site are located north of Interstate 80. The area of the Wendover mine operation is shown below. The facility, collection ditches, and evaporation systems cover approximately 87,834 acres (approximately 137 square miles). The majority of the ditch collection system is located to the south and east of the processing facilities.
A robust set of infrastructure is in place for Wendover. Natural gas, electricity, and water have historically been readily available and are expected to continue into the future. Process materials are readily available in the greater Salt Lake Area. All infrastructure for the operation is located approximately three miles east of Wendover, Utah, on old US Highway 40. Interstate 80 bisects the property. The Union Pacific Railroad runs next to the operations. The majority of personnel live and work in Wendover, Utah or West Wendover, Nevada, approximately three to six miles from the operation. The Wendover Airport is located near the operations, although most commercial flights serve the Salt Lake City Airport, which is approximately 115 miles from the operation.
The property has been in continuous operation by Intrepid since 2004. The property exhibits the normal results of a surface salt-based operation and is in good working condition. A new compaction facility was installed in 2010, and a new product warehouse was built in 2012. Intrepid uses monitoring wells drilled in October 2005 to evaluate brine quality in the shallow-brine aquifer.
Leases and Permits
Intrepid owns 57,534 acres located in Township 1 North, Range 18 West; Township 1 South, Ranges 17, 18 and 19 West; Township 2 South, Ranges 18 and 19 West; and Township 3 South, Ranges 18 and 19 West.
Approximately 30,300 acres owned by the BLM and the State of Utah are leased to Wendover, excluding lands used for highway and utility purposes. The State of Utah owns several state land trust sections within the site boundaries. Wendover holds leases from the federal government that include 24,700 acres adjoining the Wendover property to the east. Wendover also leases 5,600 acres of property from the State of Utah under special use and mineral leases. The state leases are interspersed among the Wendover property and the federal leases.
The only significant encumbrance is a reclamation bond of $8.9 million to cover the cost of site reclamation. There are no other significant encumbrances to the property, including current and future permitting requirements and associated timelines, permit conditions, and violations and fines. There are no significant factors and risks that may affect access, title, or
the right or ability to perform work on the property. Wendover holds numerous environmental and other permits and governmental approvals authorizing the operations at the facility.
History of Operations
The Bonneville area was recognized in the early 1900s as a source for potash. The original operation was known as the Salduro Works, which operated until 1918 and then closed due to a decline in potash demand. The original Salduro Works was responsible for acquiring lands on which a system of collection ditches was constructed. In the mid‐1930s, Bonneville Limited acquired more land to the west of the original property and constructed primary harvest ponds and additional infrastructure to support the mining operations. Between 1961 and 1963, various potash leases were acquired from the federal and state governments. Kaiser Aluminum & Chemical Corporation acquired Bonneville Limited in 1963. The property, including the ponds, processing operation, and lease land, was acquired by Reilly Industries, Inc. from Kaiser Aluminum & Chemical Corporation in 1988. Intrepid acquired the property from Reilly Industries, Inc. in April 2004.
Mineral Resource and Reserves Comparison to Prior Year
This is the first year of calculating reserves and resources for the Wendover property using the new methodology. A comparison to prior periods will be included in next year's filing.
Mineral Resource and Reserves
Overview
The ore resource model used to determine resources and reserves was created from a database of brine sampling data beginning in 2007 and include brine sample from the active mining horizon. Agapito has previous completed reserve estimation and analyses under SEC Guide 7, including personal inspection of the property. The most recent inspection was on May 19, 2021 and included the potash plant, evaporation ponds, wellheads, and ditches.
No traditional drilling exploration has taken place in Wendover. KCl grade is monitored from 27 wells that were drilled in October 2005 and have been sampled at least yearly to evaluate brine quality in the shallow-brine aquifer. Samples are evaluated at the on-site lab with full analysis capabilities, including X-ray fluorescence. Additional information on exploration can be found in Section 7 of the technical summary report in Exhibit 96.3 to this annual report on Form 10-K.
Mineral Resource
Estimates for potash resources were based on KCl brine concentration, porosity, and aquifer thickness from historical reports and brine monitoring data. Cutoff grade assumptions are based on historic cost data sourced from operations. Product sales prices used in the cutoff grade analyses is based on historical sales and marketing results and forward-looking pricing provided by Intrepid marketing and compared to third party sources.
Resource estimates for shallow-brine aquifer were based on the difference between historic well data collected between 1965 and 1967 and current monitoring data with consideration of the cutoff grade. There has been no change in trend of KCl grade to the primary pond or in potash production with brine grade held steady at approximately 0.97% for 58 years without declining.
Resource estimates for the deep-brine aquifer were based on current deep-well draw-down, pumping rates, and historical brine concentration variations. This resource is classified as an indicated resource due to the hydrological uncertainty of the aquifer and is expected to support production for at least 25 years.
| | | | | | | | | | | | | | | | | | | | | | | | | | | | | | | | |
Wendover—Summary of Mineral Resources in Millions of Tons of Sylvinite effective December 31, 2021 Based on 406 $/product ton mine site |
| | Resources | | | | Processing Recovery (%) |
| | Sylvinite Brine 1 (Mt) | | Grade (%K2O) | | Contained K2O (Mt) | | Brine Cutoff 2 (%K2O) | |
| | | | | |
Measured mineral resources | | — | | — | | | | | | |
Indicated mineral resources | | 80.5 | | 0.5 | | 5.0 | | 0.19 | | 85 |
Measured + Indicated mineral resources | | 80.5 | | 0.5 | | 5.0 | | 0.19 | | |
Inferred mineral resources | | 109.1 | | 0.5 | | 6.8 | | 0.19 | | 85 |
1 Sylvinite brine is NaCl and KCl in solution at average concentrations by weight. |
2 Solution mining resource cutoff is grade at which production covers operating costs. |
Mineral Resources were prepared by Agapito Associates, Inc., a qualified firm for the estimate and independent of Intrepid Potash. |
Mineral Resources are reported exclusive of Mineral Reserves, on a 100% basis. |
Mineral Resources are reported using Inverse Distance Squared (ID2) estimation methods. |
Mt = million tons, % = percent, K2O = potassium oxide, ft = feet |
Additional information regarding the methodology and key assumptions used to calculate the mineral resource can be found in Section 11 of the technical report summary in Exhibit 96.3 to this Annual Report on Form 10-K.
Mineral Reserve
Key assumptions for the mineral reserve estimates include KCl grade, thickness, geometry, and hydrogeological properties of the aquifer, presence of geologic anomalies that distort the aquifer, impurities that impact solubility or the surface concentration, separation, crystallization, or packaging process, and the cost of goods sold and estimated final price of the product. Due to its history of operations, infrastructure is mature and the processing and cost factors are well understood. Recovery estimates are based on past, current, and anticipated future performance and supported by laboratory or metallurgical testing of the plant feed.
| | | | | | | | | | | | | | | | | | | | | | | | | | | | | | | | |
Wendover—Summary of Potash Mineral Reserves effective December 31, 2021 Based on 325 $/product ton mine site |
| | Sylvinite Brine 1 (Mt) | | In Situ Grade 2 (%K2O) | | Product (Mt) | | Cutoff (%K2O) | | Processing Recovery (%) |
| | | | | |
| | | | | |
Proven Mineral Reserves | | | | | | | | | | |
Probable Mineral Reserves | | 88.5 | | 0.5 | | 1.8 | | 0.3 | | 85 |
Total Mineral Reserves | | 88.5 | | 0.5 | | 1.8 | | 0.3 | | |
1 Sylvinite brine is NaCl and KCl in solution at average concentrations by weight. |
2 Solution mining reserve cutoff is the grade at which production covers operating costs. |
Mineral Reserves were prepared by Agapito Associates, Inc., a qualified firm for the estimate and independent of Intrepid Potash. |
Mineral Reserves are reported exclusive of Mineral Resources, on a 100% basis. |
Mineral Reserves are reported based on an overall recovery factor of 60% and a product purity of 95%. |
Mt = million tons, % = percent, K2O = potassium oxide, ft = feet |
Additional information regarding the methodology and key assumptions used to calculate the mineral reserve can be found in Section 12 of the technical report summary in Exhibit 96.3 to this annual report to this annual report on Form 10-K.
Internal Controls
Intrepid-Wendover has internal quality assurance and quality control procedures for sample collection. Monitoring wells are sampled at least yearly to evaluate brine quality in the shallow-brine aquifer. During the evaporation season, daily brine samples are collected at brine advancement points. Brackish ponds and transfer pumps are sampled weekly. Sample are evaluated at an on-site lab with full analysis capabilities, including X-ray fluorescence.
Production
Our facilities have a current estimated annual productive capacity of approximately 390,000 tons of potash, and approximately 400,000 tons of langbeinite, based on current design. Our annual production rates are less than our estimated productive capacity. Actual production is affected by operating rates, the grade of ore mined, recoveries, mining rates, evaporation rates, product pricing, and the amount of development work that we perform. Therefore, as with other producers in our industry, our production results tend to be lower than reported productive capacity.
Our production capabilities and capital improvements at our facilities are described in more detail below, along with our historical production of our primary products and byproducts for the years ended December 31, 2021, 2020, and 2019.
Solution Mines
•Potash ore at HB is mined from idled original mine workings in the Carlsbad, New Mexico, area.
•The HB mine has a current estimated productive capacity of 180,000 tons annually. The productive capacity may vary between approximately 160,000 and 200,000 tons of potash, primarily due to evaporation rates. Potash produced from our HB mine is shipped by truck to the North facility for compaction.
•Potash ore at Moab is mined from two stacked ore zones: the original mine workings in Potash 5 and the horizontal caverns in Potash 9.
•The Moab mine has a current estimated productive capacity of approximately 110,000 tons of potash annually; evaporation rates have historically varied and, consequently, productive capacity may vary between approximately 75,000 and 120,000 tons of potash.
•Potash at Wendover is produced primarily from brine containing salt, potash, and magnesium chloride that is collected in ditches from the shallow aquifers of the West Desert. These materials are also collected from a deeper aquifer by means of deep-brine wells.
•The Wendover facility has a current estimated productive capacity of approximately 100,000 tons of potash annually; evaporation rates have historically varied resulting in actual annual production between approximately 65,000 and 100,000 tons of potash.
Conventional Underground Mines
•Sylvite and langbeinite ore at our Carlsbad locations occurs in a stacked ore body containing at least 10 different mineralized zones, seven of which contain proven and probable reserves.
•The East mine has a current estimated productive capacity of approximately 400,000 tons of Trio® annually, based on current design. The East mine was converted to a Trio®-only operation in April 2016 and potash is no longer produced from the East mine.
•The West mine was idled in July 2016 and placed in care-and-maintenance mode. When operational, it has an estimated productive capacity of approximately 400,000 tons of red potash annually.
Compaction Facility
•The North facility receives compactor feed from the HB mine via truck and converts the compactor feed to finished granular-sized product and standard-sized product.
Our Development Assets
We have development opportunities in our New Mexico facilities with the acceleration of production from our reserves and mineralized deposits of potash, and the potential construction of additional production facilities in the region. We also own the leases on two idled mines near Carlsbad: the AMAX/Horizon mine and the North mine.
AMAX/Horizon Mine
•We acquired the potash leases associated with the AMAX/Horizon mine in October 2012. The AMAX/Horizon mine was in continuous operation between 1952 and 1993. This mine, similar to the HB mine, is a viable candidate for solution mining in a manner that is consistent with the HB mine.
•State and federal permits were obtained in 2015 to utilize these leases for solution mining. The AMAX/Horizon solution mine is expected to utilize the same evaporation ponds and processing mill as the HB mine. We have not yet made a determination to proceed with this potential development project; however, future work may be performed to determine the ability to convert this idled underground mine to a solution mining opportunity.
North Mine
•The North mine operated from 1957 to 1982 when it was idled mainly due to low potash prices and mineralogy changes which negatively impacted mineral processing at the facilities. Although the mining and processing equipment has been removed, the mine shafts remain open. The compaction facility at the North mine is where we granulate, store, and ship potash produced from the HB mine. Two abandoned mine shafts, rail access, storage facilities, water rights, utilities and leases covering potash deposits, are already in place. As part of our long-term mine planning efforts, we may choose to evaluate our strategic development options with respect to the shafts at the North mine and their access to mineralized deposits of potash.
Our Production of Potash and Trio®
One product ton of potash contains approximately 0.60 tons of K2O when produced at our Moab and Wendover facilities and approximately 0.60 or 0.62 tons of K2O when produced at our HB facility. One product ton of langbeinite produced at our East facility contains approximately 0.22 tons of K2O. The following table summarizes production of our primary products at each of our facilities for each of the years ended December 31, 2021, 2020, and 2019:
| | | | | | | | | | | | | | | | | | | | | | | | | | | | | | | | | | | | | | | | | | | | | | | | | | | | | | | | |
(tons in thousands) | | Year Ended December 31, |
| | 2021 | | 2020 | | 2019 |
| | Ore Production | | Mill Feed Grade1 | | Finished Product | | Ore Production | | Mill Feed Grade1 | | Finished Product | | Ore Production | | Mill Feed Grade1 | | Finished Product |
Potash | | | | | | | | | | | | | | | | | | |
| | | | | | | | | | | | | | | | | | |
| | | | | | | | | | | | | | | | | | |
HB | | 746 | | 13.6% | | 117 | | 724 | | 15.2% | | 145 | | 734 | | 16.9% | | 158 |
Moab | | 648 | | 15.0% | | 118 | | 536 | | 15.3% | | 104 | | 509 | | 15.6% | | 94 |
Wendover | | 338 | | 13.3% | | 52 | | 352 | | 15.3% | | 59 | | 409 | | 15.1% | | 75 |
| | 1,732 | | | | 287 | | 1,612 | | | | 308 | | 1,652 | | | | 327 |
Langbeinite | | | | | | | | | | | | | | | | | | |
East 2 | | 1,057 | | 8.6% | | 228 | | 913 | | 8.9% | | 213 | | 944 | | 9.1% | | 228 |
Total Primary Products | | | | 515 | | | | | | 521 | | | | | | 555 |
1 Mill feed grade shown is as percent of K2O. Mill freed grade is a measurement of the amount of mineral contained in an ore as a percentage of the total weight of the ore. For potash it is often represented as a percent of potassium oxide (K2O) or percent potassium chloride (KCl).
Water and Byproduct Production
We have permitted, licensed, declared and partially adjudicated water rights in New Mexico under which we sell water primarily to support oil and gas development in the Permian Basin near our Carlsbad facilities. During the extraction of potash and Trio®, we recover marketable salt, magnesium chloride, metal recovery salts, water, and brine containing salt and potassium from our mining processes. Our salt is used in a variety of markets including animal feed, industrial applications, pool salt, and the treatment of roads and walkways for ice melting or to manage road conditions. Magnesium chloride is typically used as a road treatment agent for both deicing and dedusting. At our Moab and Wendover facilities, we also produce metal recovery salt, which is potash mixed with salt, in ratios requested by our customers. Metal recovery salt is a combination of potash and salt that chemically enhances the recovery of aluminum in recycling processing facilities. Our brines are used primarily by the oil and gas industry to support well development and completion activities.
ITEM 3.LEGAL PROCEEDINGS
ITEM 4.MINE SAFETY DISCLOSURES
We are committed to providing a safe and healthy work environment. The objectives of our safety programs are to eliminate workplace accidents and incidents, preserve employee health, and comply with all safety- and health-based regulations. We seek to achieve these objectives by training employees in safe work practices; establishing, following, and improving safety standards; involving employees in safety processes; openly communicating with employees about safety matters; and recording, reporting, and investigating accidents, incidents, and losses to avoid recurrence. As part of our ongoing safety programs, we collaborate with MSHA and the New Mexico Bureau of Mine Safety to identify and implement accident prevention techniques and practices.
Our East, West, and North facilities in New Mexico are subject to regulation by MSHA under the Federal Mine Safety and Health Act of 1977 and the New Mexico Bureau of Mine Safety. MSHA inspects these facilities on a regular basis and issues various citations and orders when it believes a violation has occurred under federal law. Exhibit 95.1 to this Annual Report on Form 10-K provides the information concerning mine safety violations and other regulatory matters required by SEC rules. Our Utah and HB facilities are subject to regulation by OSHA and, therefore, are not required to be included in the information provided in Exhibit 95.1.
PART II
ITEM 5.MARKET FOR REGISTRANT'S COMMON EQUITY, RELATED STOCKHOLDER MATTERS AND ISSUER PURCHASES OF EQUITY SECURITIES
Market Information
Our common stock is traded on the NYSE under the symbol "IPI". As of February 28, 2022, we had 60 record holders of our common stock based upon information provided by our transfer agent.
Performance Graph—Comparison of Cumulative Return
The graph below compares the cumulative total stockholder return on our common stock with the cumulative total stockholder return on the S&P 500 Index, the Dow Jones U.S. Basic Materials Index, and a peer group for the period beginning on December 31, 2016, through December 31, 2021, assuming an initial investment of $100 and the reinvestment of dividends. The peer group consisted of Potash Corporation of Saskatchewan Inc., The Mosaic Company, Compass Minerals International, Inc., and Agrium Inc. for the period beginning on December 31, 2016, through December 31, 2018, and The Mosaic Company, Compass Minerals International, Inc., and Nutrien Ltd. from January 1, 2018, through December 31, 2021. On January 1, 2018, Potash Corporation of Saskatchewan Inc. and Agrium Inc. merged to form Nutrien Ltd.
| | | | | | | | | | | | | | | | | | | | | | | |
| IPI | | Peer Group | | S&P 500 | | Dow Jones U.S. Basic Materials |
December 31, 2016 | $ | 100.00 | | | $ | 100.00 | | | $ | 100.00 | | | $ | 100.00 | |
December 31, 2017 | $ | 228.85 | | | $ | 113.32 | | | $ | 121.83 | | | $ | 125.09 | |
December 31, 2018 | $ | 125.00 | | | $ | 105.15 | | | $ | 116.49 | | | $ | 104.86 | |
December 31, 2019 | $ | 130.29 | | | $ | 104.12 | | | $ | 153.17 | | | $ | 125.58 | |
December 31, 2020 | $ | 116.11 | | | $ | 113.39 | | | $ | 181.35 | | | $ | 148.59 | |
December 31, 2021 | $ | 205.43 | | | $ | 180.24 | | | $ | 233.41 | | | $ | 189.87 | |
Dividends
We currently intend to retain earnings to reinvest for future operations and growth of our business and do not anticipate paying any cash dividends on our common stock. However, our board of directors, in its discretion, may decide to declare a dividend at an appropriate time in the future, subject to the terms of our revolving credit agreement. A decision to pay a dividend would depend upon, among other factors, our results of operations, financial condition, and cash requirements and the terms of our revolving credit agreement at the time a payment is considered.
Purchases of Equity Securities by the Issuer
| | | | | | | | | | | | | | | | | | | | | | | | | | |
Issuer Purchases of Equity Securities |
Period | | (a) Total Number of Shares Purchased1 | | (b) Average Price Paid Per Share | | (c) Total Number of Shares Purchased as Part of Publicly Announced Plans or Programs | | (d) Maximum Number (or Approximate Dollar Value) of Shares that May Yet Be Purchased Under the Plan or Programs |
October 1, 2021, through October 31, 2021 | | — | | $— | | – | | N/A |
November 1, 2021, through November 30, 2021 | | — | | — | | – | | N/A |
December 1, 2021, through December 31, 2021 | | 10,083 | | 40.66 | | – | | N/A |
Total | | 10,083 | | $40.66 | | — | | N/A |
1 Represents shares of common stock withheld by us as payment of withholding taxes due upon the vesting of restricted stock held by our employees.
ITEM 6.RESERVED
ITEM 7.MANAGEMENT'S DISCUSSION AND ANALYSIS OF FINANCIAL CONDITION
AND RESULTS OF OPERATIONS
This Management's Discussion and Analysis should be read in conjunction with the accompanying consolidated financial statements and related notes contained in "Item 8. Financial Statements and Supplemental Data" of this Annual Report on Form 10-K.
This Management's Discussion and Analysis contains forward‑looking statements that involve risks, uncertainties, and assumptions as described under the heading "Cautionary Note Regarding Forward‑Looking Statements," in Part I of this Annual Report on Form 10-K. Our actual results could differ materially from those anticipated by these forward‑looking statements as a result of many factors, including those discussed under "Item 1A. Risk Factors" and elsewhere in this Annual Report on Form 10-K.
A discussion of the changes in our results of operations between the years ended December 31, 2020 and December 31, 2019 has been omitted from this Annual Report on Form 10-K but may be found in Item 7. Management's Discussion and Analysis of Financial Condition and Results of Operations of our Annual Report on Form 10-K for the year ended December 31, 2020, filed with the SEC on March 2, 2021, which is available free of charge on the SEC's website at www.sec.gov and our corporate website (www.intrepidpotash.com).
Overview
We are a diversified mineral company that delivers potassium, magnesium, sulfur, salt, and water products essential for customer success in agriculture, animal feed and the oil and gas industry. We are the only U.S. producer of muriate of potash (sometimes referred to as potassium chloride or potash), which is applied as an essential nutrient for healthy crop development, utilized in several industrial applications, and used as an ingredient in animal feed. In addition, we produce a specialty fertilizer, Trio®, which delivers three key nutrients, potassium, magnesium, and sulfate, in a single particle. We also provide water, magnesium chloride, brine and various oilfield products and services.
Our extraction and production operations are conducted entirely in the continental United States. We produce potash from three solution mining facilities: our HB solution mine in Carlsbad, New Mexico, our solution mine in Moab, Utah and our brine recovery mine in Wendover, Utah. We also operate our North compaction facility in Carlsbad, New Mexico, which compacts and granulates product from the HB mine. We produce Trio® from our conventional underground East mine in Carlsbad, New Mexico. Until mid-2016, we also produced potash from our East and West mines in Carlsbad, New Mexico.
We have permitted, licensed, declared and partially adjudicated water rights in New Mexico under which we sell water primarily to support oil and gas development in the Permian Basin near our Carlsbad facilities. We continue to work to expand our sales of water. In May 2019, we acquired certain land, water rights, state grazing leases for cattle, and other related assets from Dinwiddie Cattle Company. We refer to these assets and operations as "Intrepid South." Due to the strategic location of Intrepid South, part of our long-term operating strategy is selling small parcels of land to other companies, where such sales provide a solution to a company's need.
We have three segments: potash, Trio®, and oilfield solutions. We account for the sale of byproducts as revenue in the potash or Trio® segment based on which segment generated the byproduct. For each of the years ended December 31, 2021, 2020, and 2019, a majority of our byproduct sales were accounted for in the potash segment.
Significant Business Trends and Activities
We continued to operate through-out the COVID-19 pandemic to produce potash and Trio® and serve oil and gas markets through our oilfield solutions business. The safety and protection of our workforce is our first and foremost priority. We continue to follow various procedures we implemented to help minimize the risks to our employees, including changes in our operating procedures to accommodate social distancing guidelines, additional cleaning and disinfection procedures and requiring those employees who can work from home to do so.
We continue to monitor the guidance from various authorities, including federal, state and local public health authorities and may take additional actions based on their recommendations. There may be developments outside our control that would require us to adjust our operating plans.
Economic activity and our financial results improved in 2021 as most cities and states reduced restrictions when compared to 2020. Given the dynamic nature of the COVID-19 pandemic, we cannot reasonably estimate the impacts of COVID-19, if any, on our financial condition, results of operations, liquidity or cash flows in the future. We expect that if governmental authorities increase restrictive orders, such actions may have a material effect on revenue growth, financial
condition, liquidity, and overall profitability in future reporting periods. Please see further discussion under "Item 1A. Risk Factors."
Our financial results have been, or are expected to be, impacted by several significant trends and activities, including impacts from the COVID-19 pandemic, as discussed below. We expect that the trends described below may continue to impact our results of operations, cash flows, and financial position.
•Potash pricing and demand. Potash remained a significant driver of our profitability, comprising 48% of our total sales in 2021. Our average net realized sales price for potash increased in 2021 to $353 per ton compared to $250 per ton for 2020 due to multiple price increases since the summer of 2020. The posted price for agricultural potash, announced in December 2021, was $725 per ton or $480 per ton above the 2020 summer fill program. After this announcement, we booked orders for first quarter 2022 delivery and continue to fill orders as the spring season begins. Another price increase of $25 per ton was announced in February 2022 for second quarter deliveries. Strong commodity prices continue to support application rates across our markets and we believe customers see good value in potash in today's market. Our price expectations could be affected by, among other things, weather, planting decisions, rail car availability, commodity price decreases as a result of the COVID-19 pandemic or other reasons, and the price and availability of other potassium products.
Our sales volumes into industrial markets improved in 2021 compared to the prior year as oilfield activity rebounded from 2020. The majority of our industrial potash sales are into oil and gas markets and correlate to drilling and completion activity, which slowed significantly during 2020 due to the containment actions taken to help reduce the spread of COVID-19. Oil price remains supportive of drilling and completion activity although additional or renewed restrictions enacted in response to the COVID-19 pandemic may impact our sales if such actions affect available labor, transportation logistics, or cause supply disruptions.
Global effective production capacity continues to exceed demand and larger producers have worked to balance the market through production curtailments. Sanctions on Belarusian potash imports were recently announced and are expected to take effect in April 2022. Belarusian potash has historically supplied approximately 7% of the annual potash consumption in the United States. We expect other suppliers will increase their volume of imports in response to the sanctions although timing of these changes and the overall effect of the sanctions on the potash market are uncertain. As a small producer, domestic pricing of our potash is influenced principally by the price established by our competitors. The interaction of global potash supply and demand, ocean, land, and barge freight rates, currency fluctuations, and crop commodity values and outlook, also influence pricing.
•Trio® pricing and demand. Our average net realized sales price for Trio® increased to $295 per ton in 2021, compared to $195 per ton in 2020 as we announced multiple Trio® price increases over the past 18 months. In December 2021, we announced a $30 to $40 per ton price increase depending on grade, bringing our posted price to $480 per ton for Trio® granular and $505 per ton for Trio® premium. Similar to potash, after the price announcement, we saw good subscription from our historic customers and committed a majority of our first quarter volumes. We announced a $35 per ton price increase in February 2022, effective immediately, and we are starting to book sales at the higher price levels. Our ability to realize the increased prices may be affected by, among other things, weather, planting decisions, rail car availability, commodity price decreases as a result of the COVID-19 pandemic, and the price and availability of other potassium products.
Overall average net realized sales price per ton for Trio® will continue to be impacted by the percentage of international sales, particularly to offshore markets. Competition from lower cost alternatives and freight costs continue to negatively impact our average net realized sales price per ton to offshore markets. Limited supply of containers and vessels in recent quarters has also increased the cost of international shipments compared to previous years, further pressuring our margins into international markets. We plan to continue a price-over-volume strategy internationally, by focusing on those international markets where we obtain the highest average net realized sales price per ton and thus the highest margin.
We experience seasonality in domestic Trio® demand, with more purchases coming in the first and second quarters in advance of the spring application season in the U.S. In turn, we generally have increased inventory levels in the third and fourth quarters in anticipation of expected demand for the following year. We continue to operate our facilities at reduced production levels that approximate expected demand and allow us to manage inventory levels. If we experience reduced demand for Trio® due to warehouse closures or other effects from the COVID-19 pandemic, we may need to further reduce production rates to manage inventory levels.
•Water sales. Water sales increased in 2021 to $22.0 million, compared to $20.4 million in 2020 as oilfield activity in the Delaware Basin improved throughout 2021, supported by increasing oil prices. Compared to previous years, fracs
are requiring more total water and higher daily refresh rates which required us to purchase more third party water than in previous years. Although water sales have improved compared to previous years, some operators have switched to using exclusively recycled water or a combination of fresh water and recycled water when completing wells. We believe this change is due to the growing focus on environmentally friendly operations and a response to the large amounts of produced water that is present in certain basins and formations, such as the Delaware Basin in southeast New Mexico. By recycling and reusing produced water, operators are able to reduce fresh water purchases and decrease the cost of transporting and disposing of produced water into disposal wells.
An update to legal proceedings concerning our water rights is contained in Note 14 to our audited consolidated financial statements included in "Item 8. Financial Statements and Supplementary Data" of this Annual Report on Form 10-K.
•Byproduct sales. Byproduct sales increased to $26.2 million in 2021 compared to $20.5 million in 2020, primarily due to a $3.0 million increase in magnesium chloride sales. Record wet weather in the summer of 2019 in Wendover limited our production of magnesium chloride, reducing sales in the first half of 2020. Our 2021 sales of magnesium chloride were near historic averages. Salt sales increased $1.6 million in 2021 compared to the prior year due mainly to growth in the pool salt market. Byproduct water sales increased $0.7 million compared to 2020 as we saw increased oilfield activity, particularly in the second half of 2021.
•Weather impact. Evaporation rates in 2021 were below average across our facilities which led to decreased potash production in the second half of 2021 and will lead to decreased potash production in the spring of 2022 when compared to the prior year. We received a significant amount of rainfall at our HB facility in Carlsbad, New Mexico late in the summer which limited the amount of solids available in our ponds. As a result of the reduced potash production, we recorded abnormal production costs of $3.6 million and $2.4 million in the third and fourth quarters of 2021 respectively.
•Diversification of products and services. We increased our revenue from byproducts and other oilfield products and services in 2021 when compared to the prior year. As oilfield activity increased in the Delaware Basin throughout 2021, we saw a corresponding increase in revenue from right-of-way agreements, surface damages and easements, caliche sales, brine sales, and a produced water royalty. These sales generated revenue of $7.2 million in 2021 compared to $4.2 million in 2020, and with the exception of our brine sales, incur either minimal or no operating expense. As operators increase the use of recycled water in their completion activity we acquired multiple mobile recycling units in the second half of 2021 with the intent of adding produced water recycling services in 2022.
We announced in the first quarter of 2022 a joint feasibility study alongside the New Mexico Water Consortium and the New Mexico Environment Department to evaluate the potential of using treated produced water from oil and gas operations as injectate for our HB solar solution mine. Recycling and treatment technology have improved considerably over the last few years and the potential to convert a waste stream into a sustainable source for producing potash is a unique opportunity for the basin and we look forward to the pilot project beginning as early as the third quarter of 2022.
In March 2020, we sold approximately 320 acres of fee land from our Intrepid South property for $4.8 million and recognized a gain on the sale of the land of $4.7 million. The terms of the sale were highly restrictive and only allow the buyer to drill AGI wells on the property to dispose of natural gas with high concentrations of hydrogen sulfide (H2S). No water rights were included in the land sale, we retained surface access, and we restricted the use of caliche located on the property to the acreage that was sold in order to prevent sales to third parties or decrease future sales to the buyer. Our long-term strategic operating plan for Intrepid South includes selling small parcels of land to customers, where such sales provide a solution to a customer's specific needs. We may have additional strategic sales of small parcels of land to customers in the future.
In May 2020, we acquired an 11% equity stake in the W.D. Von Gonten Laboratories ("WDVGL"), a global industry leader in drilling and completion chemistry and a strong supporter of the use of potassium chloride in oil and gas drilling and completion activities. With this investment we plan to revitalize our industrial sales and high-speed mixing service given the poor performance of clay-inhibition chemical substitutes in certain formations. Our investment in WDVGL is also part of our strategy to leverage our existing oil and gas midstream businesses in southeast New Mexico and expand into additional oil and gas midstream and upstream activities. This expansion may be through organic growth, other strategic investments, partnerships, or acquisitions of complementary businesses that expand our product and service offerings beyond our existing assets or products. Additionally, we may expand into oil and natural gas development and production or into new products or services in our current industry or other industries.
Consolidated Results
| | | | | | | | | | | | | | | | | | | | |
(in thousands) | | Year Ended December 31, |
| | 2021 | | 2020 | | 2019 |
Sales1 | | $ | 270,332 | | | $ | 196,954 | | | $ | 220,075 | |
| | | | | | |
Cost of Goods Sold | | $ | 161,421 | | | $ | 135,843 | | | $ | 126,110 | |
| | | | | | |
Gross Margin | | $ | 55,764 | | | $ | 10,530 | | | $ | 43,478 | |
| | | | | | |
Income (Loss) Before Income Taxes | | 40,965 | | | (27,149) | | | 13,684 | |
Income Tax Benefit (Expense) | | 208,869 | | | (5) | | | (53) | |
Net Income (Loss) | | $ | 249,834 | | | $ | (27,154) | | | $ | 13,631 | |
| | | | | | |
Average Net Realized Sales Price per Ton2 | | | | | | |
Potash | | $ | 353 | | | $ | 250 | | | $ | 284 | |
Trio® | | $ | 295 | | | $ | 195 | | | $ | 195 | |
1Sales include sales of byproducts which were $26.2 million, $20.5 million and $26.5 million for the years ended December 31, 2021, 2020, and 2019, respectively.
2Average net realized sales price per ton is a non-GAAP measure. More information about this non-GAAP measure is below under the heading "Non-GAAP Financial Measure."
Consolidated Results for the Years Ended December 31, 2021, and 2020
Sales
Our total sales increased $73.4 million, or 37% in 2021, compared to 2020, as potash sales increased $38.0 million, Trio® sales increased $25.8 million, magnesium chloride sales increased $3.0 million, salt sales increased $1.6 million, water sales increased $1.6 million, brine water sales increased $1.2 million and sales of our other products and services from our oilfield solutions segment increased $2.2 million.
Our combined potash and Trio® sales increased $63.8 million in 2021, compared to 2020. Our potash average net realized sales price per ton increased 41% and our Trio® average net realized sales price per ton increased 51% in 2021 compared to 2020. Rising crop prices have driven strong demand for potash and Trio® which, combined with tight supplies have driven the significant increases in both our potash and Trio® average net realized sales prices per ton during 2021.
Our total water sales, including byproduct water sales increased 8% in 2021 compared to 2020, as oil and gas activities near our facilities in New Mexico continued to rebound from the negative economic effects caused by the COVID-19 pandemic.
Our total byproduct sales, excluding byproduct water sales, increased $5.0 million during 2021 compared to 2020. Our magnesium chloride sales increased 62% as we had more product to sell during 2021, as compared to 2020, as above average evaporation at our Wendover facility during the summer of 2020 resulted in more product available to sell during 2021. Our byproduct brine water sales increased 34% as oil and gas activities increased as discussed above. Our byproduct salt sales increased 18% due mainly to an increase in sales to the pool salt market.
Cost of Goods Sold
Our cost of goods sold increased $25.6 million, or 19%, in 2021, as compared to 2020 due to a $6.0 million increase in labor and benefits expense, a $5.2 million increase in third party water purchases on our South ranch to meet daily frac requirements, and a $3.3 million increase in royalty expense as a result of higher fertilizer prices. Inflationary pressures and rising commodity prices led to a $3.0 million increase in energy expense across our facilities and a $2.2 million increase in maintenance and operating supplies. Reduced production at our HB facility also increased our per ton of cost of goods sold compared to the prior year.
Abnormal Production Costs
The Carlsbad, New Mexico area where our HB solar solution mining facility is located, received significant rainfall, well above the historical rainfall average during this period. Additionally, humidity was higher than normal and temperatures were cooler than average during this period which reduced our pond production and our ability to extract brine. Because of the wet, humid weather and cooler temperatures, we have fewer harvestable tons of potash from our HB solution ponds. Accordingly, we recorded abnormal production costs of $6.0 million, and we may incur additional abnormal production costs in future periods. We did not incur any abnormal production costs in 2020.
Gross Margin
Our gross margin percentage increased to 21% in 2021, compared to 5% in 2020. The increase was driven primarily by an increase in sales driven by an increase in our average net realized sales price per ton for both potash and Trio®, partially offset by the increase in abnormal production costs and our cost of goods sold, as discussed above.
Selling and Administrative Expense
In 2021, selling and administrative expenses decreased $1.5 million or 6% from 2020. This was due mainly to a $1.6 million decrease in legal and other professional services expenses in 2021, as compared to 2020. During 2020, we incurred increased legal and other professional services expenses relating to the settlement of outstanding litigation during 2020, and defending various protests to our water rights. The decrease in legal and other professional services expenses was partially offset by increased bonus expense for administrative labor.
Litigation Settlement
A settlement conference was held with Mosaic in late March 2020 related to ongoing litigation. Intrepid and Mosaic agreed to settle the matter and we paid Mosaic an aggregate of $10 million to dismiss all claims against us in this litigation, and the matter is now closed. Please see further information in Note 14 to our audited consolidated financial statements included in "Item 8. Financial Statements and Supplemental Data" of this Annual Report on Form 10-K.
Gain on Sale of an Asset
In May 2021, we sold 326 acres of land in Texas for $6.0 million and recognized a gain on the sale of the land of $2.8 million. We purchased this land in May 2019 for the development of a produced water disposal facility and had permitted two disposal wells on the property. Unlike the strategic land sale completed in March 2020 discussed below, we did not include any restrictions on the buyer of this land.
In March 2020, we sold approximately 320 acres of fee land from our Intrepid South property for $4.8 million and recognized a gain on the sale of the land of $4.7 million. The terms of the sale were highly restrictive and only allow the buyer to drill AGI wells on the property to dispose of natural gas with high concentrations of H2S. No water rights were included in the land sale, we retained surface access, and we restricted the use of caliche located on the property to the acreage that was sold in order to prevent sales to third parties or decrease future sales to the buyer. Our long-term strategic operating plan for Intrepid South includes selling small parcels of land to other companies, where such sales provide a solution to a company's needs. We may have additional strategic sales of small parcels of land in the future.
Other Operating Expense
In 2021, we recognized other operating expense of $0.2 million compared to $0.7 million in 2020. In 2021, care and maintenance expenses increased $0.6 million that were partially offset by other operating income recorded related to earning certain contractual bonuses on a project to modify the tailings pond at our West facility. We modified our West tailings pond to allow for the construction of an underground natural gas pipeline near our West facility. During 2020, we recorded $0.4 million in care and maintenance expense and $0.3 million in other expenses.
Interest Expense
Interest expense decreased $2.8 million in 2021 compared to 2020, as we repaid the outstanding balance of our Series B Senior Notes in June 2021, and we repaid the outstanding balance on our credit facility in early August 2021.
Gain on Extinguishment of Debt
In April 2020, we received a $10 million loan under the CARES Act Paycheck Protection Program (the "PPP"). In June 2021, we received notice that the SBA had remitted funds to our bank to fully repay our PPP loan and accrued interest. Accordingly, we recognized a gain of $10.1 million related to the forgiveness of the PPP loan and the associated accrued interest on the loan.
Income Tax Benefit
During 2021, our valuation allowance for deferred tax assets decreased as we released $215.9 million from the valuation allowance during the fourth quarter. We released the valuation allowance because our long-term projection of future taxable income indicates that we will be able to realize the value of most of our deferred tax assets in the future. The release of our valuation allowance allowed us to record a tax benefit of $208.9 million during 2021.
Net Income
Net income increased from a net loss of $27.2 million in 2020 to net income of $249.3 million in 2021. The increase was primarily due to releasing $215.9 million of our valuation allowance for deferred taxes, a $10.1 million gain related to the forgiveness of the PPP loan and the improvement in our gross margin, as discussed above. Excluding the release of our valuation allowance for deferred taxes, our net income would have been $33.9 million.
Potash Segment Results
| | | | | | | | | | | | | | | | | | | | |
| | Year Ended December 31, |
(in thousands) | | 2021 | | 2020 | | 2019 |
Sales1 | | $ | 151,751 | | | $ | 108,060 | | | $ | 124,648 | |
Less: Freight costs | | 17,483 | | | 17,026 | | | 18,715 | |
Warehousing and handling costs | | 5,169 | | | 4,857 | | | 4,745 | |
Cost of goods sold | | 87,281 | | | 73,496 | | | 73,401 | |
Lower of cost or NRV inventory adjustments | | — | | | 1,130 | | | — | |
Costs associated with abnormal production and other | | 5,973 | | | — | | | — | |
Gross Margin | | $ | 35,845 | | | $ | 11,551 | | | $ | 27,787 | |
Depreciation, Depletion, and Amortization Incurred2 | | $ | 26,828 | | | $ | 26,536 | | | $ | 25,796 | |
Potash Sales Volumes (tons in thousands) | | 331 | | | 317 | | | 319 | |
Potash Production Volumes (tons in thousands) | | 287 | | | 308 | | | 328 | |
Average Potash Net Realized Sales Price per Ton3 | | $ | 353 | | | $ | 250 | | | $ | 284 | |
1Potash segment sales include byproduct sales which were $21.3 million, $15.6 million and $21.2 million for the years ended December 31, 2021, 2020, and 2019, respectively.
2Depreciation, depletion, and amortization incurred excludes depreciation, depletion, and amortization amounts absorbed in or (relieved from) inventory.
3Average net realized sales price per ton is a non-GAAP measure. More information about this non-GAAP measure is below under the heading "Non-GAAP Financial Measure."
Potash Segment Results for the Years Ended December 31, 2021, and 2020
Our total potash segment sales in 2021 increased $43.7 million, or 40%, as compared to 2020, as potash sales recorded in the potash segment increased 41% and potash segment byproduct sales increased 37%.
Potash sales recorded in the potash segment increased $38.0 million, or 41%, in 2021 compared to 2020, as the average potash net realized sales price per ton increased 41%, and we sold 4% more tons of potash. Strong crop commodity prices and tight near-term inventory levels led to multiple potash price increases during 2021. We saw increased potash tons sold into the agricultural and industrial markets, while potash tons sold into the animal feed market were similar to prior year.
Potash segment byproduct sales increased $5.7 million, or 37%, in 2021 compared to 2020, due to a $3.0 million increase in byproduct magnesium chloride sales, a $1.5 million increase in byproduct salt sales, an $0.8 million increase in byproduct water sales and a $0.4 million increase in byproduct brine water sales. Our magnesium chloride sales increased as we had more product to sell in 2021, due to good evaporation during the summer of 2020. Our salt sales increased as we increased sales in the pool salt market in 2021. Byproduct water and byproduct brine water sales increased in 2021 as oilfield activities increased as many of the containment measures that were adopted during 2020 in response to the COVID-19 pandemic were relaxed in 2021.
Potash cost of goods sold increased $13.8 million, or 19%, in 2021, as compared to 2020, due to a $2.6 million increase in labor and benefits expense, a $1.6 million increase in energy expense, a $1.1 million increase in contract labor for various maintenance projects, and a $2.1 million increase in royalty expense as a result of higher fertilizer prices. Reduced production at our HB facility also increased our per ton of cost of goods sold compared to the prior year.
Potash segment freight expense increased $0.5 million, or 3%, in 2021, as compared to 2020, mainly driven by an increase in freight expense related to selling 4% more tons of potash. Our freight expense is also impacted by the rates charged by carriers, geographic distribution of our products and by the proportion of customers arranging for and paying their own freight costs.
We produced 7% fewer tons of potash during 2021 compared to 2020, mainly due to the wet weather and reduced evaporation rates at our HB solar solution facility. We recorded abnormal production expenses of $6.0 million in 2021, as we had fewer harvestable tons of potash in our HB solution ponds. We did not record any abnormal production costs during 2020. We expect our near-term potash production from our HB facility will be lower than average, and we may incur additional abnormal production costs in future periods.
Our potash segment gross margin increased $24.3 million in 2021, compared to 2020, due mainly to the $43.7 million increase in potash segment sales, as discussed above.
Potash Segment - Additional Information
The table below shows our potash sales mix for 2021, 2020, and 2019.
| | | | | | | | | | | | | | | | | | | | |
| | Year Ended December 31, |
| | 2021 | | 2020 | | 2019 |
Agricultural | | 78 | % | | 79 | % | | 74 | % |
Industrial | | 6 | % | | 3 | % | | 12 | % |
Feed | | 16 | % | | 18 | % | | 14 | % |
Trio® Segment Results
| | | | | | | | | | | | | | | | | | | | |
| | Year Ended December 31, |
(in thousands) | | 2021 | | 2020 | | 2019 |
Sales1 | | $ | 96,058 | | | $ | 70,287 | | | $ | 69,551 | |
Less: Freight costs | | 20,656 | | | 20,431 | | | 20,514 | |
Warehousing and handling costs | | 4,113 | | | 4,574 | | | 3,876 | |
Cost of goods sold | | 54,847 | | | 50,902 | | | 42,251 | |
Lower of cost or NRV inventory adjustments | | — | | | 2,885 | | | 1,810 | |
| | | | | | |
Gross Margin (Deficit) | | $ | 16,442 | | | $ | (8,505) | | | $ | 1,100 | |
Depreciation, Depletion, and Amortization incurred2 | | $ | 5,477 | | | $ | 6,068 | | | $ | 6,163 | |
Sales Volumes (tons in thousands) | | 239 | | | 230 | | | 225 | |
Production Volumes (tons in thousands) | | 228 | | | 213 | | | 228 | |
Average Net Realized Sales Price per Ton3 | | $ | 295 | | | $ | 195 | | | $ | 195 | |
1Trio® segment sales include byproduct sales which were $4.9 million, $4.9 million and $5.3 million for the years ended December 31, 2021, 2020, and 2019, respectively.
2Depreciation, depletion, and amortization incurred excludes depreciation, depletion, and amortization amounts absorbed in or (relieved from) inventory.
3Average net realized sales price per ton is a non-GAAP measure. More information about this non-GAAP measure is below under the heading "Non-GAAP Financial Measure."
Trio® Segment Results for the Years Ended December 31, 2021, and 2020
Our total Trio® segment sales increased $25.8 million, or 37%, in 2021, as compared to 2020, as Trio® sales increased 39%, while Trio® segment byproduct sales were flat.
Our 2021 Trio® sales increased $25.8 million, or 39%, in 2021, as compared to 2020, as our average net realized sales price per ton increased 52% and we sold 4% more Trio® tons. Our Trio® average net realized sales price per ton increased as rising crop prices and the continued economic rebound from the COVID-19 pandemic drove an increase in demand. Trio® tons sold domestically increased 13% in 2021, as compared to 2020. The 2021 increase in domestic tons of Trio® sold was partially offset by a decrease in international tons sold, as we continue to focus our Trio® sales on the domestic market, which has a higher average net realized sales price per ton due to lower freight costs incurred for domestic sales as compared to international sales
Trio® freight costs increased 1% in 2021, compared to 2020. While we sold 4% more tons in 2021, we sold more tons of Trio® domestically and fewer tons of Trio® internationally. We incur less freight expense on our domestic Trio® sales compared to international Trio® sales. Our freight expense is impacted by the geographic distribution of our Trio® sales and by the proportion of customers arranging for and paying their own freight costs.
Our Trio® cost of goods sold increased 8% in 2021, as compared to 2020, primarily due to a 4% increase in Trio® tons sold during 2021. We also incurred higher labor and benefits expense, royalty expense, and increased energy expense compared to the prior year, which increased our per ton costs of goods sold.
We recorded lower of cost or net realized value inventory adjustments of $2.9 million in 2020, as our weighted average price per ton was higher than our average net realized sales price per ton. As our average net realized sales price per ton increased 52% during 2021, we did not record any lower of cost or net realized value inventory adjustments during 2021.
Our Trio® segment generated a gross margin of $16.4 million in 2021, compared to a gross deficit of $8.5 million in 2020, due to the factors discussed above.
Trio® Segment - Additional Information
The table below shows the percentage of total Trio® sales that were sold internationally in the past three years. | | | | | | | | | | | | | | |
| | United States | | Export |
For the year ended December 31, 2021 | | 92 | % | | 8 | % |
For the year ended December 31, 2020 | | 85 | % | | 15 | % |
For the year ended December 31, 2019 | | 74 | % | | 26 | % |
Oilfield Solutions Segment Results | | | | | | | | | | | | | | | | | | | | |
| | Year Ended December 31, |
(in thousands) | | 2021 | | 2020 | | 2019 |
Sales | | $ | 22,770 | | | $ | 18,929 | | | $ | 27,894 | |
| | | | | | |
Less: Cost of goods sold | | 19,293 | | | 11,445 | | | 12,367 | |
Gross Margin | | $ | 3,477 | | | $ | 7,484 | | | $ | 14,591 | |
Depreciation, Depletion, and Amortization incurred | | $ | 2,996 | | | $ | 2,663 | | | $ | 1,566 | |
Oilfield Solutions Segment Results for the Years Ended December 31, 2021, and 2020
Our oilfield solutions segment sales increased 20% in 2021, compared to 2020. Water sales increased $0.9 million in 2021 to $15.6 million. Sales from right-of-way agreements, surface damages and easements increased $1.2 million, produced water disposal royalties increased $0.9 million and brine water sales increased $0.7 million. Other sales in our oilfield solutions segment, such as sales of caliche and other oilfield services increased $0.2 million.
Our oilfield solutions sales are highly correlated to oil and gas activities near our facilities in New Mexico. Overall sales increased due to increased oil and gas activities in 2021 as compared to 2020 as oil prices continued to improve from the lows made in April 2020 due to the negative economic effects from the COVID-19 pandemic.
Cost of goods sold increased 69% in 2021, compared to 2020, primarily due to a $3.9 million increase in third-party water purchases to meet the significant daily refresh rates for certain fracs on our South ranch. Additionally, rental, lease, contract labor and depreciation expenses increased in 2021 as compared to 2020.
Gross margin decreased $4.0 million, or 54%, in 2021 compared to 2020, due to the factors described above.
Specific Factors Affecting Our Results
Sales
Our gross sales are derived from the sales of potash, Trio®, water, salt, magnesium chloride, brine water and various other products and services offered to oil and gas producers. Total sales are determined by the quantities of product we sell and the sales prices we realize. For potash, Trio® and salt, we quote prices to customers both on a delivered basis and on the basis of pick-up at our plants and warehouses. Freight costs are incurred on most of our potash, Trio® and salt sales, but some customers arrange and pay for their own freight directly. When we arrange and pay for freight, our quotes and billings are based on expected freight costs to the points of delivery. When we calculate our potash and Trio® average net realized sales price per ton, we deduct any freight costs included in sales before dividing by the number of tons sold. We believe the deduction of freight costs provides a more representative measure of our performance in the market due to variations caused by ongoing changes in the proportion of customers paying for their own freight, the geographic distribution of our products, and freight rates. Freight rates have been increasing, and if we are unable to pass the increased freight costs on to the customer, our average net realized sales price per ton is negatively affected. We manage our sales and marketing operations centrally and we work to achieve the highest average net realized sales price per ton we can by evaluating the product needs of our customers and associated logistics and then determining which of our production facilities can best satisfy these needs.
The volume of product we sell is determined by demand for our products and by our production capabilities. We operate our potash and Trio® facilities at production levels that approximate expected demand and take into account current inventory levels and expect to continue to do so for the foreseeable future.
Our water sales and other products and services offered through our oilfield solutions segment are driven by demand from oil and gas exploration companies drilling in the Permian Basin. As such, demand for our water is generally stronger during a cyclical expansion of oil and gas drilling. Likewise, a cyclical contraction of oil and gas drilling may decrease demand for our water.
Cost of Goods Sold
Our cost of goods sold reflects the costs to produce our products. Many of our production costs are largely fixed and, consequently, our cost of sales per ton on a facility-by-facility basis tends to move inversely with the number of tons we produce, within the context of normal production levels. Our principal production costs include labor and employee benefits, maintenance materials, contract labor, and materials for operating or maintenance projects, natural gas, electricity, operating supplies, chemicals, depreciation and depletion, royalties, and leasing costs. Some elements of our cost structure associated with contract labor, consumable operating supplies, reagents, and royalties are variable, but such elements make up a smaller component of our cost base. Our costs often vary from period to period based on the fluctuation of inventory, sales, and production levels at our facilities.
Our production costs per ton are also impacted when our production levels change, due to factors such as changes in the grade of ore delivered to the plant, levels of mine development, plant operating performance, and downtime. We expect that our labor and contract labor costs in Carlsbad, New Mexico, will continue to be influenced most directly by the demand for labor in the local region where we compete for labor with another fertilizer company, companies in the oil and gas industry, and a nuclear waste processing and storage facility.
We pay royalties to federal, state, and private lessors under our mineral leases. These payments typically equal a percentage of sales (less freight) of minerals extracted and sold under the applicable lease. In some cases, federal royalties for potash are paid on a sliding scale that vary with the grade of ore extracted. Our average royalty rate was 4.7%, 5.0%, and 5.0% in 2021, 2020, and 2019, respectively.
We incur costs to transfer water from our water source to our customers' facilities. Our operating costs depend on the distance and amount of water we must transfer. For water sold from certain of our water sources, we pay the State of New Mexico $0.11 per barrel of water sold. Additionally, water rights in New Mexico are subject to a stated point of diversion, purpose and place of use, and many of our water rights were originally issued for uses relating to our mining operations, or in
the case of the water rights at Intrepid South, for agricultural uses. To sell water commercially under these rights, we must apply for a permit from the OSE to change point of diversion, purpose and/or place of use of the underlying water rights. Third parties often protest our applications and the decisions made by the OSE concerning the changes to our water rights permits. As we have worked to sell more water commercially, we have incurred significant legal expenses associated with defending our water rights as they proceed through adjudication and obtaining water permits and approvals.
Income Taxes
We are a subchapter C corporation and, therefore are subject to U.S. federal and state income taxes on our taxable income. We recognize deferred tax assets and liabilities for the tax effect of temporary differences between the financial statement and tax basis of recorded assets and liabilities at enacted tax rates in effect when the related taxes are expected to be settled or realized. We also reduce deferred tax assets by a valuation allowance if it is more likely than not that some portion or all of the deferred tax assets will not be realized. In determining how much of a valuation allowance to recognize we consider our projections of future taxable income. All available evidence, both positive and negative, that may affect the realizability of deferred tax assets is identified and considered in determining the appropriate amount of the valuation allowance. We have concluded valuation allowances of $2.0 million and $217.9 million were required as of December 31, 2021, and 2020, respectively.
The amount of valuation allowance decreased in 2021 as compared to 2020 primarily from a release of $215.9 million of valuation allowance. Our effective tax rate for the years ended December 31, 2021, 2020, and 2019 was (509.9)%, 0.0%, and 0.4%, respectively. Our effective income tax rates are impacted primarily by changes in the underlying tax rates in jurisdictions in which we are subject to income tax, the need for a valuation allowance or release, and permanent differences between book and tax income for the period, including the benefit associated with the estimated effect of the percentage depletion deduction.
The effective tax rate for the years ended December 31, 2021, 2020, and 2019, respectively, differs from the U.S. federal statutory rate due to the change in valuation allowance.
During the year ended December 31, 2021, we recognized $157.3 million of deferred federal tax benefit, $51.7 million of deferred state tax benefit, and $0.2 million of current state income tax expense. During the years ended December 31, 2020, and 2019, we recognized an immaterial amount of income tax expense.
The estimated statutory income tax rates that are applied to our current and deferred income tax calculations are impacted most significantly by the states in which we conduct business. Changing business conditions for normal business transactions and operations as well as changes to state tax rate and apportionment laws potentially alter our apportionment of income among the states for income tax purposes. These changes in apportionment laws result in changes in the calculation of our current and deferred income taxes, including the valuation of our deferred tax assets and liabilities. The effects of any such changes are recorded in the period of the adjustment. These adjustments can increase or decrease the net deferred tax asset on the balance sheet and impact the corresponding deferred tax benefit or deferred tax expense on the income statement.
A valuation allowance is recognized for deferred tax assets if it is more likely than not that a portion or all of the net deferred tax assets will not be realized. In making such a determination, all available positive and negative evidence is considered, including future reversals of existing taxable temporary differences, projected future taxable income, tax-planning strategies, and results of recent operations. As of December 31, 2021, we were in a cumulative three-year income position. The cumulative three-year income position is significant positive evidence when evaluating the realizability of our deferred tax assets. Additionally, industry trends and forecasts as well as internal forecasts of future business show sustained amounts of taxable income. Thus, we have concluded it is more likely than not that most of our $211.1 million of deferred tax assets will be realized.
Liquidity and Capital Resources
Our operations have primarily been funded from cash on hand, cash generated by operations, and proceeds from debt and equity offerings. During 2021, we generated $79.1 million in cash flows from operating activities and we ended the year with $36.5 million of cash on hand, compared with cash on hand of $19.5 million at December 31, 2020.
In June 2021, we repaid the remaining $15.0 million of principal outstanding on our Series B Senior Notes and satisfied all obligations under the related Note Purchase Agreement. In connection with this repayment, the Company paid in aggregate approximately $15.6 million, which consisted of (i) $15.0 million of remaining aggregate principal amount of Series B Senior Notes, (ii) approximately $0.1 million of accrued interest and (iii) a "make-whole" premium of $0.5 million. As a result of the repayment, the Note Purchase Agreement was terminated.
In April 2020, we received a $10 million loan under the CARES Act Paycheck Protection Program (the "PPP"). In June 2021, we received notice that the SBA had remitted funds to our bank to fully repay our PPP loan and accrued interest.
Accordingly, we recognized a gain of $10.1 million related to the forgiveness of the PPP loan and the associated accrued interest on the loan.
As of December 31, 2021, we had $74.0 million available to borrow under our credit facility, no outstanding borrowings, and $1.0 million outstanding in a letter of credit. With the remaining availability under our credit facility and expected cash generated from operations, we believe we have sufficient liquidity to meet our obligations for the next twelve months.
We continue to monitor our future sources and uses of cash and anticipate that we will adjust our capital allocation strategies when, and if, determined by our Board of Directors. We may, at any time we deem conditions favorable, attempt to improve our liquidity position by accessing debt or equity markets in accordance with our existing revolving credit agreement. We also may raise capital in the future through the issuance of additional equity or debt securities, subject to prevailing market conditions. However, there is no assurance that we will be able to successfully raise additional capital on acceptable terms or at all.
The following summarizes our cash flow activity for the years ended December 31, 2021, 2020, and 2019:
| | | | | | | | | | | | | | | | | | | | |
| | Year ended December 31, |
| | 2021 | | 2020 | | 2019 |
| | (In thousands) |
Cash flows provided by operating activities | | $ | 79,067 | | | $ | 31,145 | | | $ | 49,381 | |
Cash flows used in investing activities | | $ | (14,823) | | | $ | (15,157) | | | $ | (80,641) | |
Cash flows (used in) provided by financing activities | | $ | (47,282) | | | $ | (17,043) | | | $ | 18,795 | |
Our revolving credit agreement contains restrictions on our ability to declare and pay dividends. The terms of our credit facility prohibit us from declaring and paying a dividend unless availability under the credit facility after giving effect to the dividend and during a specified period before the dividend is more than $15 million.
Operating Activities
Total cash provided by operating activities for the year ended December 31, 2021, was $79.1 million, an increase of $47.9 million compared with the year ended December 31, 2020. The increase was mainly driven by an increased potash and Trio® net realized sales price.
Investing Activities
Total cash used in investing activities decreased $0.3 million in 2021, compared to 2020, primarily related to a $2.4 million decrease in cash paid for investments and a $1.3 million increase in cash proceeds from the sale of property, plant, equipment, and mineral properties. Other additions to property, plant, equipment, and mineral properties increased $3.3 million in 2021 compared to 2020. In May 2021, we sold 326 acres of land in Texas that was adjacent to our South ranch for $6.0 million. This land was originally purchased in May 2019 for the potential development of a produced water disposal facility. Proceeds from the sale of property, plant, equipment, and mineral properties totaled $4.8 million during 2020 due primarily to a strategic sale of land on our Intrepid South property.
In the second quarter of 2020, we invested $3.5 million for an 11% equity stake in W.D. Von Gonten Laboratories ("WDVGL"). WDVGL is an industry leader in drilling and completion chemistry and a strong supporter of the use of potassium chloride in oil and gas drilling and completion activity.
Financing Activities
Total cash flows used in financing activities increased $30.2 million in 2021, as compared to 2020. During the third quarter of 2021, we made payments under our credit facility of $29.8 million. In June 2021, we paid $15.6 million, including the make-whole payment, to retire our Series B Senior Notes. In April 2020, we paid $20.0 million to retire our Series A Senior Notes at maturity. In July 2020, we paid $16.9 million, including the make-whole payment, to retire our Series C Senior Notes. During 2020, we borrowed an additional $10.0 million under our credit facility and received $10.0 million under the CARES Act Paycheck Protection Program.
We routinely review the creditworthiness of our customers and make decisions to limit our exposure whenever possible. As economic activities improved in 2021, our delinquencies declined as compared to 2020. During 2020, we saw an increase in delinquencies from our smaller customers that purchase water and brine at our truck stations. These smaller customers mainly serve oil and gas exploration companies and the COVID-19 pandemic had dramatically decreased oil and gas drilling activity.
Senior Notes
In June 2021 we repaid the remaining $15.0 million of principal outstanding on our Series B Senior Notes and satisfied all obligations under the related Note Purchase Agreement. In connection with this repayment, the Company paid in aggregate approximately $15.6 million, which consisted of (i) $15.0 million of remaining aggregate principal amount of Series B Senior Notes, (ii) approximately $0.1 million of accrued interest and (iii) a "make-whole" premium of $0.5 million. As a result of the repayment, the Note Purchase Agreement was terminated.
Credit Facility
We maintain a secured revolving credit facility with Bank of Montreal. As of December 31, 2021, borrowings under the credit facility bore interest at LIBOR (London Interbank Offered Rate) plus an applicable margin of 1.25% to 2.00% per annum, based on our leverage ratio. We have granted to Bank of Montreal a first lien on substantially all of our assets. The obligations under the credit facility are unconditionally guaranteed by several of our subsidiaries.
We occasionally borrow and repay amounts under the facility for near-term working capital needs or other purposes and may do so in the future. For the year ended December 31, 2021, we made no borrowings and repaid $29.8 million under the facility. For the year ended December 31, 2020, we borrowed $10.0 million and made no repayments, under the facility. As of December 31, 2021, we had no borrowings outstanding and $1.0 million in an outstanding letter of credit under the facility. As of December 31, 2020, we had $29.8 million of borrowings outstanding and $1.0 million in an outstanding letter of credit under the facility. We had $74.0 million available under the facility as of December 31, 2021.
We were in compliance with the applicable covenants under the facility as of December 31, 2021.
PPP Loan
In April 2020, we received a $10 million loan under the CARES Act Paycheck Protection Program (the "PPP"). In June 2021, we received notice that the SBA had remitted funds to our bank to fully repay our PPP loan and accrued interest. Accordingly, we recognized a gain of $10.1 million related to the forgiveness of the PPP loan and the associated accrued interest on the loan.
Capital Investments
During 2021, we paid cash of $19.8 million to acquire property, plant, equipment, and mineral properties. Due to the economic uncertainty as a result of the COVID-19 pandemic, particularly in oil and gas markets near our operations, we limited our 2021 capital program to mostly sustaining capital projects.
We expect to make capital investments in 2022 of $40 million to $60 million. We anticipate spending approximately $25 million to $35 million on sustaining capital projects in 2022, with the remainder of our estimated spending on opportunity projects. We have significant discretion over our opportunity capital investments in 2022 and we may adjust our investment plans as our expectations for 2022 change. We anticipate our 2022 operating plans and capital programs will be funded out of operating cash flows and existing cash. We may also use our revolving credit facility, to the extent available, to fund capital investments.
Critical Accounting Policies and Estimates
Our discussion and analysis of our financial condition and results of operations are based upon our consolidated financial statements, which have been prepared in accordance with GAAP. The preparation of the consolidated financial statements in conformity with GAAP requires management to make estimates and assumptions that affect the amounts reported in our financial statements. Actual results could differ from our estimates and assumptions, and these differences could result in material changes to our financial statements.
Our significant accounting policies are further described in Note 2 to our audited consolidated financial statements included in "Item 8. Financial Statements and Supplemental Data" of this Annual Report on Form 10-K. We believe the following accounting policies include a higher degree of subjective and complex judgments in their application and are most critical to aid in fully understanding and evaluating our reported financial condition and results of operations.
Reserves and Resources
We prepare our reserves and resources estimates in accordance with SEC requirements. We have prepared these reserve and resources estimates and they have been reviewed and independently determined by mine consultants. We express tons of potash and langbeinite in resources and reserves in terms of expected finished tons of product to be realized, net of estimated losses. Market price fluctuations of potash or Trio®, as well as increased production costs or reduced recovery rates, could render resources and reserves containing relatively lower grades of mineralization uneconomic to exploit and might result in a reduction of resources and reserves.
We deplete our mineral properties using the units-of production method. Under this method, we determine a depletion rate for one ton of finished product by dividing the total mineral properties net balance by the number expected finished tons of product, which is obtained from the resources and reserve estimates. Depletion expense is calculated by multiplying the number of tons of product produced by the depletion rate per ton.
Indefinite-lived Intangible Assets
Water rights are accounted for as indefinite-lived intangible assets and are not amortized. We test indefinite-lived intangible assets for impairment at least annually on October 1, and more frequently if circumstances require. We use a qualitative assessment to determine whether it is more likely than not that the fair value of the intangible is less than its carrying value. If our qualitative assessment indicates it is more likely than not that the fair value of the intangible asset is less than its carrying value, we estimate the fair value of the intangible asset and record an impairment loss based on the excess of the carrying amount of the intangible asset over its estimated fair value. Fair value is estimated using quoted market prices, if available. If quoted market prices are not available, the estimated fair value is based on various valuation techniques, including the discounted value of estimated future cash flows. Changes in significant assumptions underlying fair value estimates may have a material effect on our financial position and results of operations.
Asset Retirement Obligations
All of our mining properties involve certain reclamation liabilities as required by the states in which they operate or by the BLM. Reclamation costs are initially recorded as a liability associated with the asset to be reclaimed or abandoned, based on
applicable inflation assumptions and discount rates. The accretion of this discounted liability is recognized as expense over the life of the related assets, and the liability is periodically adjusted to reflect changes in the estimates of the time or amount of the reclamation and abandonment costs. These asset retirement obligations are reviewed and updated at least annually with any changes in balances recorded as adjustments to the related assets and liabilities. The estimates of amounts to be spent are subject to considerable uncertainty and long timeframes. Changes in these estimates could have a material impact on our results of operations and financial position.
Income Taxes
We are a subchapter C corporation and therefore are subject to U.S. federal and state income taxes. We recognize income taxes under the asset and liability method. Deferred tax assets and liabilities are recognized for the estimated future tax consequences attributable to differences between the financial statement carrying amounts of assets and liabilities and their respective tax bases. Deferred tax assets and liabilities are measured using the enacted tax rates expected to apply to taxable income in the periods in which the deferred tax liability or asset is expected to be settled or realized. We record a valuation allowance if it is deemed more likely than not that our deferred income tax assets will not be realized in full; such determinations are subject to ongoing assessment.
Non-GAAP Financial Measure
To supplement our consolidated financial statements, which are prepared and presented in accordance with GAAP, from time to time we use "average net realized sales price per ton," which is a non-GAAP financial measure. This non-GAAP financial measure should not be considered in isolation or as a substitute for, or superior to, the financial information prepared and presented in accordance with GAAP. In addition, because the presentation of this non-GAAP financial measure varies among companies, our presentation of this non-GAAP financial measure may not be comparable to similarly titled measures used by other companies.
We believe average net realized sales price per ton provides useful information to investors for analysis of our business. We use this non-GAAP financial measure as one of our tools in comparing period-over-period performance on a consistent basis and when planning, forecasting, and analyzing future periods. We believe this non-GAAP financial measure is used by professional research analysts and others in the valuation, comparison, and investment recommendations of companies in the potash mining industry. Many investors use the published research reports of these professional research analysts and others in making investment decisions.
We calculate average net realized sales price per ton for each of potash and Trio®. Average net realized sales price per ton for potash is calculated as potash segment sales less potash segment byproduct sales and potash freight costs and then dividing that difference by the number of tons of potash sold in the period. Likewise, average net realized sales price per ton for Trio® is calculated as Trio® segment sales less Trio® segment byproduct sales and Trio® freight costs and then dividing that difference by Trio® tons sold. We consider average net realized sales price per ton to be useful, and believe it to be useful for investors, because it shows our potash and Trio® average per-ton pricing without the effect of certain transportation and delivery costs. When we arrange transportation and delivery for a customer, we include in revenue and in freight costs the costs associated with transportation and delivery. However, some of our customers arrange for and pay their own transportation and delivery costs, in which case these costs are not included in our revenue and freight costs. We use average net realized sales price per ton as a key performance indicator to analyze potash and Trio® sales and price trends.
Below is a reconciliation of average net realized sales price per ton for potash and Trio® and to the most directly comparable GAAP measure for the years ended December 31, 2021, 2020, and 2019 (in thousands, except per ton amounts):
| | | | | | | | | | | | | | | | | | | | |
| | Potash Segment |
| | 2021 | | 2020 | | 2019 |
Total Segment Sales | | $ | 151,751 | | | $ | 108,060 | | | $ | 124,648 | |
Less: Segment byproduct sales | | 21,291 | | | 15,560 | | | 21,245 | |
Potash freight costs | | 13,639 | | | 13,270 | | | 12,936 | |
Subtotal | | $ | 116,821 | | | $ | 79,230 | | | $ | 90,467 | |
| | | | | | |
Divided by: | | | | | | |
Potash tons sold (in thousands) | | 331 | | | 317 | | | 319 | |
Average net realized sales price per ton | | $ | 353 | | | $ | 250 | | | $ | 284 | |
| | | | | | | | | | | | | | | | | | | | |
| | Trio® Segment |
| | 2021 | | 2020 | | 2019 |
Total Segment Sales | | $ | 96,058 | | | $ | 70,287 | | | $ | 69,551 | |
Less: Segment byproduct sales | | 4,933 | | | 4,943 | | | 5,252 | |
Trio® freight costs | | 20,656 | | | 20,416 | | | 20,514 | |
Subtotal | | $ | 70,469 | | | $ | 44,928 | | | $ | 43,785 | |
| | | | | | |
Divided by: | | | | | | |
Trio® Tons sold (in thousands) | | 239 | | | 230 | | | 225 | |
Average net realized sales price per ton | | $ | 295 | | | $ | 195 | | | $ | 195 | |
ITEM 7A.QUANTITATIVE AND QUALITATIVE DISCLOSURES ABOUT MARKET RISK
Our operations may be impacted by commodity prices, geographic concentration, changes in interest rates, and foreign currency exchange rates.
Commodity Prices
Potash, Trio®, and water are commodities but are not traded on any commodity exchange. As such, direct hedging of future prices cannot be undertaken. For potash and Trio®, we generally do not enter into long-term sales contracts for these products, so prices vary for each particular transaction depending on the market into which we are selling and the individual bids that we receive. For water sales, we have entered into a diverse set of long-term agreements, where the price per barrel of water is fixed. Generally, these agreements allow for the parties to periodically review and adjust the price per barrel of water to the prevailing market price.
Our sales and profitability are determined principally by the price of potash, Trio®, and water. Potash and Trio® sales and profitability are also influenced, to a lesser extent, by the price of natural gas and other commodities used in production. The price of potash and Trio® is influenced by agricultural demand, global and domestic supply, competing specialty fertilizers, and the prices of agricultural commodities. Decreases in agricultural demand, increases in supply, or decreases in agricultural commodity prices could reduce our agricultural potash and Trio® sales. The price of water is influenced by demand from the oil and gas operators in the Permian Basin. Natural gas and oil price declines may result in a reduction in drilling activity, which could reduce our sales of water.
Our costs and capital investments are subject to market movements in other commodities such as natural gas, electricity, steel, and chemicals.
Interest Rate Fluctuations
Balances outstanding under our $75 million revolving credit facility bear interest at a floating rate of 1.25% to 2.00% above LIBOR, based on our leverage ratio. As of December 31, 2021, we had no borrowings outstanding on this facility and $1 million in an outstanding letter of credit under the facility. We occasionally borrow and repay amounts under the facility for near-term working capital needs.
Geographic Concentration
Our mines, facilities, and many of our customers are concentrated in the western half of United States and are, therefore, affected by weather and other conditions in this region.
Foreign Exchange Rate Fluctuations
We typically do not have balances of accounts receivable denominated in currencies other than U.S. dollars and, as a result, we do not have a direct foreign exchange risk. We do, however, have an indirect foreign exchange risk due to the industry in which we operate.
Specifically, the U.S. imports the majority of its potash, including from Canada, Russia, and Belarus. If the local currencies for foreign suppliers strengthen in comparison to the U.S. dollar, foreign suppliers realize a smaller margin in their local currencies unless they increase their nominal U.S. dollar prices. Strengthening of these local currencies therefore tends to
support higher U.S. potash prices as the foreign suppliers attempt to maintain their margins. However, if local currencies weaken in comparison to the U.S. dollar, foreign suppliers may choose to lower prices proportionally to increase sales volume while again maintaining a margin in their local currency.
ITEM 8.FINANCIAL STATEMENTS AND SUPPLEMENTARY DATA
Report of Independent Registered Public Accounting Firm
To the Stockholders and Board of Directors
Intrepid Potash, Inc.:
Opinions on the Consolidated Financial Statements and Internal Control Over Financial Reporting
We have audited the accompanying consolidated balance sheets of Intrepid Potash, Inc. and subsidiaries (the Company) as of December 31, 2021 and 2020, the related consolidated statements of operations, stockholders’ equity, and cash flows for each of the years in the three-year period ended December 31, 2021, and the related notes and financial statement schedule II (collectively, the consolidated financial statements). We also have audited the Company’s internal control over financial reporting as of December 31, 2021, based on criteria established in Internal Control – Integrated Framework (2013) issued by the Committee of Sponsoring Organizations of the Treadway Commission.
In our opinion, the consolidated financial statements referred to above present fairly, in all material respects, the financial position of the Company as of December 31, 2021 and 2020, and the results of its operations and its cash flows for each of the years in the three-year period ended December 31, 2021, in conformity with U.S. generally accepted accounting principles. Also in our opinion, the Company maintained, in all material respects, effective internal control over financial reporting as of December 31, 2021 based on criteria established in Internal Control – Integrated Framework (2013) issued by the Committee of Sponsoring Organizations of the Treadway Commission.
Basis for Opinions
The Company’s management is responsible for these consolidated financial statements, for maintaining effective internal control over financial reporting, and for its assessment of the effectiveness of internal control over financial reporting, included in the accompanying Management's Report on Internal Control over Financial Reporting. Our responsibility is to express an opinion on the Company’s consolidated financial statements and an opinion on the Company’s internal control over financial reporting based on our audits. We are a public accounting firm registered with the Public Company Accounting Oversight Board (United States) (PCAOB) and are required to be independent with respect to the Company in accordance with the U.S. federal securities laws and the applicable rules and regulations of the Securities and Exchange Commission and the PCAOB.
We conducted our audits in accordance with the standards of the PCAOB. Those standards require that we plan and perform the audits to obtain reasonable assurance about whether the consolidated financial statements are free of material misstatement, whether due to error or fraud, and whether effective internal control over financial reporting was maintained in all material respects.
Our audits of the consolidated financial statements included performing procedures to assess the risks of material misstatement of the consolidated financial statements, whether due to error or fraud, and performing procedures that respond to those risks. Such procedures included examining, on a test basis, evidence regarding the amounts and disclosures in the consolidated financial statements. Our audits also included evaluating the accounting principles used and significant estimates made by management, as well as evaluating the overall presentation of the consolidated financial statements. Our audit of internal control over financial reporting included obtaining an understanding of internal control over financial reporting, assessing the risk that a material weakness exists, and testing and evaluating the design and operating effectiveness of internal control based on the assessed risk. Our audits also included performing such other procedures as we considered necessary in the circumstances. We believe that our audits provide a reasonable basis for our opinions.
Definition and Limitations of Internal Control Over Financial Reporting
A company’s internal control over financial reporting is a process designed to provide reasonable assurance regarding the reliability of financial reporting and the preparation of financial statements for external purposes in accordance with generally accepted accounting principles. A company’s internal control over financial reporting includes those policies and procedures that (1) pertain to the maintenance of records that, in reasonable detail, accurately and fairly reflect the transactions and dispositions of the assets of the company; (2) provide reasonable assurance that transactions are recorded as necessary to permit preparation of financial statements in accordance with generally accepted accounting principles, and that receipts and expenditures of the company are being made only in accordance with authorizations of management and directors of the company; and (3) provide reasonable assurance regarding prevention or timely detection of unauthorized acquisition, use, or disposition of the company’s assets that could have a material effect on the financial statements.
Because of its inherent limitations, internal control over financial reporting may not prevent or detect misstatements. Also, projections of any evaluation of effectiveness to future periods are subject to the risk that controls may become inadequate because of changes in conditions, or that the degree of compliance with the policies or procedures may deteriorate.
Critical Audit Matter
The critical audit matter communicated below is a matter arising from the current period audit of the consolidated financial statements that was communicated or required to be communicated to the audit committee and that: (1) relates to accounts or disclosures that are material to the consolidated financial statements and (2) involved our especially challenging, subjective, or complex judgments. The communication of a critical audit matter does not alter in any way our opinion on the consolidated financial statements, taken as a whole, and we are not, by communicating the critical audit matter below, providing a separate opinion on the critical audit matter or on the accounts or disclosures to which it relates.
Realizability of deferred tax assets
As discussed in Notes 2 and 13 to the consolidated financial statements, the Company records a valuation allowance if it is deemed more likely than not deferred tax assets will not be realized in full. The ultimate realization of deferred tax assets is dependent upon the generation of certain types of future taxable income during the periods in which those temporary differences become deductible. In making this assessment, the Company considers the scheduled reversal of deferred tax liabilities, their ability to carry back the deferred tax assets, projected future taxable income, and tax planning strategies. The Company analyzes its valuation allowance using historical and projected future operating results. During 2021, the Company decreased its valuation allowance by $215.9 million as it concluded that it was more likely than not that it would realize its deferred tax assets.
We identified the evaluation of the realizability of the Company’s deferred tax assets as a critical audit matter. This evaluation required especially challenging auditor judgment to assess the Company’s estimated future taxable income over the period in which the deferred tax assets will generally reverse. Specifically, the Company’s assumptions of projected future taxable income were based primarily on prices for products subject to market volatility and forecasted sales volumes. Changes in these assumptions could have a significant impact on the realization of the Company’s deferred tax assets and the amount of the valuation allowance.
The following are the primary procedures we performed to address this critical audit matter. We evaluated the design and tested the operating effectiveness of certain internal controls related to the Company’s income tax process. This included controls related to the development of assumptions in determining the projected future taxable income, including the development of prices for products and forecasted sales volumes. We assessed the data used in the pricing assumptions used by the Company by comparing them to publicly available pricing data and existing contractual arrangements. We compared the forecasted sales volumes to historical sales volumes, and we compared the Company’s historical forecasted sales volumes to actual sales volumes to assess the Company’s ability to accurately forecast.
/s/ KPMG LLP
We have served as the Company's auditor since 2007.
Denver, Colorado
March 8, 2022
INTREPID POTASH, INC.
CONSOLIDATED BALANCE SHEETS
(In thousands, except share and per share amounts)
| | | | | | | | | | | | | | |
| | December 31, |
| | 2021 | | 2020 |
ASSETS | | | | |
Cash and cash equivalents | | $ | 36,452 | | | $ | 19,515 | |
| | | | |
Accounts receivable: | | | | |
Trade, net | | 35,409 | | | 22,516 | |
Other receivables, net | | 989 | | | 1,856 | |
| | | | |
Inventory, net | | 78,856 | | | 88,673 | |
Other current assets | | 5,144 | | | 3,228 | |
Total current assets | | 156,850 | | | 135,788 | |
Property, plant, equipment, and mineral properties, net | | 341,117 | | | 355,497 | |
Water rights | | 19,184 | | | 19,184 | |
Long-term parts inventory, net | | 29,251 | | | 28,900 | |
| | | | |
Other assets, net | | 11,418 | | | 10,819 | |
Non-current deferred tax asset, net | | 209,075 | | | — | |
Total Assets | | $ | 766,895 | | | $ | 550,188 | |
| | | | |
LIABILITIES AND STOCKHOLDERS' EQUITY | | | | |
| | | | |
Accounts payable | | $ | 9,068 | | | $ | 7,278 | |
| | | | |
Income taxes payable | | 41 | | | — | |
Accrued liabilities | | 22,938 | | | 12,701 | |
Accrued employee compensation and benefits | | 6,805 | | | 4,422 | |
Other current liabilities | | 34,571 | | | 32,816 | |
| | | | |
Current portion of long-term debt | | — | | | 10,000 | |
Total current liabilities | | 73,423 | | | 67,217 | |
| | | | |
Advances on credit facility | | — | | | 29,817 | |
Long-term debt, net | | — | | | 14,926 | |
Asset retirement obligation | | 27,024 | | | 23,872 | |
Operating lease liabilities | | 1,879 | | | 2,136 | |
Other non-current liabilities | | 1,166 | | | 961 | |
Total Liabilities | | 103,492 | | | 138,929 | |
| | | | |
Commitments and Contingencies | | | | |
| | | | |
Common stock, $0.001 par value; 40,000,000 shares authorized: | | | | |
and 13,149,315 and 13,049,820 shares outstanding | | | | |
at December 31, 2021, and 2020, respectively | | 13 | | | 13 | |
Additional paid-in capital | | 659,147 | | | 656,837 | |
| | | | |
Retained earnings (Accumulated deficit) | | 4,243 | | | (245,591) | |
Total Stockholders' Equity | | 663,403 | | | 411,259 | |
Total Liabilities and Stockholders' Equity | | $ | 766,895 | | | $ | 550,188 | |
See accompanying notes to these consolidated financial statements.
INTREPID POTASH, INC.
CONSOLIDATED STATEMENTS OF OPERATIONS
(In thousands, except share and per share amounts)
| | | | | | | | | | | | | | | | | | | | |
| | Year Ended December 31, |
| | 2021 | | 2020 | | 2019 |
Sales | | $ | 270,332 | | | $ | 196,954 | | | $ | 220,075 | |
Less: | | | | | | |
Freight costs | | 37,892 | | | 37,135 | | | 40,056 | |
Warehousing and handling costs | | 9,282 | | | 9,431 | | | 8,621 | |
Cost of goods sold | | 161,421 | | | 135,843 | | | 126,110 | |
Lower of cost or net realizable value inventory adjustments | | — | | | 4,015 | | | 1,810 | |
Costs associated with abnormal production | | 5,973 | | | — | | | — | |
Gross Margin | | 55,764 | | | 10,530 | | | 43,478 | |
| | | | | | |
Selling and administrative | | 23,998 | | | 25,476 | | | 23,556 | |
| | | | | | |
Accretion of asset retirement obligation | | 1,858 | | | 1,738 | | | 1,793 | |
Litigation settlement | | — | | | 10,075 | | | — | |
| | | | | | |
(Gain) loss on sale of assets | | (2,542) | | | (4,250) | | | 345 | |
Other operating expense | | 178 | | | 735 | | | 1,424 | |
Operating Income (Loss) | | 32,272 | | | (23,244) | | | 16,360 | |
| | | | | | |
Other Income (Expense) | | | | | | |
Interest expense, net | | (1,468) | | | (4,289) | | | (3,031) | |
| | | | | | |
Other income | | 48 | | | 384 | | | 355 | |
Gain on extinguishment of debt | | 10,113 | | | — | | | — | |
Income (Loss) Before Income Taxes | | 40,965 | | | (27,149) | | | 13,684 | |
| | | | | | |
Income Tax Benefit (Expense) | | 208,869 | | | (5) | | | (53) | |
Net Income (Loss) | | $ | 249,834 | | | $ | (27,154) | | | $ | 13,631 | |
| | | | | | |
Weighted Average Shares Outstanding: | | | | | | |
Basic | | 13,098,871 | | | 12,993,225 | | | 12,904,916 | |
Diluted | | 13,391,362 | | | 12,993,225 | | | 13,105,089 | |
Income (Loss) Per Share: | | | | | | |
Basic | | $ | 19.07 | | | $ | (2.09) | | | $ | 1.06 | |
Diluted | | $ | 18.66 | | | $ | (2.09) | | | $ | 1.04 | |
See accompanying notes to these consolidated financial statements.
INTREPID POTASH, INC.
CONSOLIDATED STATEMENTS OF STOCKHOLDERS' EQUITY
(In thousands, except share amounts)
| | | | | | | | | | | | | | | | | | | | | | | | | | | | | | | | | | |
| | Common Stock | | Additional Paid-in Capital(1) | | | | Retained Earnings (Accumulated) Deficit | | Total Stockholders' Equity |
| | Shares | | Amount(1) | | | | |
Balance, December 31, 2018 | | 12,871,659 | | | $ | 13 | | | $ | 649,318 | | | | | $ | (232,068) | | | $ | 417,263 | |
| | | | | | | | | | | | |
| | | | | | | | | | | | |
Net income | | — | | | — | | | — | | | | | 13,631 | | | 13,631 | |
Stock-based compensation | | — | | | — | | | 4,281 | | | | | — | | | 4,281 | |
Vesting of restricted shares, net of common stock used to fund employee income tax withholding due upon vesting | | 81,617 | | | — | | | (521) | | | | | — | | | (521) | |
Exercise of stock options | | 2,075 | | | — | | | 2 | | | | | — | | | 2 | |
Balance, December 31, 2019 | | 12,955,351 | | | 13 | | | 653,080 | | | | | (218,437) | | | 434,656 | |
| | | | | | | | | | | | |
Net loss | | — | | | — | | | — | | | | | (27,154) | | | (27,154) | |
Stock-based compensation | | — | | | — | | | 3,821 | | | | | — | | | 3,821 | |
Vesting of restricted shares, net of common stock used to fund employee income tax withholding due upon vesting | | 83,969 | | | — | | | (172) | | | | | — | | | (172) | |
Exercise of stock options | | 10,500 | | | — | | | 108 | | | | | — | | | 108 | |
Balance, December 31, 2020 | | 13,049,820 | | | 13 | | | 656,837 | | | | | (245,591) | | | 411,259 | |
| | | | | | | | | | | | |
| | | | | | | | | | | | |
| | | | | | | | | | | | |
Net income | | — | | | — | | | — | | | | | 249,834 | | | 249,834 | |
Stock-based compensation | | — | | | — | | | 3,012 | | | | | — | | | 3,012 | |
Vesting of restricted shares, net of common stock used to fund employee income tax withholding due upon vesting | | 90,844 | | | — | | | (791) | | | | | — | | | (791) | |
Exercise of stock options | | 8,651 | | | — | | | 89 | | | | | — | | | 89 | |
Balance, December 31, 2021 | | 13,149,315 | | | $ | 13 | | | $ | 659,147 | | | | | $ | 4,243 | | | $ | 663,403 | |
(1) - Amounts have been retroactively restated for all prior periods to reflect the one-for-ten reverse split of our common stock effected on August 14, 2020.
See accompanying notes to these consolidated financial statements.
INTREPID POTASH, INC.
CONSOLIDATED STATEMENTS OF CASH FLOWS
(In thousands) | | | | | | | | | | | | | | | | | | | | |
| | Year Ended December 31, |
| | 2021 | | 2020 | | 2019 |
Cash Flows from Operating Activities: | | | | | | |
Adjustments to reconcile net income (loss) to net cash provided by operating activities: | | | | | | |
Net income (loss) | | $ | 249,834 | | | $ | (27,154) | | | $ | 13,631 | |
| | | | | | |
| | | | | | |
Depreciation, depletion, and amortization | | 35,635 | | | 35,788 | | | 34,121 | |
Amortization of intangible assets | | 322 | | | 322 | | | 214 | |
Accretion of asset retirement obligation | | 1,858 | | | 1,738 | | | 1,793 | |
Amortization of deferred financing costs | | 314 | | | 425 | | | 303 | |
Stock-based compensation | | 3,012 | | | 3,821 | | | 4,281 | |
Reserve for obsolescence | | 2,108 | | | 492 | | | — | |
Allowance for doubtful accounts | | — | | | 75 | | | 75 | |
(Gain) Loss on disposal of assets | | (2,542) | | | (4,250) | | | 345 | |
Gain on extinguishment of debt | | (10,113) | | | — | | | — | |
Lower of cost or net realizable value inventory adjustments | | — | | | 4,015 | | | 1,810 | |
Other | | — | | | (116) | | | (34) | |
Changes in operating assets and liabilities: | | | | | | |
Trade accounts receivable, net | | (12,615) | | | 1,158 | | | 1,337 | |
Other receivables, net | | 589 | | | (609) | | | (650) | |
| | | | | | |
Inventory, net | | 7,358 | | | (291) | | | (11,525) | |
Other current assets | | (1,974) | | | 2,305 | | | (1,019) | |
Deferred tax assets, net | | (209,075) | | | — | | | — | |
Accounts payable, accrued liabilities, and accrued employee compensation and benefits | | 13,456 | | | 2,331 | | | 2,280 | |
Income tax payable | | 42 | | | (50) | | | (865) | |
Operating lease liabilities | | (2,508) | | | (2,234) | | | (2,090) | |
Other liabilities | | 3,366 | | | 13,379 | | | 5,374 | |
Net cash provided by operating activities | | 79,067 | | | 31,145 | | | 49,381 | |
| | | | | | |
Cash Flows from Investing Activities: | | | | | | |
Additions to property, plant, equipment, mineral properties and other assets | | (19,789) | | | (16,443) | | | (63,836) | |
Additions to intangible assets | | — | | | — | | | (16,873) | |
Proceeds from sale of property, plant, equipment, and mineral properties | | 6,042 | | | 4,786 | | | 68 | |
Long-term investment | | (1,076) | | | (3,500) | | | — | |
| | | | | | |
Net cash used in investing activities | | (14,823) | | | (15,157) | | | (80,641) | |
| | | | | | |
Cash Flows from Financing Activities: | | | | | | |
| | | | | | |
Repayment of long-term debt | | (15,000) | | | (35,000) | | | — | |
Debt prepayment costs | | (505) | | | (1,869) | | | — | |
Proceeds from loan under CARES Act | | — | | | 10,000 | | | — | |
Proceeds from borrowings on credit facility | | — | | | 10,000 | | | 30,317 | |
Repayments of borrowings on credit facility | | (29,817) | | | — | | | (10,500) | |
Payments of financing lease | | (1,258) | | | (74) | | | — | |
Capitalized debt costs | | — | | | (36) | | | (503) | |
Employee tax withholding paid for restricted shares upon vesting | | (791) | | | (172) | | | (540) | |
Proceeds from exercise of stock options | | 89 | | | 108 | | | 21 | |
Net cash (used in) provided by financing activities | | (47,282) | | | (17,043) | | | 18,795 | |
| | | | | | |
Net Change in Cash, Cash Equivalents, and Restricted Cash | | 16,962 | | | (1,055) | | | (12,465) | |
Cash, Cash Equivalents, and Restricted Cash, beginning of period | | 20,184 | | | 21,239 | | | 33,704 | |
Cash, Cash Equivalents, and Restricted Cash, end of period | | $ | 37,146 | | | $ | 20,184 | | | $ | 21,239 | |
| | | | | | |
Supplemental disclosure of cash flow information | | | | | | |
Net cash paid (received) during the period for: | | | | | | |
Interest, net of $0.1 million of capitalized interest in 2021, $0.1 million in 2020, and $0.2 million in 2019 | | $ | 875 | | | $ | 2,467 | | | $ | 2,733 | |
Income taxes | | $ | 193 | | | $ | 97 | | | $ | 942 | |
Accrued purchases for property, plant, equipment, and mineral properties | | $ | 2,192 | | | $ | 344 | | | $ | 5,021 | |
See accompanying notes to these consolidated financial statements.
INTREPID POTASH, INC.
NOTES TO CONSOLIDATED FINANCIAL STATEMENTS
"Intrepid," "our," "we," or "us" means Intrepid Potash, Inc. and its consolidated subsidiaries.
Note 1— COMPANY BACKGROUND
We are a diversified mineral company that delivers potassium, magnesium, sulfur, salt, and water products essential for customer success in agriculture, animal feed and the oil and gas industry. We are the only U.S. producer of muriate of potash (sometimes referred to as potassium chloride or potash), which is applied as an essential nutrient for healthy crop development, utilized in several industrial applications, and used as an ingredient in animal feed. In addition, we produce a specialty fertilizer, Trio®, which delivers three key nutrients, potassium, magnesium, and sulfate, in a single particle. We also provide water, magnesium chloride, brine and various oilfield products and services.
Our extraction and production operations are conducted entirely in the continental United States. We produce potash from three solution mining facilities: our HB solution mine in Carlsbad, New Mexico, our solution mine in Moab, Utah and our brine recovery mine in Wendover, Utah. We also operate our North compaction facility in Carlsbad, New Mexico, which compacts and granulates product from the HB mine. We produce Trio® from our conventional underground East mine in Carlsbad, New Mexico.
We have permitted, licensed, declared and partially adjudicated water rights in New Mexico under which we sell water primarily to support oil and gas development in the Permian Basin near our Carlsbad facilities. We continue to work to expand our sales of water. In May 2019, we acquired certain land, water rights, state grazing leases for cattle, and other related assets from Dinwiddie Cattle Company. We refer to these assets and operations as "Intrepid South." Due to the strategic location of Intrepid South, part of our long-term operating strategy is selling small parcels of land, including restricted use agreements of surface or subsurface rights, to customers, where such sales provide a solution to a customer's operations in the oil and gas industry.
We have three segments: potash, Trio®, and oilfield solutions. We account for the sales of byproducts as revenue in the potash or Trio® segment, based on which segment generates the byproduct. For each of the years ended December 31, 2021, 2020, and 2019, a majority of our byproduct sales were accounted for in the potash segment.
We manage sales and marketing operations centrally. This allows us to evaluate the product needs of our customers and then centrally determine which of our production facilities to use to fill customer orders in a manner designed to realize the highest average net realized sales price per ton. Average net realized sales price per ton is a non-GAAP measure that we calculate for each of potash and Trio® as segment sales less segment byproduct sales and segment freight costs, divided by the number of tons of product sold in the period. We also monitor product inventory levels and overall production costs centrally.
Note 2— SUMMARY OF SIGNIFICANT ACCOUNTING POLICIES
Basis of Presentation—Our consolidated financial statements include our accounts and those of our wholly-owned subsidiaries. All intercompany balances and transactions have been eliminated in consolidation.
Use of Estimates—The preparation of financial statements requires management to make estimates and assumptions that affect the reported amounts of assets and liabilities, the disclosure of contingent assets and liabilities as of the date of the financial statements, and the reported amounts of revenues and expenses during the reporting period. We base our estimates on historical experience and on various other assumptions that are believed to be reasonable under the circumstances. Accordingly, actual results may differ significantly from these estimates under different assumptions or conditions.
Significant estimates include, but are not limited to, those for proven and probable mineral reserves, the related present value of estimated future net cash flows, useful lives of plant assets, asset retirement obligations, normal inventory production levels, inventory valuations, the valuation of equity awards, revenue from products we sell to customers where the price is variable, the valuation of receivables, estimated future net cash flows used in long-lived assets impairment analysis, the related valuation of our long-lived assets, valuation of our deferred tax assets and estimated blended income tax rates utilized in the current and deferred income tax calculations. There are numerous uncertainties inherent in estimating quantities of proven and probable reserves, projecting future rates of production, and the timing of development expenditures. Future mineral prices may vary significantly from the prices in effect at the time the estimates are made, as may estimates of future operating costs. The estimate of proven and probable mineral reserves, the related present value of estimated future
cash flows, and useful lives of plant assets can affect various other items including depletion, the net carrying value of our mineral properties, the useful lives of related property, plant, and equipment, depreciation expense, and estimates associated with recoverability of long-lived assets and asset retirement obligations. Specific to income tax items, we experience fluctuations in the valuation of the deferred tax assets and liabilities due to changing income tax rates and the blend of state tax rates.
Revenue Recognition—We account for revenue in accordance with Accounting Standards Codification ("ASC") Topic 606 Revenue from Contracts with Customers ("ASC 606"). Under ASC 606, we recognize revenue when control of the promised goods or services is transferred to customers in an amount that reflects the consideration we expect to be entitled in exchange for those goods or services.
Performance Obligations: A performance obligation is a promise in a contract to transfer a distinct good or service to the customer and is the unit of account in ASC 606. The contract's transaction price is allocated to the performance obligations and recognized as revenue when the performance obligations are satisfied. Substantially all of our contracts are of a short-term nature and contain a single performance obligation because the sale is for one type of product and shipping and handling charges are accounted for as a fulfillment cost and are not considered to be a separate performance obligation. The performance obligation is satisfied when control of the product is transferred to the customer, which typically occurs when we ship mineral products or deliver water from our facility to the customer. We account for substantially all of our revenue from sales to customers at a single point in time.
Contract Estimates: In certain circumstances, we may sell product to customers where the sales price is variable. For variable consideration sales, we estimate the sales price we expect to realize at contract inception based on the facts and circumstances for each sale, including historical experience, and recognize revenue to the extent it is probable that a subsequent change in estimate will not result in a significant revenue reversal compared to the cumulative revenue recognized once the uncertainty is resolved. We update variable consideration estimates at each reporting date for any changes in facts and circumstances, and adjust financial information as necessary in the period the change is identified.
Contract Balances: The timing of revenue recognition, billings, and cash collection may result in contract assets or contract liabilities. For certain contracts, the customer has agreed to pay us before we have satisfied our performance obligations. Customer payments received before we have satisfied our performance obligations are accounted for as a contract liability.
Disaggregation of Revenue: We present disaggregation of revenue by products which we believe best depicts how the nature, amount, timing and uncertainty of revenue and cash flows are affected by economic conditions.
Inventory and Long-Term Parts Inventory—Inventory consists of product and byproduct stocks that are ready for sale; mined ore; potash in evaporation ponds, which is considered work-in-process; and parts and supplies inventory. Product and byproduct inventory cost is determined using the lower of weighted average cost or estimated net realizable value and includes direct costs, maintenance, operational overhead, depreciation, depletion, and equipment lease costs applicable to the production process. Direct costs, maintenance, and operational overhead include labor and associated benefits.
We evaluate our production levels and costs to determine if any should be deemed abnormal and therefore excluded from inventory costs and expensed directly during the applicable period. The assessment of normal production levels is judgmental and unique to each period. We model normal production levels and evaluate historical ranges of production by operating plant in assessing what is deemed to be normal. Each production operation typically shuts down periodically for planned maintenance activities. The costs of maintenance turnarounds at our facilities are considered part of production costs and are absorbed into inventory in the period incurred.
Parts inventory, including critical spares, that is not expected to be used within a period of one year is classified as non-current. Parts and supply inventory cost is determined using the lower of average acquisition cost or estimated replacement cost. Detailed reviews are performed related to the net realizable value of parts inventory, giving consideration to quality, slow-moving items, obsolescence, excessive levels, and other factors. Parts inventories that have not turned over in more than a year, excluding parts classified as critical spares, are reviewed for obsolescence and, if deemed appropriate, are included in the determination of an allowance for obsolescence.
Property, Plant, Equipment, Mineral Properties, and Development Costs—Property, plant, and equipment are stated at historical cost. Expenditures for property, plant, and equipment relating to new assets or improvements are capitalized, provided the expenditure extends the useful life of an asset or extends the asset's functionality. Property, plant, and equipment are depreciated under the straight-line method using estimated useful lives. The estimated useful lives of property, plant, and equipment are evaluated periodically as changes in estimates occur. No depreciation is taken on assets classified as construction in progress until the asset is placed into service. Gains and losses are recorded upon retirement, sale,
or disposal of assets. Maintenance and repair costs are recognized as period costs when incurred. Capitalized interest, to the extent of debt outstanding, is calculated and capitalized on assets that are being constructed, drilled, or built or that are otherwise classified as construction in progress.
Mineral properties and development costs, which are referred to collectively as mineral properties, include acquisition costs, the cost of drilling production wells, and the cost of other development work, all of which are capitalized. Exploration costs include geological and geophysical work performed on areas that that do not yet have proven and probable reserves declared. These costs are expensed as incurred. Depletion of mineral properties is calculated using the units-of-production method over the estimated life of the relevant ore body. The lives of reserves used for accounting purposes are shorter than current reserve life determinations due to uncertainties inherent in long-term estimates. These reserve life estimates have been prepared by us and reviewed and independently determined by mine consultants. Tons of potash and langbeinite in the proven and probable reserves are expressed in terms of expected finished tons of product to be realized, net of estimated losses. Market price fluctuations of potash or Trio®, as well as increased production costs or reduced recovery rates, could render proven and probable reserves containing relatively lower grades of mineralization uneconomic to exploit and might result in a reduction of reserves. In addition, the provisions of our mineral leases, including royalty provisions, are subject to periodic readjustment by the state and federal government, which could affect the economics of our reserve estimates. Significant changes in the estimated reserves could have a material impact on our results of operations and financial position.
Recoverability of Long-Lived Assets—We evaluate our long-lived assets for impairment when events or changes in circumstances indicate that the related carrying amount may not be recoverable. An impairment is potentially considered to exist if an asset group's total estimated net future cash flows on an undiscounted basis are less than the carrying amount of the related asset. An impairment loss is measured and recorded based on the excess of the carrying amount of long-lived assets over its estimated fair value. Changes in significant assumptions underlying future cash flow estimates or fair values of asset groups may have a material effect on our financial position and results of operations. Sales price is a significant element of any cash flow estimate, particularly for higher cost operations. Other assumptions we estimate include, among other things, the economic life of the asset, sales volume, inflation, raw materials costs, cost of capital, tax rates, and capital spending.
Factors we generally will consider important and which could trigger an impairment review of the carrying value of long-lived assets include the following:
•significant underperformance relative to expected operating results or operating losses
•significant changes in the manner of use of assets or the strategy for our overall business
•the denial or delay of necessary permits or approvals that would affect the utilization of our tangible assets
•underutilization of our tangible assets
•discontinuance of certain products by us or our customers
•a decrease in estimated mineral reserves
•significant negative industry or economic trends
Intangible Assets—Water rights are accounted for as indefinite-lived intangible assets. We test indefinite-lived intangible assets for impairment at least annually on October 1, and more frequently if circumstances require. We use a qualitative assessment to determine whether it is more likely than not that the fair value of the unamortized intangible is less than its carrying value. If our qualitative assessment indicates it is more likely than not that the fair value of the unamortized assets is less than its carrying value, we estimate the fair value of the unamortized asset and record an impairment loss based on the excess of the carrying amount of the unamortized intangible asset over its estimated fair value. Fair value is estimated using quoted market prices, if available. If quoted market prices are not available, the estimated fair value is based on various valuation techniques, including the discounted value of estimated future cash flows. Changes in significant assumptions underlying fair value estimates may have a material effect on our financial position and results of operations.
We also have finite-lived intangible assets consisting of contractual agreements. These intangible assets are amortized over the period of estimated benefit using the straight-line method. No significant residual value is estimated for our finite-lived intangible assets. We estimate the useful life of intangible assets considering various factors, including but not limited to, the expected use of the asset, the expected life of other assets the intangible asset may relate, any legal, regulatory, contractual provisions, or relevant economic factors that may limit the use of the intangible asset. We evaluate the remaining useful lives of intangible assets each reporting period to determine if a revision to the asset's remaining life is necessary. Changes in significant assumptions underlying useful lives may have a material effect on our financial position and results of operations.
We evaluate our finite-lived intangible assets for impairment when events or changes in circumstances indicate that the related carrying amount may not be recoverable. Such circumstances may include but are not limited to (1) significant
adverse changes in the manner the asset is used, or (2) significant adverse changes in legal factors or economic conditions, including adverse actions by regulatory authorities. We did not record any impairments to our intangible assets in 2021 and 2020.
Asset Retirement Obligations—Reclamation costs are initially recorded as a liability associated with the asset to be reclaimed or abandoned, based on applicable inflation assumptions and discount rates. The accretion of this discounted liability is recognized as expense over the life of the related assets, and the liability is periodically adjusted to reflect changes in the estimates of either the timing or amount of the reclamation and abandonment costs.
Leases—We determine if an arrangement is a lease or contains a lease at inception. Operating and finance lease liabilities are recognized based on the present value of the remaining lease payments, discounted using the discount rate for the lease at the commencement date. If readily determinable, we use the implicit rate in the lease to determine the present value of future lease payments. If the implicit rate is not readily determinable, we use an incremental borrowing rate based on information available at the commencement date to determine the present value of future lease payments. Operating right-of-use ("ROU") assets and finance lease assets are generally recognized based on the amount of the initial measurement of the lease liability. Lease expense for operating lease payments is recognized on a straight-line basis over the lease term. For finance leases, interest expense is recognized on the lease liability and the ROU asset is amortized over the lease term. We account for lease and non-lease components as a single lease component and we do not apply the requirements of ASC Topic 842 to short-term leases with a term of one year or less at inception.
Income Taxes—We are a subchapter C corporation and, therefore, are subject to U.S. federal and state income taxes. We recognize income taxes under the asset and liability method. Deferred tax assets and liabilities are recognized for the estimated future tax consequences attributable to differences between the financial statement carrying amounts of assets and liabilities and their respective tax bases. Deferred tax assets and liabilities are measured using the enacted tax rates expected to apply to taxable income in the periods in which the deferred tax liability or asset is expected to be settled or realized. We record a valuation allowance if it is deemed more likely than not that our deferred income tax assets will not be realized in full. These determinations are subject to ongoing assessment.
Cash and Cash Equivalents—Cash and cash equivalents consist of cash and liquid investments with an original maturity of three months or less.
Fair Value of Financial Instruments—Our financial instruments include cash and cash equivalents, restricted cash, accounts receivable, refundable income taxes, accounts payable and current accrued liabilities. These instruments are carried at cost, which approximates fair value due to the short-term maturities of the instruments. Allowances for doubtful accounts are recorded against the accounts receivable balance to estimate net realizable value. Amounts outstanding under our secured credit facility are carried at cost, which approximates fair value, due to the short-term nature of the borrowings.
Earnings per Share—Basic net income or loss per common share of stock is calculated by dividing net income or loss available to common stockholders by the weighted average basic common shares outstanding for the respective period.
Diluted net income per common share of stock is calculated by dividing net income by the weighted average diluted common shares outstanding, which includes the effect of potentially dilutive securities. Potentially dilutive securities for the diluted earnings or loss per share calculation consist of awards of restricted shares, performance units, and non‑qualified stock options. The dilutive effect of stock-based compensation arrangements is computed using the treasury‑stock method. Following the lapse of the vesting period of restricted shares, the shares are considered issued and therefore are included in the number of issued and outstanding shares for purposes of these calculations. When we report a net loss, all potentially dilutive securities are considered anti-dilutive and are excluded from the dilutive loss per share calculation.
Reverse Stock Split—On August 10, 2020, after receiving stockholder approval, the Board of Directors approved an amendment to Certificate of Incorporation to effect a reverse stock split of our common stock, par value $0.001 per share, by a ratio of one-for-ten. The reverse stock split was effected on August 14, 2020. Additionally, the total number of authorized shares of our common stock was reduced to 40,000,000 shares. Unless otherwise indicated, all share amounts, per share data, share prices, exercise prices and conversion rates set forth in these notes and the accompanying consolidated financial statements have, where applicable, been adjusted retroactively to reflect this reverse stock split.
Stock‑Based Compensation—We account for stock-based compensation by recording expense using the fair value of the awards at the time of grant. We have recorded compensation expense associated with the issuance of restricted shares, performance units, and non-qualified stock options, all of which are subject to service conditions and in some cases subject to operational performance or market-based conditions. We recognize expense associated with such awards over the service period associated with each grant. For awards with service only conditions we recognize expense using the straight-line recognition method over the requisite service period of the award, which is generally the vesting period of the award. We
recognize expense for awards with service and operational performance conditions using the accelerated recognition method over the requisite service period of the award, which is generally the vesting period of the award. We recognize expense associated with awards that contain both a service condition and a market condition using the accelerated recognition method over the requisite service period of the award, which is generally the longer of the explicit service period or the derived service period (expected date the market condition is estimated to be achieved).
Recently Adopted Accounting Standards—In June 2016, the Financial Accounting Standards Board ("FASB") issued Accounting Standards Update ("ASU") No. 2016-13, as amended by ASU No. 2019-04 and ASU No. 2019-10, Financial Instruments - (Topic 326): Measurement of Credit Losses on Financial Instruments ("ASC Topic 326"), which we adopted on January 1, 2020. ASC Topic 326 changed the way entities recognized impairment of many financial assets by requiring immediate recognition of estimated credit losses expected to occur over their remaining life. Because our trade receivables are short-term in nature, the adoption of this new standard did not have a material impact on our consolidated financial statements.
In December 2019, the FASB issued ASU 2019-12, Income Taxes (Topic 740): Simplifying the Accounting for Income Taxes, which simplifies the accounting for income taxes by removing certain exceptions to the general principles in Topic 740 and amending existing guidance to improve consistent application. The adoption of this standard did not have a material impact on our consolidated financial statements.
Pronouncements Issued But Not Yet Adopted—In March 2020, the FASB issued ASU No. 2020-04, Reference Rate Reform (Topic 848): Facilitation of the Effects of Reference Rate Reform on Financial Reporting ("ASU 2020-04"), which provides optional exceptions to GAAP for certain transactions related to the transition away from The London Interbank Offered Rate ("LIBOR"). The amended guidance is designed to provide relief from the accounting analysis and impacts that may otherwise be required for modifications to agreements necessitated by the reference rate reform. Application of the guidance in ASU 2020-04 is optional, is only available in certain situations, and is only available for companies to apply until December 31, 2022. We are currently evaluating the impacts of reference rate reform and the guidance in ASU 2020-04 on our consolidated financial statements.
Note 3— EARNINGS PER SHARE
Basic earnings per share is computed by dividing net income or loss by the weighted-average number of shares of common stock outstanding during the period. For purposes of determining diluted earnings per share, basic weighted-average common shares outstanding is adjusted to include potentially dilutive securities, including restricted stock, stock options, and performance units. The treasury-stock method is used to measure the dilutive impact of potentially dilutive shares. Potentially dilutive shares are excluded from the diluted weighted-average shares outstanding computation in periods in which they have an anti-dilutive effect. The following table shows the calculation of basic and diluted earnings (loss) per share (in thousands, except per share amounts):
| | | | | | | | | | | | | | | | | | | | |
| | Year Ended December 31, |
| | 2021 | | 2020 | | 2019 |
Net income (loss) | | $ | 249,834 | | | $ | (27,154) | | | $ | 13,631 | |
| | | | | | |
Basic weighted average common shares outstanding | | 13,099 | | | 12,993 | | | 12,905 | |
Add: Dilutive effect restricted common stock | | 221 | | | — | | | 121 | |
Add: Dilutive effect of stock options outstanding | | 71 | | | — | | | 79 | |
| | | | | | |
Diluted weighted average common shares outstanding | | 13,391 | | | 12,993 | | | 13,105 | |
| | | | | | |
Earnings (loss) per share: | | | | | | |
Basic | | $ | 19.07 | | | $ | (2.09) | | | $ | 1.06 | |
Diluted | | $ | 18.66 | | | $ | (2.09) | | | $ | 1.04 | |
The following table shows anti-dilutive shares excluded from the calculation of diluted earnings (loss) per share (in thousands):
| | | | | | | | | | | | | | | | | | | | |
| | Year Ended December 31, |
| | 2021 | | 2020 | | 2019 |
Anti-dilutive effect of restricted shares | | 57 | | | 246 | | | 50 | |
Anti-dilutive effect of stock options outstanding | | 156 | | | 309 | | | 165 | |
| | | | | | |
Note 4— CASH, CASH EQUIVALENTS AND RESTRICTED CASH
Total cash, cash equivalents and restricted cash, as shown on the consolidated statements of cash flows are included in the following accounts at December 31, 2021, 2020, and 2019 (in thousands):
| | | | | | | | | | | | | | | | | |
| Year Ended December 31, |
| 2021 | | 2020 | | 2019 |
Cash and cash equivalents | $ | 36,452 | | | $ | 19,515 | | | $ | 20,603 | |
Restricted cash included in "Other current assets" | 175 | | | 150 | | | 150 | |
Restricted cash included in "Other assets, net" | 519 | | | 519 | | | 486 | |
Total cash, cash equivalents, and restricted cash shown in the statement of cash flows | $ | 37,146 | | | $ | 20,184 | | | $ | 21,239 | |
Restricted cash included in "Other assets, net" on the balance sheet at December 31, 2021, 2020, and 2019 represents amounts whose use is restricted by contractual agreements with the Bureau of Land Management or the State of Utah as security to fund future reclamation obligations at our sites. Restricted cash included in "Other current assets" on the balance sheet at December 31, 2021 represents cash deposits with supply vendors.
Note 5— INVENTORY AND LONG-TERM PARTS INVENTORY
The following summarizes our inventory, recorded at the lower of weighted average cost or estimated net realizable value as of December 31, 2021, and 2020, respectively (in thousands):
| | | | | | | | | | | | | | |
| | December 31, |
| | 2021 | | 2020 |
Finished goods product inventory | | $ | 42,492 | | | $ | 48,961 | |
In-process inventory | | 27,211 | | | 28,833 | |
Total product inventory | | 69,703 | | | 77,794 | |
Current parts inventory, net | | 9,153 | | | 10,879 | |
Total current inventory, net | | 78,856 | | | 88,673 | |
Long-term parts inventory, net | | 29,251 | | | 28,900 | |
Total inventory, net | | $ | 108,107 | | | $ | 117,573 | |
During the year ended December 31, 2021, we recorded no charges for lower of weighted average cost or estimated net realizable value on our finished goods product inventory. During the years ended December 31, 2020 and 2019, we recorded charges or approximately, $4.0 million, and $1.8 million, respectively, as a result of routine assessments of the lower of weighted average cost or estimated net realizable value on our finished goods product inventory.
Parts inventories are shown net of any required allowances.
Note 6— PROPERTY, PLANT, EQUIPMENT, AND MINERAL PROPERTIES
"Property, plant, equipment, and mineral properties, net" were comprised of the following (in thousands):
| | | | | | | | | | | | | | | | | | |
| | December 31, | | |
| | 2021 | | 2020 | | | | |
Land | | $ | 24,136 | | | $ | 27,263 | | | | | |
Ponds and land improvements | | 69,261 | | | 67,843 | | | | | |
Mineral properties and development costs | | 144,255 | | | 143,955 | | | | | |
Buildings and plant | | 84,268 | | | 81,692 | | | | | |
Machinery and equipment | | 272,323 | | | 265,121 | | | | | |
Vehicles | | 6,855 | | | 5,919 | | | | | |
Office equipment and leasehold improvements | | 8,956 | | | 9,083 | | | | | |
Operating lease ROU assets | | 7,763 | | | 9,622 | | | | | |
Breeding stock | | 308 | | | 260 | | | | | |
Construction in progress | | 11,469 | | | 1,710 | | | | | |
Total property, plant, equipment, and mineral properties, gross | | $ | 629,594 | | | $ | 612,468 | | | | | |
Less: accumulated depreciation, depletion, and amortization | | (288,477) | | | (256,971) | | | | | |
Total property, plant, equipment, and mineral properties, net | | $ | 341,117 | | | $ | 355,497 | | | | | |
We incurred the following expenses for depreciation, depletion, and amortization of ROU assets, including expenses capitalized into inventory, for the following periods (in thousands):
| | | | | | | | | | | | | | | | | | | | |
| | Year Ended December 31, |
| | 2021 | | 2020 | | 2019 |
Depreciation | | $ | 29,447 | | | $ | 29,697 | | | $ | 27,889 | |
Depletion | | 3,979 | | | 3,952 | | | 4,173 | |
Amortization of ROU assets | | 2,209 | | | 2,139 | | | 2,059 | |
Total incurred | | $ | 35,635 | | | $ | 35,788 | | | $ | 34,121 | |
Note 7— LEASES
We determine if an arrangement is a lease or contains a lease at inception. We have operating leases for mining equipment, trucks, rail cars, and office space. Our operating leases have remaining leases terms ranging from less than one year to five years. Leases recorded on the balance sheet consist of the following (amounts in thousands):
| | | | | | | | | | | | | | | | | | | | |
Leases | | Classification on the Balance Sheet | | Balance, December 31, 2021 | | Balance, December 31, 2020 |
Assets | | | | | | |
Operating lease ROU assets, net | | Property, plant, equipment, and mineral properties, net | | $ | 3,398 | | | $ | 4,091 | |
Finance lease ROU assets, net | | Property, plant, equipment, and mineral properties, net | | $ | — | | | $ | 1,301 | |
Liabilities | | | | | | |
Current operating lease liabilities | | Other current liabilities | | $ | 1,655 | | | $ | 2,057 | |
Current finance lease liability | | Other current liabilities | | $ | — | | | 1,258 | |
Non-current operating lease liabilities | | Operating lease liabilities | | $ | 1,879 | | | $ | 2,136 | |
Other information related to lease term and discount rate is as follows:
| | | | | | | | | | | | | | |
| | December 31, 2021 | | December 31, 2020 |
Weighted average remaining lease term - operating leases | | 2.5 years | | 2.4 years |
Weighted average remaining lease term - finance leases | | 0.00 years | | 0.30 years |
| | | | |
Weighted average discount rate - operating leases | | 4.59 | % | | 5.49 | % |
Weighted average discount rate - finance leases | | — | % | | 1.75 | % |
The components of lease expense are as follows (amounts in thousands):
| | | | | | | | | | | | | | | | | | | | |
| | For the Year Ended December 31, 2021 | | For the Year Ended December 31, 2020 | | For the Year Ended December 31, 2019 |
Operating lease expense | | $ | 2,370 | | | $ | 2,434 | | | $ | 2,410 | |
Short-term lease expense | | 122 | | | 117 | | | 107 | |
Total lease expense | | $ | 2,492 | | | $ | 2,551 | | | $ | 2,517 | |
Supplemental cash flow information related to leases was as follows (amounts in thousands):
| | | | | | | | | | | | | | |
| | For the Year Ended December 31, 2021 | | For the Year Ended December 31, 2020 |
Cash paid for amounts included in the measurement of lease liabilities | | | | |
Operating cash flows from operating leases | | $ | 2,336 | | | $ | 2,480 | |
Finance cash flows from finance leases | | 1,258 | | | 74 | |
| | | | |
Right-of-Use Assets exchanged for new operating lease liabilities | | 1,849 | | | 216 | |
Right-of-Use Assets exchanged for new finance lease liabilities | | — | | | 1,332 | |
As of December 31, 2021, maturities of lease liabilities are summarized as follows (amounts in thousands):
| | | | | | | | | | | | |
Years Ending December 31, | | Operating Leases | | | | |
2022 | | $ | 1,781 | | | | | |
2023 | | 1,010 | | | | | |
2024 | | 658 | | | | | |
2025 | | 145 | | | | | |
2026 | | 7 | | | | | |
Thereafter | | — | | | | | |
Total future minimum lease payments | | $ | 3,601 | | | | | |
Less - amount representing interest | | 67 | | | | | |
Present value of future minimum lease payments | | $ | 3,534 | | | | | |
Less - current lease obligations | | 1,655 | | | | | |
Long-term lease obligations | | $ | 1,879 | | | | | |
Note 8— INTANGIBLE ASSETS
We acquired certain water rights, recorded at $16.9 million, and other intangible assets, recorded at $6.4 million, in the Intrepid South asset acquisition that we completed in May 2019. We account for our water rights as indefinite-lived intangible assets.
We account for the other intangible assets acquired in the Intrepid South asset acquisition as finite-lived intangible assets and amortize those intangible assets over the period of estimated benefit, using the straight-line method. The weighted-average amortization period for the other intangible assets acquired in the Intrepid South asset acquisition was 20 years. These intangible assets are included in "Other assets, net" on the consolidated balance sheets.
As of December 31, 2021, and December 31, 2020, we have the following amounts recorded for intangible assets (amounts in thousands):
| | | | | | | | | | | | | | | | | | | | | | | | | | | | | | |
| | December 31, 2021 | | December 31, 2020 | | |
Finite-lived intangible assets: | | Gross Carrying Amount | | Accumulated Amortization | | Gross Carrying Amount | | Accumulated Amortization | | | | |
Produced water disposal royalty agreements | | $ | 2,694 | | | $ | (360) | | | $ | 2,694 | | | $ | (225) | | | | | |
Surface damage and easement agreements | | 3,723 | | | (498) | | | 3,723 | | | (311) | | | | | |
Total | | $ | 6,417 | | | $ | (858) | | | $ | 6,417 | | | $ | (536) | | | | | |
| | | | | | | | | | | | |
Indefinite-lived intangible assets: | | | | | | | | | | | | |
Water rights | | $ | 19,184 | | | | | $ | 19,184 | | | | | | | |
Total amortization of intangible assets for the years ended December 31, 2021, and 2020, was $0.3 million. Total amortization for 2019 was $0.2 million. We estimate the annual amortization expense of intangible assets will be $0.3 million for each of the next five years.
Note 9— DEBT
Credit Facility—We maintain a secured revolving credit facility with Bank of Montreal. Borrowings under the credit facility bore interest at LIBOR (London Interbank Offered Rate) plus an applicable margin of 1.25% to 2.00% per annum, based on our leverage ratio. We have granted to Bank of Montreal a first lien on substantially all of our current assets and a second lien on substantially all of our non-current assets. The obligations under the credit facility are unconditionally guaranteed by several of our subsidiaries.
We occasionally borrow and repay amounts under the facility for near-term working capital needs or other purposes and may do so in the future. For the year ended December 31, 2021, we made no borrowings and repaid $29.8 million under the facility. For the year ended December 31, 2020, we borrowed $10.0 million and made no repayments, under the facility. As of December 31, 2021, we had no borrowings outstanding and $1.0 million in an outstanding letter of credit under the facility. As of December 31, 2020, we had $29.8 million of borrowings outstanding and $1.0 million in an outstanding letter of credit under the facility. We had $74.0 million available under the facility as of December 31, 2021.
We were in compliance with the applicable covenants under the facility as of December 31, 2021.
PPP Loan—In April 2020, we received a $10 million loan under the CARES Act Paycheck Protection Program (the "PPP"). We submitted our application for forgiveness of the full amount of the loan in November 2020. In June 2021, we received notice that the SBA had remitted funds to our bank to fully repay our PPP loan and accrued interest. Accordingly, we recognized a gain of $10.1 million related to the forgiveness of the PPP loan and the associated accrued interest on the loan.
Senior Notes—In June 2021 we repaid the remaining $15.0 million of principal outstanding on our Series B Senior Notes and satisfied all obligations under the related Note Purchase Agreement. In connection with this repayment, the Company paid in aggregate approximately $15.6 million, which consisted of (i) $15.0 million of remaining aggregate principal amount of Series B Senior Notes, (ii) approximately $0.1 million of accrued interest and (iii) a "make-whole" premium of $0.5 million. As a result of the repayment, the Note Purchase Agreement was terminated. As of December 31, 2020, we had outstanding $15.0 million of Series B Senior Notes.
Our total outstanding long-term debt, net, as of December 31, 2020, was as follows (in thousands):
| | | | | | | |
| | | December 31, 2020 |
Notes and Payroll Protection Loan | | | $ | 25,000 | |
Less current portion of long-term debt | | | (10,000) | |
Less deferred financing costs | | | (74) | |
Long-term portion of Notes, net | | | $ | 14,926 | |
Interest Expense—Interest expense is recorded net of any capitalized interest associated with investments in capital projects. We incurred gross interest expense of $1.5 million, $4.4 million, and $3.2 million for the years ended December 31, 2021, 2020, and 2019, respectively.
Amounts included in interest expense for the years ended December 31, 2021, 2020, and 2019 (in thousands) are as follows:
| | | | | | | | | | | | | | | | | | |
| Year ended December 31, |
| 2021 | | 2020 | | 2019 | |
Interest expense on borrowings | $ | 724 | | | $ | 2,107 | | | $ | 2,908 | | |
Make-whole payments | 505 | | | 1,868 | | | — | | |
Amortization of deferred financing costs | 314 | | | 425 | | | 303 | | |
Gross interest expense | 1,543 | | | 4,400 | | | 3,211 | | |
Less capitalized interest | 75 | | | 111 | | | 180 | | |
Interest expense, net | $ | 1,468 | | | $ | 4,289 | | | $ | 3,031 | | |
Note 10— ASSET RETIREMENT OBLIGATION
We recognize an estimated liability for future costs associated with the abandonment and reclamation of our mining properties. A liability for the fair value of an asset retirement obligation and a corresponding increase to the carrying value of the related long-lived asset are recorded as the mining operations occur or the assets are acquired.
Our asset retirement obligation is based on the estimated cost to abandon and reclaim the mining operations, the economic life of the properties, and federal and state regulatory requirements. The liability is discounted using credit adjusted risk-free rate estimates at the time the liability is incurred or when there are upward revisions to estimated costs. The credit adjusted risk-free rates used to discount our abandonment liabilities range from 6.9% to 9.7%. Revisions to the liability occur due to construction of new or expanded facilities, changes in estimated abandonment costs or economic lives, changes in the estimated timing of the reclamation activities or if federal or state regulators enact new requirements regarding the abandonment or reclamation of mines.
Following is a table of the changes to our asset retirement obligations for the following periods (in thousands):
| | | | | | | | | | | | | | | | | | | | |
| | Year Ended December 31, |
| | 2021 | | 2020 | | 2019 |
Asset retirement obligation, at beginning of period | | $ | 23,872 | | | $ | 22,250 | | | $ | 23,125 | |
Liabilities settled | | — | | | (116) | | | (38) | |
Liabilities incurred | | — | | | — | | | 60 | |
Changes in estimated obligations | | 1,294 | | | — | | | (2,690) | |
Accretion of discount | | 1,858 | | | 1,738 | | | 1,793 | |
Total asset retirement obligation, at end of period | | $ | 27,024 | | | $ | 23,872 | | | $ | 22,250 | |
We estimate approximately $6.7 million in payments may occur in the next five years.
Note 11— REVENUE
Revenue Recognition—Under ASC 606, we recognize revenue when control of the promised goods or services is transferred to customers in an amount that reflects the consideration we expect to be entitled in exchange for those goods or services.
Contract Balances—As of December 31, 2021, and 2020, we had $33.8 million and $30.4 million of contract liabilities, respectively, the majority of which are included in "Other current liabilities" on the consolidated balance sheets, primarily related to cash advances received from a customer for water purchases. Customer advances received before we have satisfied our performance obligations are accounted for as a contract liability (sometimes referred to in practice as deferred revenue). We will recognize the deferred revenue at the time the customer calls for water delivery, which we expect will be sourced from our existing long-term water rights. Our contract liability activity for the years ended December 31, 2021, 2020, and 2019 is shown below (in thousands):
| | | | | | | | | | | | | | | | | | | | |
| | Year Ended December 31, |
| | 2021 | | 2020 | | 2019 |
Beginning balance | | $ | 30,419 | | | $ | 16,612 | | | $ | 11,678 | |
Additions | | 4,310 | | | 17,657 | | | 11,058 | |
Recognized as revenue during period from the beginning balance | | (941) | | | (3,850) | | | (6,124) | |
Ending balance | | $ | 33,788 | | | $ | 30,419 | | | $ | 16,612 | |
Disaggregation of Revenue—The table below shows the disaggregation of revenue by product and reconciles disaggregated revenue to segment revenue for the years ended December 31, 2021, 2020, and 2019. We believe the disaggregation of revenue by products best depicts how the nature, amount, timing and uncertainty of revenue and cash flows are affected by economic conditions (in thousands):
| | | | | | | | | | | | | | | | | | | | | | | | | | | | | | | | |
| | Year Ended December 31, 2021 |
Product | | Potash Segment | | Trio® Segment | | Oilfield Solutions Segment | | Intersegment Eliminations | | Total |
Potash | | $ | 130,460 | | | $ | — | | | $ | — | | | $ | (247) | | | $ | 130,213 | |
Trio® | | — | | | 91,125 | | | — | | | — | | | 91,125 | |
Water | | 2,050 | | | 4,355 | | | 15,594 | | | — | | | 21,999 | |
Salt | | 9,592 | | | 578 | | | — | | | — | | | 10,170 | |
Magnesium Chloride | | 7,847 | | | — | | | — | | | — | | | 7,847 | |
Brines | | 1,802 | | | — | | | 1,129 | | | — | | | 2,931 | |
Other | | — | | | — | | | 6,047 | | | — | | | 6,047 | |
Total Revenue | | $ | 151,751 | | | $ | 96,058 | | | $ | 22,770 | | | $ | (247) | | | $ | 270,332 | |
| | | | | | | | | | | | | | | | | | | | | | | | | | | | | | | | |
| | Year Ended December 31, 2020 |
Product | | Potash Segment | | Trio® Segment | | Oilfield Solutions Segment | | Intersegment Eliminations | | Total |
Potash | | $ | 92,500 | | | $ | — | | | $ | — | | | $ | (322) | | | $ | 92,178 | |
Trio® | | — | | | 65,344 | | | — | | | — | | | 65,344 | |
Water | | 1,253 | | | 4,444 | | | 14,701 | | | — | | | 20,398 | |
Salt | | 8,103 | | | 499 | | | — | | | — | | | 8,602 | |
Magnesium Chloride | | 4,855 | | | — | | | — | | | — | | | 4,855 | |
Brines | | 1,349 | | | — | | | 438 | | | — | | | 1,787 | |
Other | | — | | | — | | | 3,790 | | | — | | | 3,790 | |
Total Revenue | | $ | 108,060 | | | $ | 70,287 | | | $ | 18,929 | | | $ | (322) | | | $ | 196,954 | |
| | | | | | | | | | | | | | | | | | | | | | | | | | | | | | | | |
| | Year Ended December 31, 2019 |
Product | | Potash Segment | | Trio® Segment | | Oilfield Solutions Segment | | Intersegment Eliminations | | Total |
Potash | | $ | 103,403 | | | $ | — | | | $ | 2,973 | | | $ | (1,909) | | | $ | 104,467 | |
Trio® | | — | | | 64,299 | | | — | | | — | | | 64,299 | |
Water | | 1,823 | | | 4,495 | | | 19,339 | | | — | | | 25,657 | |
Salt | | 12,022 | | | 757 | | | — | | | — | | | 12,779 | |
Magnesium Chloride | | 4,907 | | | — | | | — | | | — | | | 4,907 | |
Brines | | 2,493 | | | — | | | — | | | — | | | 2,493 | |
Other | | — | | | — | | | 5,582 | | | (109) | | | 5,473 | |
Total Revenue | | $ | 124,648 | | | $ | 69,551 | | | $ | 27,894 | | | $ | (2,018) | | | $ | 220,075 | |
Note 12— COMPENSATION PLANS
Cash Bonus Programs—We use cash bonus programs under which our employees may be eligible to receive cash bonuses based on corporate, department, location, or individual performance or other events or accomplishments. We accrue cash bonus expense related to the current year's performance and we expect to pay in early 2022 a cash bonus to our employees under our 2021 bonus program. While we did meet certain performance metrics related to our 2020 cash bonus program, we did not pay a cash bonus under our 2020 cash bonus program. We did not meet our performance metrics related to the 2019 cash bonus program, and accordingly, we did not pay a cash bonus for 2019 under the program.
Equity Incentive Compensation Plan—Our Board of Directors and stockholders adopted a long-term incentive compensation plan called the Intrepid Potash, Inc. Amended and Restated Equity Incentive Plan (the "Plan"). We have issued restricted shares, common stock, performance units, and non-qualified stock option awards under the Plan. As of December 31, 2021, 407,597 restricted shares and options to purchase 283,924 shares of common stock were outstanding. As of December 31, 2021, approximately 0.6 million shares of common stock remained available for issuance under the Plan. Total compensation expense related to the Plan was $3.0 million, $3.8 million, and $4.3 million, for the years ended December 31, 2021, 2020, and 2019, respectively. As of December 31, 2021, there was $6.7 million of total remaining unrecognized compensation expense that is expected to be recognized over a weighted-average period of 1.5 years. When restricted shares and performance units vest and when stock options are exercised, new shares are issued and considered outstanding for financial statement purposes.
Restricted Shares
•Restricted Shares with Service Conditions—Under the Plan, the Compensation Committee of the Board of Directors (the "Compensation Committee") has granted restricted shares of common stock to members of the Board of Directors, executive officers, and other key employees. The restricted shares contain service conditions associated with continued employment or service. The restricted shares provide voting and regular dividend rights to the holders of the awards.
In 2021, the Compensation Committee granted 76,869 restricted shares to executives and key employees under the Plan as part of our annual equity award program. The awards vest over three years, subject to continued employment or service.
In 2021, the Compensation Committee granted 19,480 restricted shares to non-employee members of the Board of Directors. The restricted shares vest one year after the date of grant, subject to continued service.
We use the closing price of our common stock on the grant date as the grant date fair value for these awards. We record compensation expense monthly using the straight-line recognition method over the vesting period of the award. The weighted-average grant date fair value per share for restricted shares with service conditions issued in 2021, 2020, and 2019 was $37.49, $14.49, and $34.70, respectively.
•Restricted Shares with Service and Market Conditions— Under the Plan in March 2021, the Compensation Committee granted restricted shares of common stock with service and market conditions to certain members of our executive team as part of their annual compensation package. The grants vest over three years from the quarter ended in which the volume-weighted average share closing price for 20 consecutive days has met one of the applicable price achievement targets; provided, however, that no vesting would occur if the volume-weighted average closing price for 20 consecutive days has not met one or more applicable price achievement goals on or before March 11, 2024. The share price achievement goals of these awards have been met as of December 31, 2021, and will vest over three years subject to continued employment.
Under the Plan in December 2021, the Compensation Committee granted restricted shares of common stock with service and market conditions to a member of our executive team as part of his annual compensation package. This grant vests over two years from the quarter ended in which the volume-weighted average share closing price for 20 consecutive trading days has met one of the applicable price achievement targets; provided, however, that no vesting would occur if the volume-weighted average closing price for 20 consecutive trading days has not met one or more applicable price achievement goals on or before December 23, 2025. As of December 31, 2021, share price achievement goals have not been met.
Under the plan in 2020 and 2019, the Compensation Committee granted restricted shares of common stock with service and market conditions to a member of our executive team as part of his annual compensation package.
The 2020 grant vests over two years from the quarter ended in which the volume weighted average share closing price for 20 consecutive trading days has met one of the applicable price achievement targets; provided, however, that no vesting would occur if the volume-weighted average closing price for 20 consecutive trading days has not met one or more applicable price achievement goals on or before June 8, 2024. As of December 31, 2021, share price achievement targets have been met for the 2020 grant. The 2019 grant vests over three years; provided, however, that no vesting will occur unless and until the volume-weighted average share closing price meets the applicable share price achievement goal on or before March 13, 2024. As of December 31, 2021, the applicable share price achievement targets for the 2019 award have not been met.
We used a Monte Carlo simulation valuation model to estimate the fair value of these awards on the grant date. We record compensation expense monthly using the accelerated recognition method over the longer of the explicit or derived service period of the award. The weighted-average grant date fair value per share of restricted shares with service and market conditions issued in 2021, 2020, and 2019, was $23.76, $19.22 and $28.90, respectively.
Valuation models require the input of highly subjective assumptions, including the expected volatility of the price of the underlying stock. We used the following assumptions to compute the weighted-average grant date fair market value of restricted stock with service and market conditions granted in 2021, 2020, and 2019:
| | | | | | | | | | | | | | | | | | | | |
| | 2021 | | 2020 | | 2019 |
Closing stock price on grant date | | $ | 42.03 | | | $ | 13.80 | | | $ | 33.10 | |
Risk free interest rate | | 1.1 | % | | 0.6 | % | | 2.2 | % |
Dividend yield | | — | % | | — | % | | — | % |
Estimated volatility | | 89.0 | % | | 83.9 | % | | 84.5 | % |
Expected life | | 5.5 years | | 6.0 years | | 4.8 years |
A summary of all activity relating to our restricted shares for the year ended December 31, 2021, is presented below:
| | | | | | | | | | | | | | |
| | | | Weighted Average Grant-Date Fair Value |
| | Shares | |
Restricted shares of common stock, beginning of period | | 362,399 | | | $ | 19.06 | |
Granted with service only condition | | 96,349 | | | $ | 37.49 | |
| | | | |
Granted with service and market conditions | | 89,226 | | | $ | 23.76 | |
Vested, service only condition | | (112,221) | | | $ | 16.63 | |
| | | | |
Forfeited, service only condition | | (24,287) | | | $ | 21.18 | |
Forfeited, service and market conditions | | (3,869) | | | $ | 23.38 | |
| | | | |
Restricted shares of common stock, end of period | | 407,597 | | | $ | 24.95 | |
Non-Qualified Stock Option Activity
We have not granted any non-qualified stock options to our employees since 2018. A summary of all stock option activity for the year ended December 31, 2021, is as follows:
| | | | | | | | | | | | | | | | | | | | | | | | | | |
| | Shares | | Weighted Average Exercise Price | | Aggregate Intrinsic Value1 | | Weighted Average Remaining Contractual Life |
Outstanding non-qualified stock options, beginning of period | | 296,046 | | | $31.66 | | | | |
Granted | | — | | | $— | | | | |
Exercised | | (8,651) | | | $10.30 | | | | |
Forfeited | | — | | | $— | | | | |
Expired | | (3,471) | | | $356.90 | | | | |
Outstanding non-qualified stock options, end of period | | 283,924 | | | $28.33 | | $4,088,429 | | 5.6 |
| | | | | | | | |
Vested or expected to vest, end of period | | 283,924 | | | $28.33 | | $4,088,429 | | 5.6 |
| | | | | | | | |
Exercisable non-qualified stock options, end of period | | 190,433 | | | $23.09 | | $3,739,708 | | 5.4 |
1The intrinsic value of a stock option is the amount by which the market value exceeds the exercise price as of the end of the period presented.
The total intrinsic value of exercised options to purchase stock during 2021, 2020 and 2019 was immaterial for each year.
Note 13— INCOME TAXES
We account for income taxes in accordance with ASC Topic 740, Income Taxes. This standard requires the recognition of deferred tax assets and liabilities for the tax effect of temporary differences between the financial statement and tax basis of recorded assets and liabilities at enacted tax rates in effect when the related taxes are expected to be settled or realized. We recognize income taxes in each of the tax jurisdictions where we conduct business. The effect on deferred tax assets and liabilities of a change in tax rates is recognized in income in the period that includes the enactment date.
A summary of the provision for income taxes is as follows (in thousands):
| | | | | | | | | | | | | | | | | | | | |
| | Year Ended December 31, |
| | 2021 | | 2020 | | 2019 |
Current portion of income tax expense (benefit): | | | | | | |
Federal | | $ | — | | | $ | (42) | | | $ | — | |
State | | 206 | | | 47 | | | 53 | |
Deferred portion of income tax expense: | | | | | | |
Federal | | (157,348) | | | — | | | — | |
State | | (51,727) | | | — | | | — | |
Total income tax (benefit) expense | | $ | (208,869) | | | $ | 5 | | | $ | 53 | |
A reconciliation of the federal statutory income tax rate of 21% to our effective rate is as follows (in thousands, except percentages):
| | | | | | | | | | | | | | | | | | | | |
| | Year Ended December 31, |
| | 2021 | | 2020 | | 2019 |
Federal taxes at statutory rate | | $ | 8,603 | | | $ | (5,701) | | | $ | 2,874 | |
Add: | | | | | | |
State taxes, net of federal benefit | | 1,278 | | | (1,316) | | | 1,245 | |
| | | | | | |
Change in valuation allowance | | (215,910) | | | 6,320 | | | (6,754) | |
PPP loan forgiveness | | (2,115) | | | — | | | — | |
Change in federal and state tax rates | | 138 | | | 3 | | | 2,322 | |
Percentage depletion | | (463) | | | — | | | (600) | |
Other | | (400) | | | 699 | | | 966 | |
Net (benefit) expense as calculated | | $ | (208,869) | | | $ | 5 | | | $ | 53 | |
| | | | | | |
Effective tax rate | | (509.9) | % | | — | % | | 0.4 | % |
Our effective tax rate for the years ended December 31, 2021, 2020, and 2019 differs from the U.S. federal statutory rate due to the change in valuation allowance.
As of December 31, 2021, and 2020, we had gross deferred tax assets of $211.1 million and $217.9 million, respectively. During the year ended December 31, 2021, our deferred tax assets decreased primarily from our usage of prior year net operating losses to offset current year income. Included in gross deferred tax assets as of December 31, 2021 were approximately $215.0 million of federal net operating loss carryforwards, which expire beginning in 2034, and approximately $279.3 million of state net operating loss carryforwards, the majority of which begin to expire in 2033. Also included are $1.9 million of federal research and development credits which begin to expire in 2031. The federal loss carryforward could be subject to examination by the tax authorities within three years after the carryforward is utilized, while the state net operating loss carryforwards could be subject to examination by the tax authorities generally within three and four years after the carryforward is utilized, depending on jurisdiction.
Significant components of our deferred tax assets and liabilities were as follows (in thousands):
| | | | | | | | | | | | | | |
| | December 31, |
| | 2021 | | 2020 |
| | |
Deferred tax assets (liabilities): | | | | |
Property, plant, equipment and mineral properties, net | | $ | 131,496 | | | $ | 133,720 | |
Federal and state net operating loss carryforwards | | 59,331 | | | 66,316 | |
Asset retirement obligation | | 6,900 | | | 6,070 | |
Deferred revenue | | 8,628 | | | 7,651 | |
Other | | 2,883 | | | 2,316 | |
Federal R&D credits | | 1,870 | | | 1,870 | |
| | | | |
| | | | |
| | | | |
| | | | |
Total deferred tax assets | | 211,108 | | | 217,943 | |
Valuation allowance | | (2,033) | | | (217,943) | |
Deferred tax asset, net | | $ | 209,075 | | | $ | — | |
In assessing the need for a valuation allowance, we consider whether it is more likely than not that some portion or all of the deferred tax assets will not be realized. We evaluate our ability to realize the tax benefits associated with deferred tax assets by analyzing the relative impact of all the available positive and negative evidence regarding our forecasted taxable income using both historical and projected future operating results, the reversal of existing taxable temporary differences, taxable income in prior carryback years, as permitted by regulation, and the availability of tax planning strategies. In determining how much of a valuation allowance to recognize we primarily consider our projections of future taxable income. All available evidence, both positive and negative, that may affect the realizability of deferred tax assets is identified and considered in determining the appropriate amount of the valuation allowance. The ultimate realization of deferred tax assets is dependent upon the generation of certain types of future taxable income during the periods in which those temporary differences become deductible. Assumptions of expected future taxable income are based primarily on prices and forecasted sales volumes which are subject to market volatility. In making this assessment, we consider the scheduled reversal of deferred tax liabilities, our ability to carry back the deferred tax asset, projected future taxable income, and tax planning strategies.
As of December 31, 2021, we were in a cumulative three-year income position. The cumulative three-year income position is significant positive evidence when evaluating the realizability of our deferred tax assets. Additionally, industry trends and forecasts as well as internal forecasts of future business show sustained amounts of taxable income. Thus, we have concluded that it is more likely than not that most of our $211.1 million of deferred tax assets will be realized. We continue to maintain a valuation allowance of $2.0 million against our deferred tax assets related to federal and state R&D credits as we forecast these will expire before being used. As of December 31, 2020, we had a full valuation allowance against our deferred tax assets. During 2021, our valuation allowance decreased $215.9 million as we have concluded that we will more likely than not realize most of our deferred tax assets. Our deferred tax assets, net of the valuation allowance at December 31, 2021, and 2020, was $209.1 million and zero, respectively
The estimated statutory income tax rates that are applied to our current and deferred income tax calculations are impacted most significantly by the tax jurisdictions in which we conduct business. Changing business conditions for normal business transactions and operations, as well as changes to state tax rates and apportionment laws, potentially alter the apportionment of income among the states for income tax purposes. These changes to apportionment laws result in changes in the calculation of our current and deferred income taxes, including the valuation of our deferred tax assets and liabilities. The effects of any such changes are recorded in the period of the adjustment. Such adjustments can increase or decrease the net deferred tax asset on the balance sheet and impact the corresponding deferred tax benefit or deferred tax expense on the statement of operations.
A decrease of our state tax rate decreases the value of its deferred tax asset, resulting in additional deferred tax expense being recorded on the income statement. Conversely, an increase in our state income tax rate would increase the value of the deferred tax asset, resulting in an increase in our deferred tax benefit. Because of the magnitude of the temporary differences between our book and tax basis in the assets, relatively small changes in the state tax rate may have a pronounced impact on the value of our net deferred tax asset.
Each quarter we evaluate the need for a liability for uncertain tax positions. At December 31, 2021, and 2020, we had no items that required disclosure in accordance with FASB guidance on accounting for uncertainty in income taxes.
We operate, and accordingly file income tax returns, in the U.S. federal jurisdiction and various U.S. state jurisdictions. With few exceptions, we are no longer subject to income tax audits that could result in an assessment for years prior to 2018.
Note 14— COMMITMENTS AND CONTINGENCIES
Reclamation Deposits and Surety Bonds—As of December 31, 2021, and 2020, we had $23.0 million and $22.3 million, respectively, of security placed principally with the State of Utah and the Bureau of Land Management for eventual reclamation of its various facilities. Of this total requirement, as of December 31, 2021, and 2020, $0.5 million consisted of long-term restricted cash deposits reflected in "Other" long-term assets on the balance sheet, and $22.5 million and $21.8 million, respectively, was secured by surety bonds issued by an insurer. The surety bonds are held in place by an annual fee paid to the issuer.
We may be required to post additional security to fund future reclamation obligations as reclamation plans are updated or as governmental entities change requirements.
Legal—We are subject to claims and legal actions in the ordinary course of business. We expense legal costs as incurred. While there are uncertainties in predicting the outcome of any claim or legal action, except as noted below, we believe the ultimate resolution of these claims or actions is not reasonably likely to have a material adverse effect on our financial condition, results of operations, or cash flows.
Mosaic Settlement
In March 2020, we entered into a definitive settlement agreement with Mosaic Potash Carlsbad Inc. ("Mosaic") related to a compliant originally brought against us and Steve Gamble in February 2015. Mr. Gamble is a former employee of Intrepid and Mosaic. Under the terms of the settlement agreement, we paid Mosaic an aggregate of $10 million in May 2020 to dismiss all current and future claims arising from this matter against us and the matter is now closed.
Water Rights
In February 2019, Pecos Valley Artesian Conservancy District, Carlsbad Irrigation District, and Otis Mutual Domestic Water Consumers & Sewage Works Association (together, the "Protestants") filed an expedited inter se proceeding against us, Henry McDonald, Select Energy Services, LLC d/b/a Gregory Rockhouse Ranch, and Vision Resources, Inc. in the Fifth Judicial District Court for the County of Chaves in the State of New Mexico. This court serves as the adjudication court for the Pecos Stream System, which includes the Pecos River. The Protestants challenged the validity of our Pecos River water rights, representing approximately 20,000 acre feet per year. A virtual trial began on December 8, 2020, and concluded on December 18, 2020.
In August 2021, the adjudication court issued its rulings on the validity of our Pecos River water rights. The adjudication court found that our predecessors had forfeited all but approximately 5,800 feet of water per year, and further ruled that, of the remaining 5,800 acre feet of water that had not been forfeited, all but 150 acre feet of water had been abandoned prior to 2017. Following briefing on specific issues, requested by the adjudication court, the adjudication court withdrew its initial findings of fact and conclusions of law and entered amended findings of fact and conclusions of law on December 17, 2021. The order based on these findings of fact and conclusions of law has not yet been entered, but we expect the adjudication court to enter an order based on its findings of fact and conclusions of law in the near future. We anticipate filing an appeal of the adjudication court's ruling on the validity of our water rights.
In 2017 and 2018 the New Mexico Office of the State Engineer (“OSE”) had granted us preliminary authorizations to sell approximately 5,700 acre feet of water per year from our Pecos River water rights. The preliminary authorizations allowed for water sales to begin immediately, subject to repayment if the underlying water rights are ultimately found to be invalid. If the adjudication court enters, as expected, an order based on its amended findings of fact and conclusion of law discussed above, and our expected appeal of the adjudication court's ruling is unsuccessful, we may have to repay for the water we sold under the preliminary authorizations. Repayment of this water can be up to two times the amount of water removed from the river. Repayment is customarily made in-kind over a period of time but can take other forms including cash repayment. If we are not able to repay in-kind due to the lack of remaining water rights or logistical constraints, we may need to purchase water to meet this repayment or be subject to a cash repayment. We cannot reasonably estimate the potential volume, timing, or form of repayment, if any, and have not recorded a loss contingency in our statement of operations related to this legal matter.
In March 2021, we received notice from a customer of a default under the terms of a long-term sales contract because we have not been able to deliver water to diversion points specified in the contract. We had relied primarily upon our Pecos River water rights to deliver water under this contract, the majority of which are currently unavailable due to the factors discussed above. Under this contract we have received quarterly installments of approximately $3.9 million for the future delivery of water to the customer. In April 2021, we agreed to suspend the second quarter and future quarterly installments due from the customer as we continue to work to resolve the issue. In December 2021, we amended our long-term sales agreement with the customer due to our inability to deliver water. In the amendment, we agreed to suspend all rights and obligations of both parties under the agreement until July 1, 2022. During the suspension period, we have no obligation to deliver water and our customer has no obligation to take water, if available, or make quarterly payments to us. After the suspension period, our customer has the right to terminate the agreement for any reason with thirty days written notice at which time we would be required to repay any outstanding balance for undelivered water. We are continuing to work with the customer to resolve this issue. If we are not able to resolve the issue, we may have to repay the $32.5 million outstanding contract liability we have with this customer as of December 31, 2021. See Note 11—Revenue above for additional information.
In August 2021, NGL Energy Partners (NGL), our partner in the Joint Marketing Agreement (“JMA”) that was entered into in May 2019, filed suit against us alleging, amongst other items, we overcharged the JMA for various operating costs and that we used third party water to service certain fracs when JMA water should have been used in those fracs. NGL is seeking to immediately terminate the JMA as well as compensatory damages. We are vigorously defending against the lawsuit. Because this matter is at an early stage, we are unable to reasonably estimate the potential amount of loss, if any.
We are subject to other claims and legal actions in the ordinary course of business. Legal costs are expensed as incurred. While there are uncertainties in predicting the outcome of any claim or legal action, we believe that the ultimate resolution of these other claims or actions is not reasonably likely to have a material adverse effect on our financial condition, results of operations, or cash flows.
Note 15— FAIR VALUE MEASUREMENTS
We measure our financial assets and liabilities in accordance with Accounting Standards Codification ("ASC") Topic 820, Fair Value Measurements and Disclosures. ASC Topic 820 defines fair value as the price that would be received to sell an asset or paid to transfer a liability (an exit price) in an orderly transaction between market participants at the measurement date. The topic establishes market or observable inputs as the preferred sources of values, followed by assumptions based on hypothetical transactions in the absence of market inputs. The topic also establishes a hierarchy for grouping these assets and liabilities based upon the lowest level of input that is significant to the fair value measurement. The definition of each input is described below:
•Level 1—Quoted prices in active markets for identical assets and liabilities
•Level 2—Quoted prices in active markets for similar assets and liabilities, quoted prices for identical or similar instruments in markets that are not active, and model‑derived valuations whose inputs are observable or whose significant value drivers are observable
•Level 3—Significant inputs to the valuation model that are unobservable
As of December 31, 2021, and 2020, our cash consisted of bank deposits. Other financial assets and liabilities including, accounts receivable, refundable income taxes, accounts payable, accrued liabilities, and advances on credit facility are carried at cost which approximates fair value because of the short-term nature of these instruments.
In May of 2020, we acquired a non-controlling interest in W.D. Von Gonten Laboratories ("WDVGL") for $3.5 million. This investment is an equity investment without a readily determinable fair value and is recorded at cost with adjustments for observable changes in prices resulting from orderly transactions for the identical or a similar investment of the same issuer, or impairment (a Level 3 input), and is included in "Other assets, net" on the Consolidated Balance Sheets. We did not record any adjustments to the $3.5 million carrying value of the investment during 2021 or 2020.
As of December 31, 2020, the carrying value and the estimated fair value of our outstanding Notes was $15.0 million. The fair value of our Notes was estimated using a discounted cash flow analysis based on current borrowing rates for debt with similar remaining maturities and ratings (a Level 2 input) and is designed to approximate the amount at which the instruments could be exchanged in an arm's-length transaction between knowledgeable willing parties.
Note 16— EMPLOYEE BENEFITS
401(k) Plan
We maintain a savings plan qualified under Internal Revenue Code Sections 401(a) and 401(k). The 401(k) Plan is available to eligible employees of our consolidated entities. Employees may contribute amounts as allowed by the U.S. Internal Revenue Service to the 401(k) Plan (subject to certain restrictions) in before-tax contributions. In January 2018, we increased the matching contributions on a dollar-for-dollar basis up to a maximum of 5% of the employee's base compensation. Our contributions to the 401(k) Plan in the following periods were (in thousands):
| | | | | | | | |
| | Contributions |
Year Ended December 31, 2021 | | $ | 1,633 | |
Year Ended December 31, 2020 | | $ | 1,569 | |
Year Ended December 31, 2019 | | $ | 1,522 | |
Note 17— BUSINESS SEGMENTS
Our operations are organized into three segments: potash, Trio®, and oilfield solutions. The reportable segments are determined by management based on several factors including the types of products and services sold, production processes, markets served and the financial information available for our chief operating decision maker. We evaluate performance based on the gross margins of the respective business segments and do not allocate corporate selling and administrative expenses, among others, to the respective segments. Intersegment sales prices are market-based and are eliminated in the "Other" column. Information for each segment is provided in the tables that follow (in thousands).
| | | | | | | | | | | | | | | | | | | | | | | | | | | | | | | | |
Year Ended December 31, 2021 | | Potash | | Trio® | | Oilfield Solutions | | Other | | Consolidated |
Sales1 | | $ | 151,751 | | | $ | 96,058 | | | $ | 22,770 | | | $ | (247) | | | $ | 270,332 | |
Less: Freight costs | | 17,483 | | | 20,656 | | | — | | | (247) | | | 37,892 | |
Warehousing and handling costs | | 5,169 | | | 4,113 | | | — | | | — | | | 9,282 | |
Cost of goods sold | | 87,281 | | | 54,847 | | | 19,293 | | | — | | | 161,421 | |
| | | | | | | | | | |
Costs associated with abnormal production | | 5,973 | | | — | | | — | | | — | | | 5,973 | |
Gross Margin | | $ | 35,845 | | | $ | 16,442 | | | $ | 3,477 | | | $ | — | | | $ | 55,764 | |
Depreciation, depletion, and amortization2 incurred | | $ | 26,828 | | | $ | 5,477 | | | $ | 2,996 | | | $ | 656 | | | $ | 35,957 | |
| | | | | | | | | | |
Year Ended December 31, 2020 | | Potash | | Trio® | | Oilfield Solutions | | Other | | Consolidated |
Sales1 | | $ | 108,060 | | | $ | 70,287 | | | $ | 18,929 | | | $ | (322) | | | $ | 196,954 | |
Less: Freight costs | | 17,026 | | | 20,431 | | | — | | | (322) | | | 37,135 | |
Warehousing and handling costs | | 4,857 | | | 4,574 | | | — | | | — | | | 9,431 | |
Cost of goods sold | | 73,496 | | | 50,902 | | | 11,445 | | | — | | | 135,843 | |
Lower of cost or NRV inventory adjustments | | 1,130 | | | 2,885 | | | — | | | — | | | 4,015 | |
| | | | | | | | | | |
Gross Margin (Deficit) | | $ | 11,551 | | | $ | (8,505) | | | $ | 7,484 | | | $ | — | | | $ | 10,530 | |
Depreciation, depletion, and amortization incurred2 | | $ | 26,536 | | | $ | 6,068 | | | $ | 2,663 | | | $ | 843 | | | $ | 36,110 | |
| | | | | | | | | | |
Year Ended December 31, 2019 | | Potash | | Trio® | | Oilfield Solutions | | Other | | Consolidated |
Sales1 | | $ | 124,648 | | | $ | 69,551 | | | $ | 27,894 | | | $ | (2,018) | | | $ | 220,075 | |
Less: Freight costs | | 18,715 | | | 20,514 | | | 936 | | | (109) | | | 40,056 | |
Warehousing and handling costs | | 4,745 | | | 3,876 | | | — | | | — | | | 8,621 | |
Cost of goods sold | | 73,401 | | | 42,251 | | | 12,367 | | | (1,909) | | | 126,110 | |
Lower of cost or NRV inventory adjustments | | — | | | 1,810 | | | — | | | — | | | 1,810 | |
| | | | | | | | | | |
Gross Margin | | $ | 27,787 | | | $ | 1,100 | | | $ | 14,591 | | | $ | — | | | $ | 43,478 | |
Depreciation, depletion, and amortization incurred2 | | $ | 25,796 | | | $ | 6,163 | | | $ | 1,566 | | | $ | 810 | | | $ | 34,335 | |
1 Segment sales include the sales of byproducts generated during the production of potash and Trio®.
2 Depreciation, depletion, and amortization incurred for potash and Trio® excludes depreciation, depletion, and amortization absorbed in or (relieved from) inventory.
Total assets are not presented for each reportable segment as they are not reviewed by, nor otherwise regularly provided to, the chief operating decision maker.
Note 18— CONCENTRATION OF CREDIT RISK
Credit risk represents the loss that would be recognized at the reporting date if counterparties failed completely to perform as contracted. Concentrations of credit risk, whether on- or off-balance sheet, that arise from financial instruments exist for counterparties when they have similar economic characteristics that would cause their ability to meet contractual obligations to be similarly affected by changes in economic or other conditions.
Our products are marketed for sale into three primary markets. These markets are the agricultural market as a fertilizer, the industrial market as a component in drilling fluids for oil and gas exploration, and the animal feed market as a
nutrient. Credit risks associated with the collection of accounts receivable are primarily related to the impact of external factors on our customers. Our customers are distributors and end-users whose credit worthiness and ability to meet their payment obligations will be affected by factors in their industries and markets. Those factors include soil nutrient levels, crop prices, weather, the type of crops planted, changes in diets, growth in population, the amount of land under cultivation, fuel prices and consumption, oil and gas drilling and completion activity, the demand for biofuels, government policy, and the relative value of currencies. Our industrial sales are significantly influenced by oil and gas drilling activity.
In 2021, 2020, and 2019, no customer accounted for more than 10% of our sales. Because of the size of our company compared to the overall size of the North American market and the regional demands for our products, we believe that a decline in a specific customer's purchases would not have a material adverse long-term effect on our financial results.
In each of the last three years ended December 31, 2021, 2020, and 2019, 97%, 97%, and 94%, respectively, of our total sales were sold to customers located in the United States. All of our long-lived assets are located in the United States.
We maintain cash accounts with several financial institutions. At times, the balances in the accounts may exceed the $250,000 balance insured by the Federal Deposit Insurance Corporation.
Note 19— FINANCIAL INFORMATION FOR SUBSIDIARY GUARANTORS
OF POSSIBLE FUTURE PUBLIC DEBT
Intrepid Potash, Inc., as the parent company, has no independent assets or operations, and operations are conducted solely through its subsidiaries. Cash generated from operations is held at the parent company level as cash on hand and short- and long-term investments. Cash on hand totaled $36.5 million and $19.5 million at December 31, 2021, and 2020, respectively. In the event that one or more of our wholly-owned operating subsidiaries guarantee public debt securities in the future, those guarantees will be full and unconditional and will constitute the joint and several obligations of the subsidiary guarantors. Our other subsidiaries are minor. There are no restrictions on our ability to obtain cash dividends or other distributions of funds from the subsidiary guarantors, except those imposed by applicable law.
Note 20— SUBSEQUENT EVENT
In February of 2022, our Board of Directors approved a $35 million share repurchase program. Under the share repurchase program, we may repurchase shares from time to time in the open market or in privately negotiated transactions. The timing, volume and nature of share repurchases, if any, will be at our sole discretion and will be dependent on market conditions, liquidity, applicable securities laws, and other factors. We may suspend or discontinue the share repurchase program at any time.
SCHEDULE II - VALUATION AND QUALIFYING ACCOUNTS
| | | | | | | | | | | | | | | | | | | | | | | | | | |
| | (In thousands) |
Description | | Balance at Beginning of Year | | Charged to Costs and Expenses | | Deductions | | Balance at End of Year |
| | | | | | | | |
| | | | | | | | |
| | | | | | | | |
| | | | | | | | |
| | | | | | | | |
| | | | | | | | |
| | | | | | | | |
| | | | | | | | |
| | | | | | | | |
| | | | | | | | |
| | | | | | | | |
| | | | | | | | |
| | | | | | | | |
| | | | | | | | |
For the Year Ended December 31, 2019 | | | | | | | | |
Allowances deducted from assets | | | | | | | | |
Deferred tax assets - valuation allowance | | $ | 218,377 | | | $ | — | | | $ | (6,754) | | | $ | 211,623 | |
Reserve for parts inventory obsolescence | | 1,743 | | | — | | | (1,127) | | | 616 | |
Allowance for doubtful accounts and other receivables | | 465 | | | 75 | | | (60) | | | 480 | |
Total allowances deducted from assets | | $ | 220,585 | | | $ | 75 | | | $ | (7,941) | | | $ | 212,719 | |
| | | | | | | | |
For the Year Ended December 31, 2020 | | | | | | | | |
Allowances deducted from assets | | | | | | | | |
Deferred tax assets - valuation allowance | | 211,623 | | | 6,320 | | | — | | | 217,943 | |
Reserve for parts inventory obsolescence | | 616 | | | 492 | | | (58) | | | 1,050 | |
Allowance for doubtful accounts and other receivables | | 480 | | | 275 | | | (200) | | | 555 | |
Total allowances deducted from assets | | $ | 212,719 | | | $ | 7,087 | | | $ | (258) | | | $ | 219,548 | |
| | | | | | | | |
For the Year Ended December 31, 2021 | | | | | | | | |
Allowances deducted from assets | | | | | | | | |
Deferred tax assets - valuation allowance | | 217,943 | | | — | | | (215,910) | | | 2,033 | |
Reserve for parts inventory obsolescence | | 1,050 | | | 2,108 | | | — | | | 3,158 | |
Allowance for doubtful accounts and other receivables | | 555 | | | — | | | — | | | 555 | |
Total allowances deducted from assets | | $ | 219,548 | | | $ | 2,108 | | | $ | (215,910) | | | $ | 5,746 | |
ITEM 9.CHANGES IN AND DISAGREEMENTS WITH ACCOUNTANTS ON ACCOUNTING
AND FINANCIAL DISCLOSURE
None.
ITEM 9A.CONTROLS AND PROCEDURES
Evaluation of Disclosure Controls and Procedures
We maintain "disclosure controls and procedures." Our disclosure controls and procedures are designed to ensure that information required to be disclosed by us in reports that we file or submit under the Exchange Act is recorded, processed, summarized, and reported within the time periods specified in SEC rules and forms. Our disclosure controls and procedures are also designed to ensure that this information is accumulated and communicated to our management, including our principal executive officer and principal financial officer, as appropriate, to allow timely decisions regarding required disclosure. Under the supervision and with the participation of our management, including our principal executive officer and principal financial officer, we conducted an evaluation of our disclosure controls and procedures as of December 31, 2021. Based on this evaluation, our principal executive officer and principal financial officer have concluded that our disclosure controls and procedures were effective as of December 31, 2021, at the reasonable assurance level.
Management's Report on Internal Control over Financial Reporting
Our management is responsible for establishing and maintaining adequate "internal control over financial reporting." Our internal control over financial reporting is a process designed to provide reasonable assurance regarding the reliability of financial reporting and the preparation of financial statements for external purposes in accordance with GAAP. Under the supervision and with the participation of our management, including our principal executive officer and principal financial officer, we conducted an evaluation of the effectiveness of our internal control over financial reporting as of December 31,
2021, based on the criteria established in Internal Control—Integrated Framework issued by the Committee of Sponsoring Organizations of the Treadway Commission (COSO) in 2013.
Based on the results of our evaluation, our management concluded that our internal control over financial reporting was effective as of December 31, 2021.
The effectiveness of our internal control over financial reporting as of December 31, 2021, has been audited by KPMG LLP, our independent registered public accounting firm, as stated in their report which appears herein.
Changes in Internal Control over Financial Reporting
There were no changes in our internal control over financial reporting that occurred during the three months ended December 31, 2021, that materially affected, or are reasonably likely to materially affect, our internal control over financial reporting.
Inherent Limitations on Effectiveness of Controls
Our management, including our principal executive officer and principal financial officer, do not expect that our disclosure controls or our internal control over financial reporting will prevent all errors and all fraud. A control system, no matter how well conceived and operated, can provide only reasonable, not absolute, assurance that the objectives of the control system are met. Further, the design of a control system must reflect the fact that there are resource constraints, and the benefits of controls must be considered relative to their costs. Because of the inherent limitations in all control systems, no evaluation of controls can provide absolute assurance that all control issues and instances of fraud, if any, within Intrepid have been detected. These inherent limitations include the realities that judgments in decision-making can be faulty, and that breakdowns can occur because of a simple error or mistake. Additionally, controls can be circumvented by the individual acts of some persons, by collusion of two or more people, or by management override of the controls. The design of any system of controls also is based in part upon certain assumptions about the likelihood of future events, and there can be no assurance that any design will succeed in achieving its stated goals under all potential future conditions. Over time, controls may become inadequate because of changes in conditions, or the degree of compliance with policies or procedures may deteriorate. Because of the inherent limitations in a cost-effective control system, misstatements due to error or fraud may occur and not be detected.
ITEM 9B.OTHER INFORMATION
Not applicable.
ITEM 9C.DISCLOSURE REGARDING FOREIGN JURISDICTIONS THAT PREVENT INSPECTIONS
None
PART III
ITEM 10.DIRECTORS, EXECUTIVE OFFICERS AND CORPORATE GOVERNANCE
Biographical information about our executive officers is set forth in "Item 1. Business—Executive Officers." Other information required by this item will be included in the proxy statement for our 2022 annual stockholders' meeting and is incorporated by reference into this Annual Report on Form 10-K.
ITEM 11.EXECUTIVE COMPENSATION
Information required by this item will be included in the proxy statement for our 2022 annual stockholders' meeting and is incorporated by reference into this Annual Report on Form 10-K.
ITEM 12.SECURITY OWNERSHIP OF CERTAIN BENEFICIAL OWNERS AND MANAGEMENT AND RELATED STOCKHOLDER MATTERS
Information required by this item will be included in the proxy statement for our 2022 annual stockholders' meeting and is incorporated by reference into this Annual Report on Form 10-K.
ITEM 13.CERTAIN RELATIONSHIPS AND RELATED TRANSACTIONS,
AND DIRECTOR INDEPENDENCE
Information required by this item will be included in the proxy statement for our 2022 annual stockholders' meeting and is incorporated by reference into this Annual Report on Form 10-K.
ITEM 14.PRINCIPAL ACCOUNTANT FEES AND SERVICES
Information required by this item will be included in the proxy statement for our 2022 annual stockholders' meeting and is incorporated by reference into this Annual Report on Form 10-K.
PART IV
ITEM 15.EXHIBITS, FINANCIAL STATEMENT SCHEDULES
(a) Financial Statements, Financial Statement Schedules and Exhibits
The following are filed as a part of this Annual Report on Form 10-K:
(1) Financial Statements
Management's Report on Internal Control over Financial Reporting
Report of Independent Registered Accounting Firm (PCAOB ID 185)
Consolidated Balance Sheets as of December 31, 2021, and 2020
Consolidated Statements of Operations for the years ended December 31, 2021, 2020, and 2019
Consolidated Statements of Stockholders' Equity for the years ended December 31, 2021, 2020, and 2019
Consolidated Statements of Cash Flows for the years ended December 31, 2021, 2020, and 2019
Notes to Consolidated Financial Statements
(2) Financial Statement Schedule
| | | | | | | | |
Schedule | | Schedule Description |
Schedule II | | Schedule of Valuation and Qualifying Accounts |
Schedule II is filed as part of this Annual Report on Form 10-K and is set forth immediately following the Notes to the Consolidated Financial Statements referred to above. All other financial statement schedules have been omitted because they are not required, are not applicable, or the information is included in the consolidated financial statements or notes thereto.
(3) Exhibits
The following exhibits are filed or incorporated by reference in this report:
| | | | | | | | | | | | | | | | | |
| | | | Incorporated by Reference from the Below-Listed Form (Each Filed under SEC File Number 001-34025) |
Exhibit Number | | Exhibit Description | | Form | Filing Date |
| | Restated Certificate of Incorporation of Intrepid Potash, Inc. | | 8-K | April 25, 2008 |
| | Certificate of Amendment to Restated Certificate of Incorporation of Intrepid Potash, Inc. | | 8-K | May 26, 2016 |
| | Certificate of Amendment to Restated Certificate of Incorporation of Intrepid Potash, Inc. | | 8-K | August 14, 2020 |
| | Amended and Restated Bylaws of Intrepid Potash, Inc. | | 8-K | June 25, 2015 |
| | Description of Registrant's Securities | | 10-K | March 3, 2020 |
| | Form of Indemnification Agreement with each director and officer | | 8-K | April 25, 2008 |
| | Director Designation and Voting Agreement, dated as of April 25, 2008, by and among Intrepid Potash, Inc., Harvey Operating and Production Company, Intrepid Production Corporation, and Potash Acquisition, LLC | | 8-K | May 1, 2008 |
| | Registration Rights Agreement, dated as of April 25, 2008, by and among Intrepid Potash, Inc., Harvey Operating & Production Company, Intrepid Production Corporation, and Potash Acquisition, LLC | | 8-K | May 1, 2008 |
| | Acknowledgment and Relinquishment, dated as of December 19, 2011, by and among Intrepid Potash, Inc., Harvey Operating and Production Company, Intrepid Production Corporation, and Potash Acquisition, LLC | | 10-K | February 16, 2012 |
| | | | | | | | | | | | | | | | | |
| | Amended and Restated Credit Agreement, dated as of August 1, 2019, by and among Intrepid Potash, Inc., the subsidiaries party thereto, Bank of Montreal, as administrative agent, swing line lender, lead arranger, and book runner, and the lenders party thereto. | | 8-K | August 1, 2019 |
| | First Amended and Restated Credit Agreement, dated as of April 17, 2020, by and among Intrepid Potash, Inc., the subsidiaries party thereto, Bank of Montreal, as administrative agent, swing line lender, lead arranger, and book runner, and the lenders party thereto. | | 8-K | April 23, 2020 |
| | Amended and Restated Employment Agreement, dated as of May 19, 2010, by and between Intrepid Potash, Inc. and Robert P. Jornayvaz III+ | | 8-K | May 19, 2010 |
| | Amendment to Employment Agreement, dated February 23, 2011, by and between Intrepid Potash, Inc. and Robert P. Jornayvaz III+ | | 8-K | March 1, 2011 |
| | Second Amendment to Employment Agreement, dated as of February 14, 2013, by and between Intrepid Potash, Inc. and Robert P. Jornayvaz III+ | | 8-K | February 19, 2013 |
| | Third Amendment to Employment Agreement, dated as of March 22, 2016, by and between Intrepid Potash, Inc. and Robert P. Jornayvaz III+ | | 8-K | March 23, 2016 |
| | Fourth Amendment to Employment Agreement, dated as of March 12, 2019, by and between Intrepid Potash, Inc. and Robert P. Jornayvaz III+ | | 8-K | March 15, 2019 |
| | Amended and Restated Employment Agreement, dated as of May 19, 2010, by and between Intrepid Potash, Inc. and Hugh E. Harvey, Jr.+ | | 8-K | May 19, 2010 |
| | Intrepid Potash, Inc. Amended and Restated Equity Incentive Plan+ | | 8-K | May 24, 2019 |
| | Form of Restricted Stock Agreement under Intrepid Potash, Inc. Amended and Restated Equity Incentive Plan+ | | 10-K | March 2, 2021 |
| | Form of Stock Option Agreement under Intrepid Potash, Inc. Amended and Restated Equity Incentive Plan+ | | 10-K | March 2, 2021 |
| | Intrepid Potash, Inc. Amended and Restated Short-Term Incentive Plan+ | | 8-K | May 26, 2016 |
| | Form of Change-of-Control Severance Agreement with Robert P. Jornayvaz III and Hugh E. Harvey, Jr.+ | | 10-Q | November 3, 2011 |
| | Form of Change-in-Control Severance Agreement with Margaret E. McCandless and Mark A. McDonald+ | | 10-K | March 12, 2019 |
| | Form of Noncompete Agreement with executives other than Robert P. Jornayvaz III+ | | 10-K | February 28, 2017 |
| | Form of Retention Agreement+ | | 10-K | March 12, 2019 |
| | Aircraft Dry Lease, dated as of January 9, 2009, by and between Intrepid Potash, Inc. and Intrepid Production Holdings LLC | | 8-K | January 12, 2009 |
| | First Amendment to Aircraft Dry Lease, dated as of September 1, 2014, by and between Intrepid Potash, Inc. and Intrepid Production Holdings LLC | | 8-K | August 18, 2014 |
| | Aircraft Dry Lease, dated as of September 1, 2014, by and between Intrepid Potash, Inc. and Odyssey Adventures, LLC | | 8-K | August 18, 2014 |
| | List of Subsidiaries | | * | |
| | Consent of KPMG LLP | | * | |
| | Consent of Agapito Associates, Inc. | | * | |
| | Certification of Principal Executive Officer pursuant to Exchange Act Rules 13a-14(a) and 15d-14(a) | | * | |
| | Certification of Principal Financial Officer pursuant to Exchange Act Rules 13a-14(a) and 15d-14(a) | | * | |
| | Certification of Principal Executive Officer pursuant to 18 U.S.C. Section 1350, as adopted pursuant to Section 906 of the Sarbanes-Oxley Act of 2002 | | ** | |
| | Certification of Principal Financial Officer pursuant to 18 U.S.C. Section 1350, as adopted pursuant to Section 906 of the Sarbanes-Oxley Act of 2002 | | ** | |
| | Mine Safety Disclosure Exhibit | | * | |
| | Technical Report Summary for Intrepid Potash - New Mexico | | | |
| | Technical Report Summary for Intrepid Potash - Moab | | | |
| | | | | | | | | | | | | | | | | |
| | Technical Report Summary for Intrepid Potash - Wendover | | | |
| | Transition Services Agreement, dated as of April 25, 2008, by and between Intrepid Potash, Inc., Intrepid Oil & Gas, LLC, and Intrepid Potash-Moab, LLC | | 8-K | May 1, 2008 |
| | Extension and Amendment to Transition Services Agreement dated July 14, 2009, to be effective as of April 25, 2009, between Intrepid Potash, Inc. and Intrepid Oil & Gas, LLC | | 10-Q | August 7, 2009 |
| | Third Amendment to Transition Services Agreement dated March 26, 2010, between Intrepid Potash, Inc. and Intrepid Oil & Gas, LLC | | 10-Q | May 5, 2010 |
| | Fourth Amendment to Transition Services Agreement dated March 25, 2011, between Intrepid Potash, Inc. and Intrepid Oil and Gas, LLC | | 10-Q | May 5, 2011 |
| | Sixth Amendment to Transition Services Agreement dated April 3, 2013, between Intrepid Potash, Inc. and Intrepid Oil & Gas, LLC | | 10-Q | May 2, 2013 |
| | Seventh Amendment to Transition Services Agreement dated March 24, 2015, between Intrepid Potash, Inc. and Intrepid Oil & Gas, LLC | | 10-Q
| April 28, 2015 |
| | Eighth Amendment to Transition Services Agreement dated March 22, 2017, between Intrepid Potash, Inc. and Intrepid Oil & Gas, LLC | | 10-Q | May 2, 2017 |
| | Ninth Amendment to Transition Services Agreement dated February 20, 2019, between Intrepid Potash, Inc. and Intrepid Oil & Gas, LLC. | | 10-K | March 12, 2019 |
101.INS | | XBRL Instance Document | | * | |
101.SCH | | XBRL Taxonomy Extension Schema | | * | |
101.CAL | | XBRL Extension Calculation Linkbase | | * | |
101.DEF | | XBRL Extension Definition Linkbase | | * | |
101.LAB | | XBRL Extension Label Linkbase | | * | |
101.PRE | | XBRL Extension Presentation Linkbase | | * | |
104 | | Cover Page Interactive Date File (formatted as inline XBRL with applicable taxonomy extension information contain in Exhibits 101. | | | |
* Filed herewith
** Furnished herewith
+ Management contract or compensatory plan or arrangement
ITEM 16.FORM 10-K SUMMARY
Not applicable.
SIGNATURES
Pursuant to the requirements of Section 13 or 15(d) of the Securities Exchange Act of 1934, the registrant has duly caused this report to be signed on its behalf by the undersigned, thereunto duly authorized.
| | | | | | | | |
| | INTREPID POTASH, INC. (Registrant) |
| | |
March 8, 2022 | | /s/ Robert P. Jornayvaz III |
| | Robert P. Jornayvaz III - Executive Chairman of the Board and Chief Executive Officer (Principal Executive Officer and Duly Authorized Officer) |
Pursuant to the requirements of the Securities Exchange Act of 1934, this report has been signed below by the following persons on behalf of the registrant and in the capacities and on the dates indicated.
| | | | | | | | | | | | | | |
Signature | | Title | | Date |
| | | | |
/s/ Robert P. Jornayvaz III | | Executive Chairman of the Board and Chief Executive Officer | | March 8, 2022 |
Robert P. Jornayvaz III | | | | |
| | | | |
/s/ Matthew D. Preston | | Chief Financial Officer (Principal Financial Officer) | | March 8, 2022 |
Matthew D. Preston | | | | |
| | | | |
/s/ Chris A. Elliott | | Director | | March 8, 2022 |
Chris A. Elliott | | | | |
| | | | |
/s/ Lori A. Lancaster | | Director | | March 8, 2022 |
Lori A. Lancaster | | | | |
| | | | |
/s/ Mary E. McBride | | Director | | March 8, 2022 |
Mary E. McBride | | | | |
| | | | |
/s/ Barth E. Whitham | | Lead Director | | March 8, 2022 |
Barth E. Whitham | | | | |